Pubblicazioni
Nessuna pubblicazione presente
News
PRIMO PIANO
NEWS
SALUTE E SICUREZZA SUL LAVORO
26/06/2025
Sistemi innovativi e sicurezza macchine per la lotta al "defeating"
Nonostante i progressi tecnologici e in ambito di sensibilizzazione di aziende e lavoratori sull’importanza della sicurezza negli ambienti di lavoro, ancora oggi si registrano numerosi inf ...
NEWS
SALUTE E SICUREZZA SUL LAVORO
12/06/2025
Il Piano Triennale INAIL 2025-2027: una strategia integrata per salute, sicurezza e sostenibilità del lavoro
Con la delibera n.7 del 13 maggio 2025 del Consiglio di Indirizzo e Vigilanza, L’INAIL ha recentemente approvato il Piano triennale per la prevenzione 2025-2027, documento cardine che orienter&a ...
NEWS
SALUTE E SICUREZZA SUL LAVORO
29/05/2025
Sicurezza sul lavoro: ecco perché il preposto non può “chiudere gli occhi”
Nel contesto della salute e sicurezza sul lavoro, la figura del preposto riveste un ruolo fondamentale e autonomo, anche quando si trova a operare sotto la direzione di superiori gerarchici. Un esempi ...
NEWS
SALUTE E SICUREZZA SUL LAVORO
15/05/2025
Sicurezza sul lavoro: i chiarimenti dell’INL su macchine e attrezzature
Il 18 marzo 2025, l’Ispettorato Nazionale del Lavoro (INL) ha pubblicato la Circolare n. 2668 per fornire importanti chiarimenti operativi in materia di sicurezza, in risposta alle numerose rich ...
NEWS
SALUTE E SICUREZZA SUL LAVORO
24/04/2025
Valutazione del rischio da stress termico: strumenti e metodi per una sicurezza efficace sul lavoro
Lo stress termico rappresenta un rischio significativo in molteplici ambienti di lavoro, con potenziali ripercussioni sulla salute e sicurezza dei lavoratori, soprattutto in ambienti industriali dove ...
NEWS
SALUTE E SICUREZZA SUL LAVORO
10/04/2025
Sicurezza sul lavoro: un caso di responsabilità per incendio in azienda
La sicurezza sul lavoro è un tema di primaria importanza, soprattutto in contesti industriali e produttivi, dove il rischio di incidenti è elevato. In particolare, un recente caso discus ...
NEWS
SALUTE E SICUREZZA SUL LAVORO
27/03/2025
Il primo soccorso per contatto accidentale con agenti chimici: la guida INAIL
La gestione delle sostanze chimiche in ambito lavorativo richiede attenzione, preparazione e conoscenza delle procedure di emergenza, dato che il contatto accidentale con agenti chimici può ave ...
NEWS
SALUTE E SICUREZZA SUL LAVORO
13/03/2025
Il Ruolo del RSPP: una garanzia per la sicurezza dei lavoratori e delle figure esterne
Sebbene il suo compito sia di natura consulenziale e non gestionale, Il Responsabile del Servizio di Prevenzione e Protezione (RSPP) ha precisi obblighi giuridici nell'individuare e segnalare i rischi ...
NEWS
SALUTE E SICUREZZA SUL LAVORO
13/02/2025
Interazione uomo-macchina: è possibile prevedere gli usi scorretti?
Nell'era della digitalizzazione, l'interazione tra uomo e macchina si evolve rapidamente, portando con sé nuove sfide per la valutazione dei rischi dei lavoratori, per garantire la loro salute ...
NEWS
SALUTE E SICUREZZA SUL LAVORO
30/01/2025
Gestire il rischio di stress lavoro correlato: la monotonia, i suoi effetti e le misure correttive più efficaci.
In un mondo lavorativo in continua evoluzione, il tema dello stress lavoro correlato è diventato di crescente importanza, soprattutto a seguito degli impatti causati dalla pandemia e dai cambia ...
NEWS
SALUTE E SICUREZZA SUL LAVORO
16/01/2025
La responsabilità del datore di lavoro nella sicurezza: spunti dalla recente sentenza della Corte di Cassazione
La sentenza della Corte di Cassazione in questione – la n. 39168 del 25 ottobre 2024 – risulta particolarmente interessante in quanto mette in evidenza le possibili conseguenze di una viol ...
NEWS
SALUTE E SICUREZZA SUL LAVORO
12/12/2024
Gestione dei near miss nelle piccole imprese: un'iniziativa INAIL
Negli ultimi anni, la gestione dei near miss – eventi che non provocano danni fisici ai lavoratori, ma hanno il potenziale di causare infortuni – ha acquisito sempre maggiore rilevanza nel ...
NEWS
SALUTE E SICUREZZA SUL LAVORO
28/11/2024
Agenti chimici e DPI: protezione di vie respiratorie, occhi, mani e corpo
Più volte in passato abbiamo parlato dei rischi causati dagli agenti chimici presenti in alcuni ambienti di lavoro (ad esempio in questo articolo del 2021 e in questo altro articolo del 2023).
...
NEWS
SALUTE E SICUREZZA SUL LAVORO
14/11/2024
Attività di pulizia: la sicurezza delle macchine semoventi con operatore a bordo
Ce lo diciamo da sempre: la sicurezza è un elemento fondamentale durante le fasi di utilizzo di una macchina o attrezzatura da lavoro, per via dei numerosi rischi di infortunio e malattie profe ...
NEWS
SALUTE E SICUREZZA SUL LAVORO
10/10/2024
L'importanza della formazione e della verifica nell'utilizzo delle attrezzature di lavoro
La sicurezza sul lavoro è un tema di primaria importanza, specialmente in contesti dove l'uso di vari macchinari e/o e attrezzature è quotidiano. A tal proposito, un recente verdetto del ...
NEWS
SALUTE E SICUREZZA SUL LAVORO
26/09/2024
Robotica avanzata e intelligenza artificiale: opportunità e rischi per la salute e sicurezza sul Lavoro
L'evoluzione della tecnologia nel contesto lavorativo – soprattutto attraverso l'adozione della robotica avanzata e dell'intelligenza artificiale – ha portato significativi cambiamenti nel ...
NEWS
SALUTE E SICUREZZA SUL LAVORO
12/09/2024
Esplosioni da polveri: prevenzione e protezione tecnica
Il rischio associato alle esplosioni da polveri rappresenta una minaccia significativa in molte attività industriali, incluse quelle del settore alimentare, tessile, della plastica, dei metalli ...
NEWS
SALUTE E SICUREZZA SUL LAVORO
11/07/2024
Esoscheletri e sicurezza sul lavoro: la nuova norma Uni/Tr 11950 per un utilizzo consapevole
Gli esoscheletri occupazionali sono dispositivi indossabili progettati per assistere e supportare fisicamente i lavoratori durante le attività lavorative, permettendo loro di ridurre lo sforzo ...
NEWS
SALUTE E SICUREZZA SUL LAVORO
27/06/2024
Rischio macchina: come individuare e valutare carenze nella prevenzione
A chi ci legge ormai è ben noto che per garantire la sicurezza sul luogo di lavoro è essenziale svolgere una corretta valutazione del rischio e adottare misure preventive adeguate che pe ...
NEWS
SALUTE E SICUREZZA SUL LAVORO
23/05/2024
Guida ai dispositivi di protezione individuale per il lavoro con agenti chimici pericolosi
Se è vero che, quando si tratta di sicurezza sul lavoro, prevenire è sempre meglio che curare, ciò vale ancora di più quando si tratta di agenti chimici pericolosi. Ogni gi ...
NEWS
SALUTE E SICUREZZA SUL LAVORO
18/04/2024
Responsabilità condivisa e sicurezza macchine: una sentenza rilevante per gli imprenditori
In un recente verdetto della IV Sezione penale della Corte di Cassazione, emerge un chiaro messaggio per gli imprenditori e i fornitori del settore delle macchine industriali: la sicurezza deve essere ...
NEWS
SALUTE E SICUREZZA SUL LAVORO
14/03/2024
Nuovo bando 2023-2024 per finanziamenti a fondo perduto alle imprese: ecco a chi si rivolge e le modalità di accesso
A dicembre 2023, l’INAIL ha pubblicato il nuovo Bando ISI 2023 – 2024 che permette alle imprese italiane di ottenere finanziamenti a fondo perduto da investire in progetti di miglioramento ...
NEWS
SALUTE E SICUREZZA SUL LAVORO
29/02/2024
Classificazione zone ATEX: cos’è cambiato dal 23 gennaio 2024
A partire dal 23 gennaio 2024, le aziende con zone a rischio esplosione devono aggiornare obbligatoriamente il documento di classificazione dei luoghi per adeguarsi alla nuova normativa vigente.
&nbs ...
NEWS
SALUTE E SICUREZZA SUL LAVORO
15/02/2024
Valutare il sovraccarico biomeccanico: la metodologia check-list OCRA
Come alcuni tra i nostri lettori di vecchia data ricorderanno a maggio 2023 abbiamo condiviso con voi la notizia della recente pubblicazione terzo volume INAIL di schede per la valutazione del rischio ...
NEWS
SALUTE E SICUREZZA SUL LAVORO
25/01/2024
Come valutare la qualità dell’aria nei luoghi di lavoro
Ormai sappiamo bene che la presenza di condizioni ambientali non ottimali può interferire negativamente con le attività lavorative, portando a maggiori distrazioni, rallentamenti, errori ...
CARICA ALTRO
ALTRE NEWS
NEWS
MARCATURA CE
31/03/2016
Progettazione e costruzione dei ripari sulla macchina: la norma UNI EN ISO 14120: 2015
Alla fine del 2015 è stata pubblicata anche in Italia la norma EN ISO 14120: 2015 relativa alla progettazione e costruzione dei ripari fissi e mobili su una macchina. Questa norma, che garant ...
NEWS
SALUTE E SICUREZZA SUL LAVORO
16/02/2016
La Valutazione del Rischio Chimico: il rinnovato metodo Inforisk
La letteratura in merito ai metodi analitici quantitativi per la valutazione preliminare del rischio di esposizione ad agenti chimici è molto estesa e propone varie metodologie, di derivazion ...
NEWS
SALUTE E SICUREZZA SUL LAVORO
25/01/2016
Utilizzo delle banche dati nella valutazione del rischio rumore
Nell’ambito della valutazione di tutti i possibili rischi correlati alle mansioni lavorative e alle attività presenti in azienda, la valutazione del rischio rumore comporta la necessit& ...
NEWS
MARCATURA CE
17/12/2015
Passaggio dalla Direttiva Atex 94/9/CE alla nuova 2014/34/UE
Da più di un anno è stata pubblicata la nuova Direttiva Atex 2014/34/UE che risulterà applicabile a partire dal 20 aprile 2016. Fino a questa data resta applicabile l’attu ...
NEWS
SALUTE E SICUREZZA SUL LAVORO
10/12/2015
Prevenzione delle patologie muscolo-scheletriche: la Linea Guida di Regione Lombardia
Nel settembre 2015 è stata pubblicata la Linea Guida di Regione Lombardia per la prevenzione delle patologie muscolo scheletriche connesse con movimenti e sforzi ripetuti degli arti superiori ...
NEWS
SALUTE E SICUREZZA SUL LAVORO
09/12/2015
La valutazione dei rischio di esposizione a Radiazioni Ottiche Artificiali
Le Radiazioni Ottiche Artificiali sono sempre più presenti all’interno delle nostre aziende, moltiplicandosi appunto l’impiego di sorgenti laser e LED per l’effettuazione de ...
NEWS
SALUTE E SICUREZZA SUL LAVORO
04/12/2015
Scelta dei Dispostivi di Protezione Individuale (DPI) per la protezione delle vie respiratorie
Il datore di lavoro è tenuto a mettere a disposizione dei lavoratori specifici Dispositivi di Protezione Individuale quando i rischi non possano essere ridotti mediante misure tecniche di pre ...
NEWS
SALUTE E SICUREZZA SUL LAVORO
04/12/2015
Analisi del Rischio Esplosione per le operazioni che impiegano polveri combustibili o elettrostatiche
Diversamente da quanto si può pensare i dati storici evidenziano una costante presenza di incidenti in attività produttive causati dall’esplosione di polveri combustibili o elett ...
NEWS
SALUTE E SICUREZZA SUL LAVORO
25/11/2015
Nuova definizione di “operatore” secondo il D.Lgs. 81/2008
Il Decreto Legislativo 14 Settembre 2015, n. 151 ha modificato in alcuni punti il Testo unico in materia di tutela della salute e della sicurezza nei luoghi di lavoro. In particolare, la principale mo ...
NEWS
SALUTE E SICUREZZA SUL LAVORO
02/10/2015
Obbligo del datore di lavoro: valutazione dei rischi sulle macchine in uso
In accordo a quanto riportato nell’art. 28 del D.Lgs. 81/2008 e s.m.i. il datore di Lavoro deve considerare e analizzare tutti i rischi a cui possono essere esposti i propri lavoratori durante ...
NEWS
SALUTE E SICUREZZA SUL LAVORO
08/09/2015
Le novità introdotte dalla nuova versione della norma CEI 11-27 “Lavori su impianti elettrici”
Già in altri passati comunicati ci siamo soffermati sull’importanza di avere una procedura aziendale in merito alla corretta effettuazione di attività di manutenzione su impianti ...
NEWS
SVILUPPO SOSTENIBILE
02/09/2015
Come gli studi di Life Cycle Assessment sono percepiti dalle organizzazioni stesse che li conducono
Gli studi di LCA, sui quali scopi ci siamo già ampiamente dilungati in precedenti comunicati, offrono molteplici benefici all’azienda che li conduce, visti i numerosi utilizzi che possono ...
NEWS
MARCATURA CE
28/08/2015
Responsabilità di progettisti, fabbricanti, fornitori e installatori
Progettare, realizzare e installare un macchinario industriale secondo i requisiti della Direttiva Macchine 2006/42/CE permette di assolvere obblighi ed evitare quindi sanzioni, non solo correlati al ...
NEWS
MARCATURA CE
28/08/2015
Direttiva Atex 94/9/CE: certificazione degli assiemi
La Direttiva Atex 94/9/CE, si applica agli apparecchi destinati ad essere utilizzati in atmosfera potenzialmente esplosiva. Nella definizione di “apparecchi” sono inclusi anche più ...
NEWS
MARCATURA CE
28/08/2015
La valutazione dei rischi secondo la Direttiva Atex 94/9/CE
Il processo di certificazione che porta alla marcatura CE Atex di un prodotto secondo la Direttiva 94/9/CE cambia a secondo del gruppo e della categoria di protezione del prodotto. Tuttavia la necessi ...
NEWS
SALUTE E SICUREZZA SUL LAVORO
27/08/2015
La gestione integrata degli infortuni
La gestione degli infortuni che occorrono in azienda riveste un aspetto molto importante poiché incorpora in sé numerosi obblighi, ma anche numerose opportunità di miglioramento ...
NEWS
SALUTE E SICUREZZA SUL LAVORO
03/07/2015
Noleggio o comodato d’uso di attrezzature assoggettate a verifiche periodiche
L’obbligatorietà delle verifiche periodiche è prevista dall’art. 71, comma 11 del D.Lgs. n.81/2008 e s.m.i. per quelle attrezzature di lavoro riportate nell’elenco dell ...
NEWS
MARCATURA CE
01/07/2015
Classificazione attrezzature a pressione secondo la Direttiva 2014/68/UE (PED)
Dal 1 giugno 2015 è entrato in vigore nell’intero mercato unico europeo e, pertanto, anche in Italia, l’articolo 13 (classificazione delle attrezzature a pressione) della nuova Dire ...
NEWS
SALUTE E SICUREZZA SUL LAVORO
15/06/2015
Il rischio chimico e cancerogeno dell’attività di saldatura
La saldatura di metalli è un’attività lavorativa che si ritrova in numerose aziende italiane, sia all’interno di reparti manutenzione, ove viene eseguita saltuariamente per ...
NEWS
SISTEMI DI GESTIONE
04/05/2015
La Nuova Norma ISO 14001 : 2015
Nel corso dell’anno 2015 è prevista la pubblicazione della nuova Norma ISO 14001:2015 da parte dell’Organizzazione Internazionale per la Normazione (ISO).
La versione odierna del ...
NEWS
SALUTE E SICUREZZA SUL LAVORO
04/05/2015
Dispositivi di Protezione Individuale per le mani
Per quanto riguarda la scelta e l’utilizzo dei Dispositivi di Protezione Individuale (DPI), il datore di lavoro è tenuto a rispettare gli obblighi riportati all’art. 77 del D.Lgs. ...
NEWS
SISTEMI DI GESTIONE
01/04/2015
La Nuova Norma ISO 9001 : 2015 e la gestione del transitorio
Nel corso dell’anno 2015 è prevista la pubblicazione della nuova Norma ISO 9001:2015 da parte dell’Organizzazione Internazionale per la Normazione (ISO).
La Norma che regola la r ...
NEWS
MARCATURA CE
27/03/2015
Uso scorretto ragionevolmente prevedibile di una macchina
Secondo quanto richiesto dalla Direttiva Macchine 2006/42/CE, il Fabbricante di una macchina deve garantire che sia effettuata una valutazione dei rischi esistenti considerando l’uso previsto e ...
NEWS
SALUTE E SICUREZZA SUL LAVORO
17/03/2015
Nuovo Regolamento sui dispositivi di protezione individuale (DPI)
A breve la Commissione Europea pubblicherà un nuovo Regolamento inerente i Dispositivi di Protezione Individuale che andrà a sostituire l’attuale Direttiva 89/686/CEE. A riguardo ...
NEWS
MARCATURA CE
09/03/2015
Parti del sistema di comando legate alla sicurezza: una nuova norma supererà a breve le attuali EN ISO 13849 e IEC 62061
Due importanti norme inerenti la progettazione delle parti del sistema di comando legate alla sicurezza, EN ISO 13849 e IEC 62061, a breve saranno accorpate. Cosa significa questo per i costruttori di ...
CARICA ALTRE NEWS
News
Sistemi innovativi e sicurezza macchine per la lotta al "defeating"
26/06/2025
Nonostante i progressi tecnologici e in ambito di sensibilizzazione di aziende e lavoratori sull’importanza della sicurezza negli ambienti di lavoro, ancora oggi si registrano numerosi infortuni gravi riconducibili alla manomissione o neutralizzazione dei dispositivi di protezione di macchine e impianti.
A tal proposito, il recente documento INAIL — che raccoglie gli atti della conferenza internazionale “Safety & Innovation” svoltasi lo scorso marzo a Roma — offre spunti importanti per affrontare questa problematica.
La conferenza ha riunito esperti internazionali per discutere soluzioni avanzate in tema di sicurezza macchine e non solo. Tra questi, uno dei contributi più rilevanti riguardava proprio il defeating, termine inglese che indica la neutralizzazione intenzionale dei dispositivi di sicurezza installati sui macchinari.
Lo studio “Survey on defeating of safeguards on machinery” a cura di S. Otto (DGUV – Germania) riportato alla conferenza, mette infatti in luce dati allarmanti: la rimozione delle protezioni è una delle principali cause di infortuni sul lavoro legati all’uso delle macchine. Nonostante i rischi evidenti, molte protezioni vengono infatti disattivate dagli operatori e, in alcuni casi, anche con il benestare dei dirigenti. Il motivo? Ottimizzare i tempi, aumentare l’efficienza o semplificare le operazioni.
Tuttavia, il prezzo da pagare per questi solo apparenti vantaggi può essere altissimo, arrivando a causare infortuni anche molto gravi.
Prevenire il defeating è dunque essenziale e richiede l’impegno congiunto di progettisti, costruttori, datori di lavoro e lavoratori. A questo proposito, il documento INAIL raccoglie le principali soluzioni e pratiche emerse durante la conferenza, evidenziando quelle tecnologie emergenti in grado di aumentare concretamente la sicurezza nell’utilizzo dei macchinari. Nello specifico, nel documento si parla di:
· Sistemi di riconoscimento visivo che – anche grazie all’AI – rilevano la presenza di mani vicino a parti pericolose (come ad esempio delle lame) e disattivano automaticamente la funzione pericolosa.
· Barriere fotoelettriche con oscuramento dinamico, che mantengono la protezione attiva senza ostacolare la visibilità o l'operatività.
· Dispositivi e soluzioni progettuali ergonomiche e coinvolgenti, che integrano la sicurezza nel processo lavorativo, senza compromettere la produttività.
Infine, segnaliamo che il sito www.stop-defeating.org offre un’ampia raccolta di materiali formativi, casi studio, moduli didattici scaricabili e video informativi rivolti a costruttori, operatori e dirigenti. L’obiettivo è promuovere la diffusione di buone pratiche contro il defeating, attraverso una corretta sensibilizzazione e formazione in materia di sicurezza sul lavoro a tutti i livelli aziendali – dal dirigente all’operaio – e tramite la progettazione di macchine e protezioni più integrate e capaci di garantire un ambiente di lavoro sicuro senza compromettere l’efficienza operativa.
Per maggiori approfondimenti rimandiamo alla lettura integrale del documento INAIL fin qui analizzato, che come sempre potete scaricare gratuitamente al link qui sotto. Se invece aveste bisogno di una consulenza in materia non esitate a contattarci o a prenotarne una sul portale dedicato. Buona lettura!
- CONFERENCE PROCEEDINGS - "ICSI 2025: International Conference on Safety & Innovation" - INAIL, 2025.
-
News
Il Piano Triennale INAIL 2025-2027: una strategia integrata per salute, sicurezza e sostenibilità del lavoro
12/06/2025
Con la delibera n.7 del 13 maggio 2025 del Consiglio di Indirizzo e Vigilanza, L’INAIL ha recentemente approvato il Piano triennale per la prevenzione 2025-2027, documento cardine che orienterà le politiche italiane in materia di salute e sicurezza sul lavoro nei prossimi tre anni. Con questo viene quindi sancito un primo grande passo avanti nella promozione di un sistema di prevenzione moderno, inclusivo e sostenibile.
Il Piano adotta un approccio integrato ispirato ai principi del Total Worker Health (TWH), il quale definisce la prevenzione come un’azione multidimensionale: protezione dai rischi, promozione del benessere psicosociale e ambienti di lavoro favorevoli. Il modello, in linea con l’Agenda ONU 2030 e la Strategia europea 2021-2027, valorizza il capitale umano e la sostenibilità, puntando alla resilienza e alla competitività del sistema produttivo.
Il documento riconosce inoltre le trasformazioni epocali del mondo del lavoro: l’invecchiamento della forza lavoro, la digitalizzazione e la transizione ecologica impongono infatti una revisione profonda delle strategie di prevenzione. Allo stesso modo, l’uso di intelligenza artificiale e robotica – regolato a livello europeo dall’AI Act (UE 2024/1689) – è un grande cambiamento che presenta notevoli opportunità, ma anche un’importante sfida per la tutela della salute e sicurezza sul lavoro, soprattutto nei settori ad alto rischio.
Azioni strategiche e settori prioritari
Nel corso del documento, il Piano individua quattro assi principali d’intervento:
1. Cultura della prevenzione: progetti formativi dedicati ai giovani per instillare una mentalità sicura fin dai primi contatti con il lavoro;
2. Sostegno alle PMI: incentivi e trasferimento tecnologico dalle attività di ricerca verso le piccole e medie imprese, spesso penalizzate da risorse limitate;
3. Integrazione tra sicurezza e sostenibilità: promozione di pratiche ambientali che riducano i rischi per i lavoratori;
4. Focus sui settori critici: edilizia, logistica, sanità e agricoltura restano ambiti prioritari per interventi mirati.
Conclusioni: uno sguardo verso il futuro
Procedendo con la lettura del Piano in modo più approfondito appare infine chiaro che, più che un documento programmatico, si tratta di una vera e propria roadmap per trasformare la cultura della sicurezza nel nostro Paese. Il suo approccio integrato e forward-looking posiziona infatti l'Italia tra i paesi all'avanguardia nello sviluppo di politiche di prevenzione, preparando il sistema produttivo nazionale ad affrontare le sfide del futuro con strumenti adeguati e una cultura della sicurezza sempre più matura e diffusa.
Tuttavia, nonostante questa ottima premessa, si tratta di obiettivi ambiziosi e complessi, la cui realizzazione richiederà grande impegno e collaborazione tra tutti gli attori del sistema: dalle imprese alle istituzioni, dai lavoratori ai professionisti della sicurezza.
Per saperne di più, al link qui sotto puoi scaricare gratuitamente il Piano triennale di prevenzione 2025-2027, così come pubblicato dall’INAIL. Se invece sei alla ricerca di una consulenza su marcatura CE e sicurezza macchine, puoi contattarci o prenotare direttamente sul portale dedicato.
Buona lettura!
-
Piano Triennale INAIL 2025-2027: una strategia integrata per salute, sicurezza e sostenibilità del lavoro.
News
Sicurezza sul lavoro: ecco perché il preposto non può “chiudere gli occhi”
29/05/2025
Nel contesto della salute e sicurezza sul lavoro, la figura del preposto riveste un ruolo fondamentale e autonomo, anche quando si trova a operare sotto la direzione di superiori gerarchici. Un esempio in proposito è la recente sentenza della Corte di Cassazione (n. 10460 del 17 marzo 2025), che ribadisce con fermezza che l’ordine dall’alto non solleva il preposto dalle proprie responsabilità.
Fatti e iter giudiziario
La vicenda giudiziaria nasce da un grave infortunio accaduto a un operaio apprendista in uno stabilimento del milanese, durante il lavaggio manuale di un filtro essiccatore con disattivazione dei sistemi di sicurezza, che gli è costato l’amputazione di un braccio.
Le prove raccolte, le testimonianze e i riscontri documentali hanno poi dimostrato che, per quanto pericolosa, l’attività in questione risulta una prassi consolidata in azienda, poiché era non solo tollerata, ma di fatto imposta dal dirigente di reparto e trasmessa in modo informale dai capi ai nuovi assunti.
Su queste basi, il Tribunale ha condannato in primo grado il dirigente responsabile del reparto, indicato come consapevole e promotore della prassi irregolare, ma anche i tre preposti – caporeparto, capoturno e vice capoturno – poiché sapevano della prassi, ma non sono intervenuti né hanno informato altri soggetti aziendali al di fuori della linea gerarchica.
In Appello, i tre preposti hanno cercato di far valere la propria estraneità all’evento, sostenendo:
§ di non avere potere effettivo contro le decisioni del dirigente;
§ che la prassi era così consolidata da essere nota a tutti, anche ai superiori;
§ che denunciare sarebbe stato inutile, come dimostrato dal caso di un collega, che era stato trasferito dopo aver sollevato delle rimostranze in proposito.
Tuttavia, la Corte d’Appello ha rigettato il ricorso, sostenendo che l’argomentazione non fosse sufficiente a esonerare i preposti dalle loro responsabilità, poiché l’autonomia della posizione di garanzia del preposto impone comunque l’obbligo di intervento e di segnalazione a figure diverse dal diretto superiore, come RSPP o altri soggetti aziendali.
La sentenza della Cassazione
Successivamente, la Cassazione ha confermato le condanne, con una sentenza che definisce il principio chiave secondo cui il fatto che un preposto agisca sotto le direttive del superiore gerarchico non lo libera da responsabilità qualora abbia tollerato o non denunciato prassi pericolose, poiché la sua posizione di garanzia è autonoma e personale.
In particolare, la Corte ha sottolineato come ciascun garante della sicurezza – inclusi i preposti – sia tenuto a impedire l’evento lesivo fintanto che permane nella sua funzione e che, anche in presenza di pressioni o minacce implicite, la facoltà di rivolgersi a figure esterne al proprio superiore diretto non può venir meno.
Questa sentenza ribadisce dunque l’importanza del ruolo attivo del preposto nella prevenzione degli infortuni sul lavoro e, più in generale, di coloro che ricoprono cariche legate alla sicurezza sul luogo di lavoro: non è sufficiente “eseguire ordini” o “adeguarsi al clima aziendale” quando si ricopre un ruolo di garante che, come tale, chiama a vigilare, intervenire e – se necessario – denunciare.
Per maggiori dettagli in merito alla sentenza della Cassazione in questione, al link qui sotto è possibile scaricarne gratuitamente la versione integrale. Se invece necessitate di una consulenza non esitate a contattarci o ad acquistare un servizio dal nostro portale dedicato. Buona lettura!
-
Cassazione Penale, Sez. 4, 17 marzo 2025, n. 10460 - Amputazione del braccio dell'apprendista-operaio durante la pulizia della macchina filtro essiccatore. Prassi consolidata di lavaggio a boccaporto aperto.
News
Sicurezza sul lavoro: i chiarimenti dell’INL su macchine e attrezzature
15/05/2025
Il 18 marzo 2025, l’Ispettorato Nazionale del Lavoro (INL) ha pubblicato la Circolare n. 2668 per fornire importanti chiarimenti operativi in materia di sicurezza, in risposta alle numerose richieste ricevute da aziende e professionisti. Il documento – scaricabile gratuitamente a fondo pagina – è frutto di un confronto con il Gruppo Tecnico Interregionale Salute e Sicurezza sul Lavoro e diventa, dunque, un riferimento per l’applicazione uniforme del D.Lgs. 81/2008, in coerenza con l’Accordo Stato-Regioni del 27 luglio 2022.
Luoghi di lavoro e “categorie omogenee” di violazioni
Uno dei temi affrontati riguarda l’applicazione dell’art. 68, comma 2 del Testo Unico sulla Sicurezza sul Lavoro, il quale stabilisce che la violazione di più precetti riferiti a una stessa “categoria omogenea” di requisiti di sicurezza nei luoghi di lavoro venga considerata un’unica infrazione, con conseguente applicazione di una sola sanzione. Il dubbio in questione nasce dalla non esplicitazione di cosa si intendesse, in concreto, per “categoria omogenea”.
Per risolvere questa ambiguità interpretativa, la circolare spiega che i vari punti dell’Allegato IV del D.Lgs. 81/2008 indicano ciascuno una categoria distinta, raggruppando precetti che tutelano uno stesso interesse (es. stabilità strutturale, aerazione, illuminazione, ecc.).
Nella circolare è dunque chiarito che, se più inadempienze riguardano la stessa categoria tra quelle elencate nell’Allegato IV – come ad esempio la stabilità strutturale – esse verranno trattate come un'unica violazione e, di conseguenza, un’unica sanzione. Al contrario, infrazioni che ricadono in categorie diverse – ad esempio una sulla stabilità e una sull’illuminazione – sono da considerarsi violazioni distinte, che comporteranno quindi due sanzioni separate.
Questo chiarimento è fondamentale per garantire un’applicazione equa e coerente delle norme durante le ispezioni.
Macchine “ante direttiva”: certificazione di conformità
Un altro nodo chiarito dalla circolare riguarda la conformità delle macchine costruite prima del 21 settembre 1996, cioè prima che entrasse in vigore il DPR 459/1996, il quale recepiva la prima Direttiva Macchine (89/392/CEE). Queste macchine, essendo prive di marcatura CE, devono oggi rispettare i requisiti generali di sicurezza previsti dall’Allegato V del D.Lgs. 81/2008.
La necessità di chiarimento nasce dal fatto che, nella pratica, è diffusa l’idea che per attestare la conformità di queste macchine fosse obbligatorio rivolgersi a un tecnico abilitato. La circolare chiarisce invece che il legislatore non impone alcun obbligo di certificazione da parte di un tecnico: il Datore di Lavoro ha l’obbligo di effettuare una corretta valutazione dei rischi e di assicurarsi che l’attrezzatura rispetti i requisiti dell’Allegato V, ma, sebbene possa avvalersi della consulenza di un tecnico abilitato, non è tenuto per legge a ottenere una certificazione formale, dato che l’assenza di un’attestazione tecnica non equivale automaticamente a una non conformità.
Macchine “ante direttiva”: manuale d’uso e manutenzione
Il terzo e ultimo punto della circolare riguarda anch’esso le attrezzature messe in servizio prima del DPR 459/1996: per queste non era previsto, all’epoca, l’obbligo del libretto di uso e manutenzione. Tuttavia, oggi il Datore di lavoro deve comunque garantire la disponibilità di istruzioni operative, procedure scritte o schede tecniche che forniscano tutte le informazioni essenziali per l’uso in sicurezza dell’attrezzatura, così come previsto dall’Allegato V, punto 9.2 del D.Lgs. 81/2008.
Il dubbio operativo, emerso in molte aziende, era se fosse necessario redigere ex novo un manuale completo anche per queste attrezzature datate. In proposito, la circolare chiarisce che non è obbligatorio ricostruire o redigere integralmente il libretto, poiché questo obbligo non esisteva all’epoca della produzione, ma sottolinea comunque l’obbligo del Datore di lavoro di fornire ai lavoratori informazioni chiare e accessibili, tramite schede tecniche, istruzioni operative o procedure che indichino modalità d’uso, rischi, misure di sicurezza e comportamenti corretti.
Come anticipato all’inizio dell’articolo, al link qui sotto potete scaricare gratuitamente la versione integrale della circolare fin qui analizzata. Se invece siete alla ricerca di una consulenza personalizzata non esitate a contattarci o ad acquistare una video consulenza specifica sul portale dedicato. Buona lettura!
-
Circolare 2668: Modalità di applicazione delle sanzioni ai precetti riconducibili alla stessa categoria omogenea – Conformità macchine ante direttiva. Chiarimenti.
News
Valutazione del rischio da stress termico: strumenti e metodi per una sicurezza efficace sul lavoro
24/04/2025
Lo stress termico rappresenta un rischio significativo in molteplici ambienti di lavoro, con potenziali ripercussioni sulla salute e sicurezza dei lavoratori, soprattutto in ambienti industriali dove le condizioni di lavoro possono variare rapidamente.
In particolare, oggi ce ne occupiamo a partire dallo studio "Rischio da stress termico e l’utilizzo consapevole degli indici di esposizione", così come presentato da Alessandro Merlino, Daniele Meda, Andrea Pelizzoni, Gabriele Quadrio e Diego Rizzardini durante il convegno "dBA2024 – Agenti Fisici nei luoghi di lavoro" del 20 novembre 2024.
L’approccio descritto è ispirato alla norma UNI EN ISO 15265:2005 e mette in evidenza l'importanza di selezionare e utilizzare correttamente gli indici di esposizione.
Premessa: stress termico vs discomfort termico
Nel contesto del D.Lgs.81/2008, che riguarda la salute e la sicurezza sul lavoro, i concetti di stress termico e discomfort termico sono distinti, ma entrambi si riferiscono agli effetti delle condizioni termiche sull'organismo umano. Ecco le differenze principali:
1. Stress termico
Si verifica quando il corpo umano non è in grado di mantenere una temperatura interna stabile a causa di condizioni ambientali estreme. Può provocare problemi come colpi di calore, esaurimento da calore, congelamenti o ipotermia, a seconda delle condizioni specifiche. Nel D.Lgs. 81/2008, lo stress termico è considerato un rischio per la salute, e sono previsti criteri di valutazione e misure preventive per proteggere i lavoratori.
2. Discomfort termico
Il discomfort termico, d'altra parte, è una condizione in cui la temperatura ambiente non è ideale per il benessere del lavoratore, ma non comporta rischi immediati per la salute. È il caso di quegli ambienti di lavoro un po’ troppo caldi o freddi che causano disagio a molti, ma senza portare a danni fisici gravi. Nel D.Lgs.81/2008, il discomfort termico non è classificato come rischio per la salute in senso stretto, ma può influire su l benessere e sulla produttività dei lavoratori.
Se nei contesti non industriali ci si basa sugli indici di comfort termico (Es. per regolare il termostato in ufficio), in ambito industriale sono spesso necessarie temperature fuori dal comfort ideale, motivo per cui è essenziale valutare il rischio da stress termico. Tuttavia, basarsi esclusivamente sugli indici di stress termico potrebbe condurre a valutazioni incomplete o poco esaustive; per questo motivo, la valutazione di questo rischio deve necessariamente passare attraverso l’uso consapevole degli indici di esposizione.
Tuttavia, il microclima è meno normato di altri agenti fisici come vibrazioni e rumore, per i quali esistono metodi e limiti ben definiti. Il D.Lgs. 81/2008 non prevede infatti valori limiti di esposizione (VLE) o valori di azione (VA) specifici per lo stress termico, il che rende difficile l’identificazione e la quantificazione del rischio e limita la possibilità di sviluppare procedure adeguate di prevenzione e protezione.
Un metodo integrato di valutazione
Lo studio in questione propone una metodologia di valutazione del rischio che integra sia indici di comfort termico – come il Predicted Mean Vote o PMV – sia indici di stress termico, allo scopo di ottenere una valutazione più completa ed efficace.
A tal proposito, la tabella delle classi di rischio della UNI EN ISO 15265 offre un valido quadro di riferimento (Tabella 1 Pag. 10 del doc. integrale a fondo pagina).
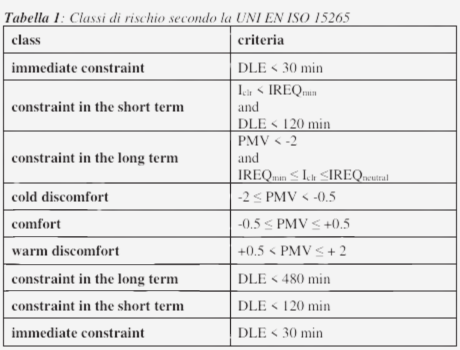
Il comfort termico viene suddiviso in intervalli specifici, permettendo di identificare rapidamente le condizioni di disagio: se l’indice PMV rientra nell’intervallo “-0.5, +0.5”, l’esposizione è considerata sotto controllo, in caso contrario vanno attivate strategie e azioni correttive e/o di gestione, che variano al variare dell’intervallo.
L’applicazione sul campo di questo metodo permette di raggiungere due obiettivi:
§ Essere efficaci, restituendo dati capaci di restituire un dettagliato spettro dell’entità del rischio, dove questo è presente;
§ Dotare il datore di lavoro di uno strumento concreto per la gestione del rischio in azienda e non un troppo semplicistico “promosso o bocciato”.
Per maggiori approfondimenti riguardo allo studio in questione, qui sotto trovate il link per scaricare gratuitamente il documento integrale di riferimento, che riporta anche diversi esempi pratici. Buona lettura!
-
“Rischio da stress termico e l’utilizzo consapevole degli indici di esposizione”, a cura di Alessandro Merlino, Daniele Meda, Andrea Pelizzoni, Gabriele Quadrio, Diego Rizzardini (CeSNIR), intervento al convegno “dBA2024 – Agenti Fisici nei luoghi di lavoro: stato dell’arte, novità e strumenti di supporto alla valutazione del rischio” (Bologna, novembre 2024).
News
Sicurezza sul lavoro: un caso di responsabilità per incendio in azienda
10/04/2025
La sicurezza sul lavoro è un tema di primaria importanza, soprattutto in contesti industriali e produttivi, dove il rischio di incidenti è elevato. In particolare, un recente caso discusso dalla Corte di Cassazione porta alla luce le implicazioni legali e le responsabilità del Datore di Lavoro riguardo la formazione e l'informazione dei lavoratori in relazione ai rischi di incendio.
I fatti e l’iter giudiziario
Il 6 giugno 2017, all'interno dello stabilimento in Veneto, un operaio ha subito gravi ustioni mentre cercava di gestire un incendio causato da scintille generate da un attrezzo di lavoro. In un tentativo impulsivo di arginare il fuoco, l’operaio ha sollevato un contenitore di solvente in fiamme, subendo così ustioni sul 44% del corpo. L'incidente ha sollevato dubbi sulla formazione ricevuta dall'operaio e sulla conduzione delle misure di sicurezza da parte del Datore di Lavoro.
Il Datore di Lavoro e legale rappresentante dell’azienda è stato condannato per lesioni colpose, sia in primo grado che in appello. Nel suo ricorso alla Cassazione, ha sollevato alcune critiche, tra cui:
1. Ha contestato la motivazione sulla connessione tra le sue responsabilità e l'infortunio, sostenendo che la Corte di Appello non ha chiarito quali obblighi formativi siano stati trasgrediti e come una formazione adeguata avrebbe potuto prevenire l'incidente.
2. Ha dichiarato che il comportamento del lavoratore era "abnorme", attribuendo a lui la responsabilità dell'incidente poiché ha agito in modo "irragionevole" e non conforme alle procedure di sicurezza, affermando che questo interromperebbe il nesso causale tra le mancanze aziendali e l'incidente.
La decisione della Corte di Cassazione
Lo scorso 31 gennaio 2025, la Corte ha confermato la condanna del Datore di Lavoro, ritenendo non valide le sue obiezioni riguardo alla condotta "abnorme" del lavoratore. Infatti, la Corte ha sottolineato che un comportamento può essere definito "abnorme" solo se si distacca in modo del tutto imprevedibile dalle normali mansioni lavorative.
Inoltre, è stato ribadito che una formazione adeguata è un obbligo fondamentale per il Datore di Lavoro, come stabilito dalla normativa sulla sicurezza sul lavoro (D.Lgs. 81/2008). La mancanza di istruzioni specifiche in situazioni di emergenza, come un incendio, non può essere giustificata.
In assenza di informazioni utili e procedure chiare, il lavoratore può reagire in modo istintivo e pericoloso. Questo è esattamente quanto accaduto nel caso in questione, dove il tentativo di spegnere le fiamme ha portato a conseguenze tragiche. La reazione del lavoratore, sebbene avventata, è stata considerata non solo prevedibile, ma anche comprensibile, il che evidenzia la responsabilità del Datore di Lavoro per non aver fornito le necessarie procedure e formazione.
In conclusione
Questa sentenza rappresenta un forte richiamo all'importanza della formazione sulla sicurezza dei lavoratori, soprattutto in ambiti dove si maneggiano sostanze infiammabili o pericolose. I datori di lavoro devono garantire ai loro dipendenti non solo una formazione teorica generica, ma istruzioni specifiche su come affrontare i rischi in situazioni di emergenza, in modo da evitare incidenti gravi e le conseguenze legali che ne seguono.
Per maggiori informazioni sul caso giudiziario, al link qui sotto è possibile scaricare gratuitamente la sentenza della Corte di Cassazione fin qui citata nella sua versione integrale. Buona lettura!
-
Cassazione Penale, Sez. 4, 31 gennaio 2025, n. 4165 - Ustioni al lavoratore che tenta di spegnere un incendio causato da scintille generate da una mola. Nessun comportamento abnorme se il datore di lavoro non rispetta gli obblighi di formazione.
News
Il primo soccorso per contatto accidentale con agenti chimici: la guida INAIL
27/03/2025
La gestione delle sostanze chimiche in ambito lavorativo richiede attenzione, preparazione e conoscenza delle procedure di emergenza, dato che il contatto accidentale con agenti chimici può avere conseguenze particolarmente gravi per la salute dei lavoratori. Con queste premesse, lo scorso novembre è stato pubblicato il documento “Azioni di primo soccorso in caso di contatto accidentale con agenti chimici”, a cura del Dipartimento di medicina, epidemiologia, igiene del lavoro e ambientale (Dimeila) dell’INAIL.
Questo manuale di circa 80 pagine risulta essere uno strumento schematico e di facile consultazione delle principali situazioni che potrebbero verificarsi, utile per i datori di lavoro, gli addetti al primo soccorso aziendale e i lavoratori che potrebbero trovarsi a dover intervenire in caso di incidenti dovuti ad agenti chimici. Tuttavia, ricordiamo che, per la sua natura schematica, il documento non può considerarsi esaustivo di tutte le possibili situazioni, motivo per cui le sue indicazioni vanno sempre affiancate ad altre informazioni specifiche, come quelle contenute nelle schede dati di sicurezza dei singoli prodotti.
Tipologie di contatto e come gestirle
Oltre che in base al tipo di agente chimico, il manuale fornisce consigli di primo soccorso per i principali tipi di contatto con la sostanza chimica. Ad esempio:
1. Contatto con la pelle
Il contatto cutaneo con sostanze chimiche può causare irritazioni, ustioni o assorbimento sistemico della sostanza. In caso di incidente:
Rimuovere immediatamente gli indumenti contaminati, evitando di diffondere la sostanza su altre parti del corpo.
Sciacquare abbondantemente la zona interessata con acqua corrente per almeno 15-20 minuti. Utilizzare docce di emergenza se disponibili.
Non strofinare la pelle, per evitare di peggiorare l'irritazione o diffondere la sostanza.
Consultare un medico se il contatto ha causato ustioni, arrossamenti persistenti o qualsiasi altro sintomo.
2. Contatto con gli occhi
Gli occhi sono particolarmente sensibili ai danni causati da sostanze chimiche. In caso di contatto:
Sciacquare immediatamente con acqua corrente per almeno 15 minuti, tenendo le palpebre aperte per garantire un lavaggio completo.
Utilizzare lavaocchi di emergenza, se presenti sul posto di lavoro.
Non strofinare gli occhi, per evitare ulteriori danni.
Rivolgersi ad un medico o a un oculista il prima possibile, anche se i sintomi sembrano lievi.
3. Contattto per inalazione
L'inalazione di vapori, gas o polveri tossiche può causare difficoltà respiratorie, intossicazione o danni ai polmoni. In caso di esposizione:
Allontanare immediatamente la persona dall'area contaminata, portandola in un luogo con aria fresca.
Chiamare i soccorsi e fornire informazioni dettagliate sulla sostanza inalata.
Somministrare ossigeno, sempre se se possibile e se si è formati per farlo.
Monitorare i sintomi: difficoltà respiratorie, vertigini nausea o perdita di coscienza richiedono un intervento medico urgente.
4. Ingestione accidentale
L'ingestione di sostanze chimiche è un'evenienza rara ma potenzialmente molto pericolosa. In caso di incidente:
Contattare immediatamente un centro antiveleni e/o un medico, fornendo indicazioni precise sulla sostanza ingerita.
Non indurre il vomito, a meno che non sia espressamente indicato da un professionista sanitario.
Somministrare acqua o latte, a seconda di cosa consigliato dall'esperto.
La prevenzione è la miglior difesa
Sapere come comportarsi in caso di contatto accidentale con gli agenti chimici è essenziale, ma la prevenzione rimane la strategia più efficace per ridurre i rischi legati alle sostanze chimiche, evitando di incorrere in situazioni pericolose.
A tal proposito, il documento segnala alcune buone pratiche, tra cui:
Formazione dei dipendenti: assicurarsi che conoscano le procedure di sicurezza e le misure di primo soccorso.
Dispositivi di Protezione Individuale (DPI): utilizzare sempre guanti, occhiali, maschere e indumenti protettivi adeguati.
Etichettatura e schede di sicurezza: verificare che tutte le sostanze chimiche siano correttamente etichettate e che le schede di sicurezza siano facilmente accessibili.
Dotazione di emergenza: assicurarsi che siano sempre presenti docce di sicurezza, lavaocchi e kit di primo soccorso nelle vicinanze delle aree di lavoro a rischio.
In conclusione, sebbene il contatto accidentale con agenti chimici possa avere conseguenze gravi, un intervento rapido e appropriato può limitare i danni e salvare vite, soprattutto se abbinato ad un'adeguata valutazione e gestione del rischio specifico.
Ti serve una mano con la valutazione dei rischi? Contattaci!
Se invece vuoi ricevere ulteriori informazioni in materia di rischi chimici puoi consultare la versione integrale del manuale INAIL fin qui analizzato: basta cliccare qui sotto e scaricarlo gratuitamente. Buona lettura!
-
Inail, Dipartimento di medicina, epidemiologia, igiene del lavoro e ambientale, “ Azioni di primo soccorso in caso di contatto con agenti chimici. Manuale” - Curato da Lidia Caporossi, Mariangela De Rosa, Silvia Capanna, Bruno Papaleo, Alessandra Pera e Stefano Moriani (Inail, Dimeila) e da Giorgio Ricci e Lorenzo Losso (Centro Antiveleni di Verona, Azienda ospedaliera universitaria integrata Verona), ed. 2024, Collana Salute e sicurezza.
News
Il Ruolo del RSPP: una garanzia per la sicurezza dei lavoratori e delle figure esterne
13/03/2025
Sebbene il suo compito sia di natura consulenziale e non gestionale, Il Responsabile del Servizio di Prevenzione e Protezione (RSPP) ha precisi obblighi giuridici nell'individuare e segnalare i rischi presenti nell'ambiente lavorativo. Egli può dunque essere chiamato a rispondere, quale garante, degli eventi che si dovessero verificare per effetto della violazione dei suoi doveri di sicurezza.
Tale principio è stato ribadito dalla Corte di Cassazione nella sua recente sentenza n. 42483 del 20 novembre 2024 (u.p. 23 ottobre 2024), secondo cui l’RSPP può essere considerato garante della sicurezza, non solo per i lavoratori, ma anche per i terzi che si trovano nell'ambiente di lavoro.
Fatti e iter giudiziario
La sentenza riguarda un incidente mortale avvenuto durante una gara di orienteering in un parco pubblico. In questa circostanza, un minore è caduto in un pozzo non adeguatamente segnalato e coperto, riportando conseguenze fatali. L’ RSPP incaricato della redazione del Documento di Valutazione dei Rischi (DVR) non aveva indicato il pericolo rappresentato dal pozzo, e ciò è stato ritenuto un elemento determinante per l'incidente.
La corte ha infatti rigettato il ricorso del RSPP, confermando la responsabilità per omicidio colposo aggravato dalla violazione delle norme di sicurezza. La mancata segnalazione del pericolo ha infatti determinato una situazione di rischio evitabile, aggravando le responsabilità del RSPP come garante della sicurezza.
La sentenza
Nell sentenza, la Corte di Cassazione ha sottolineato la responsabilità del RSPP secondo il principio per cui la normativa antinfortunistica è volta a tutelare non solo i lavoratori, ma anche chiunque acceda all’ambiente di lavoro, indipendentemente dall'esistenza di un rapporto di dipendenza con l'azienda.
Sebbene si tratti di un fatto avvenuto in un parco pubblico, questo principio è cruciale non solo per garantire la sicurezza in luoghi accessibili alla collettività – parchi, centri commerciali o fiere – ma anche per tutte le aziende alle quali accedono fornitori, clienti e altre figure esterne.
Conclusioni
Il ruolo del RSPP è dunque fondamentale per la prevenzione degli infortuni e, per essere svolto al meglio, deve avvalersi di un Documento di Valutazione dei Rischi accurato e una costante collaborazione con il datore di lavoro, in modo da garantire un ambiente sicuro per tutti, lavoratori e figure terze.
Per maggiori informazioni sul caso giudiziario, al link qui sotto è possibile scaricare gratuitamente la sentenza della Corte di Cassazione fin qui citata nella sua versione integrale. Buona lettura!
-
Cassazione Penale, Sez. 4, 20 novembre 2024, n. 42483 - Caduta nel pozzo del minore durante la gara di orienteering.
News
Interazione uomo-macchina: è possibile prevedere gli usi scorretti?
13/02/2025
Nell'era della digitalizzazione, l'interazione tra uomo e macchina si evolve rapidamente, portando con sé nuove sfide per la valutazione dei rischi dei lavoratori, per garantire la loro salute e sicurezza. In particolare, un recente factsheet INAIL dedicato alle macchine autonome e semiautonome affronta un aspetto cruciale della questione: In un contesto in cui le macchine non solo affiancano, ma richiedono attivamente la collaborazione dell'operatore umano, è ragionevolmente prevedibile l'uso scorretto di queste tecnologie?
Tradizionalmente, la sicurezza sul lavoro si basa sulla separazione fisica tra l'operatore e i componenti pericolosi delle macchine, come ad esempio mettendo barriere fisiche che coprano gli organi mobili, evitandone così il contatto accidentale con il lavoratore.
Tuttavia, con la crescente autonomia delle tecnologie, questa separazione sta diventando sempre più impraticabile: l’interazione diretta rappresenta infatti il fulcro dei sistemi uomo-macchina, rendendo inevitabile una valutazione approfondita dei comportamenti umani e delle loro variabili.
A questo proposito, un elemento chiave del documento è la necessità di esaminare gli stati cognitivi che possono causare usi non corretti, poiché per progettare sistemi di lavoro veramente sicuri è fondamentale comprendere e modellare le condizioni cognitive degli operatori. Questo approccio antropocentrico suggerisce quindi che la progettazione delle macchine debba mirare a ridurre il carico cognitivo e migliorare il comfort operativo, in modo da prevenire l'insorgere di errori involontari, piuttosto che limitarsi a stimarli.
Esaminando infine la questione in relazione al quadro normativo di riferimento, risulta più importante che mai garantire il rispetto dei requisiti progettuali per prevenire infortuni nell'uso delle macchine. Sotto questo aspetto, la Direttiva Macchine 2006/42/CE e il Regolamento UE 2023/1230 richiedono al fabbricante di garantire che i prodotti soddisfino requisiti minimi attraverso una valutazione dei rischi, che deve considerare sia l'uso previsto che quello scorretto.
Nonostante la soggettività dei termini "prevedibile" e "ragionevole", i fabbricanti devono tenere conto degli usi scorretti ragionevolmente prevedibili da parte degli utenti finali, adottando misure adeguate.
A tal proposito, il documento segnala che:
§ la norma UNI EN ISO 12100 offre esempi di comportamenti involontari;
§ il Rapporto Tecnico UNI ISO/TR14121-2 sottolinea l'importanza di una comunicazione efficace tra fabbricanti e utilizzatori per identificare usi scorretti;
§ la norma UNI EN ISO 14119 evidenzia il ruolo degli operatori nella scoperta di usi potenzialmente pericolosi.
È fondamentale poi considerare come l'organizzazione del lavoro e la formazione influenzino i comportamenti degli operatori, soprattutto in caso di malfunzionamenti. Gli autori, però, evidenziano che le normative tecniche non forniscono indicazioni pratiche per identificare o valutare i rischi. Inoltre, per le macchine autonome e semi-autonome, le informazioni tra i diversi soggetti coinvolti sono ancora limitate a causa della recente introduzione di queste tecnologie.
In conclusione, l'interazione tra uomo e macchina, in particolare nelle macchine autonome e semi-autonome, richiede un'analisi approfondita e una progettazione che metta al centro l'operatore. Investire nella formazione, nel monitoraggio delle variabili cognitive e nella progettazione ergonomica aiuta a ridurre gli usi scorretti e a migliorare la sicurezza sul lavoro.
Per approfondire ulteriormente l’argomento, invitiamo a consultare il factsheet INAIL fin qui citato nella sua versione integrale, scaricabile gratuitamente al link qui sotto. Buona lettura!
-
INTERAZIONE UOMO-MACCHINA: L’USO SCORRETTO PUÒ ESSERE RAGIONEVOLMENTE PREVEDIBILE? - INAIL, 2024
News
Gestire il rischio di stress lavoro correlato: la monotonia, i suoi effetti e le misure correttive più efficaci.
30/01/2025
In un mondo lavorativo in continua evoluzione, il tema dello stress lavoro correlato è diventato di crescente importanza, soprattutto a seguito degli impatti causati dalla pandemia e dai cambiamenti sociali e ambientali in atto. A tal proposito, il documento “Primo documento di consenso. Dallo stress lavoro correlato alla prevenzione dei rischi psicosociali” della Consulta Interassociativa Italiana per la Prevenzione (CIIP) offre linee guida preziose su come affrontare la questione con strategie efficaci.
Innanzitutto, il documento inizia sottolineando che, come per altre tipologie di rischio sul lavoro, l’eliminazione o la riduzione dei problemi di stress lavoro correlato passa in primo luogo dall’individuazione delle fonti di tale stress, per poi adottare misure correttive, come ad esempio misure di gestione e di comunicazione, formazione specifica in materia per dirigenti e lavoratori.
Tuttavia – prosegue il documento – nel nostro paese tali misure vengono raramente introdotte in modo attivo e costante dalle aziende. Inoltre, quando ciò avviene, si tratta per lo più di misure individuali – come percorsi formativi individuali sulla resilienza, sportelli di ascolto, counseling, coaching – o misure collettive - formazione di team/reparti su soft skills quali ad esempio il team working o la gestione dei conflitti.
Sebbene risultino utili a mitigare la situazione, quello che spesso manca sono gli interventi primari di tipo organizzativo, che in molti casi i lavoratori indicano come i veri stressor, che però non sono quasi mai oggetto di intervento poiché ritenuto troppo complesso o rischioso.
Tuttavia, tra le possibili azioni correttive di tipo organizzativo rientrano anche interventi meno complessi, come ad esempio:
ü l’adozione di un codice etico volto a identificare comportamenti inaccettabili e responsabilizzare i dirigenti nella promozione di procedure che possano contrastarli;
ü integrare i risultati delle valutazioni del rischio stress con altre analisi aziendali, come indagini sul clima e bilanci di genere, in modo da poter per elaborare piani d’azione coesi e mirati che considerino il benessere a all'interno dell'organizzazione 360 gradi.
Particolare attenzione deve essere poi rivolta al carico mentale e alla monotonia, che possono influenzare negativamente la produttività e la salute psicologica dei lavoratori. La monotonia, infatti, può causare fatica mentale, riduzione della vigilanza e, alla lunga, anche potenziali disturbi psichiatrici. Per contrastare questi effetti, il CIIP suggerisce varie misure, tra cui:
ü favorire interazioni relazionali tra collaboratori e superiori, creando un ambiente di lavoro più coeso e supportivo;
ü rivedere la programmazione delle pause di riposo, per garantire una maggiore rigenerazione psicofisica;
ü Ridurre la staticità delle mansioni, rendendo il lavoro più dinamico;
ü arricchire i compiti lavorativi con una maggiore varietà, per prevenire la sensazione di monotonia;
ü promuovere una comunicazione fluida tra i membri del team e garantire un adeguato livello di autonomia nella gestione del ritmo di lavoro.
Infine, qualora non fosse possibile evitare la monotonia attraverso modifiche progettuali, le aziende dovrebbero considerare l’automazione delle attività più ripetitive, affinché i lavoratori possano concentrarsi sulle mansioni a maggior valore aggiunto.
In conclusione, il documento fin qui analizzato sottolinea quanto sia essenziale l’impegno costante e coordinato dell'intera direzione aziendale per affrontare il rischio di stress lavoro correlato, arrivando sempre più ad offrire un ambiente di lavoro sano e produttivo, che permette non solo di salvaguardare la salute dei lavoratori, ma anche per incrementare la performance complessiva dell’azienda.
Per maggiori dettagli sull’argomento, come sempre qui sotto è presente il link per scaricare gratuitamente il documento integrale da cui è tratto l’articolo.
Buona lettura!
-
PRIMO DOCUMENTO DI CONSENSO Dallo stress lavoro correlato alla prevenzione dei rischi psicosociali A cura del Gruppo di Lavoro CIIP “Stress lavoro-correlato”
News
La responsabilità del datore di lavoro nella sicurezza: spunti dalla recente sentenza della Corte di Cassazione
16/01/2025
La sentenza della Corte di Cassazione in questione – la n. 39168 del 25 ottobre 2024 – risulta particolarmente interessante in quanto mette in evidenza le possibili conseguenze di una violazione degli obblighi di sicurezza da parte del datore di lavoro.
In particolare, la Corte in questa sede ha ribadito come, in quanto garante della sicurezza dei suoi lavoratori, il datore di lavoro deve assolvere tutti i suoi compiti in modo attivo, poiché non impedire un evento che si ha l'obbligo giuridico di impedire equivale a cagionarlo.
Il contesto dell’incidente e l'iter giudiziario
Nel caso in esame, un lavoratore ha subito gravi lesioni durante le operazioni di carico di capriate sul rimorchio di un automezzo. La mancanza di adeguati sistemi di assicurazione delle capriate caricate alle sponde del mezzo ha portato al ribaltamento di una di esse, che ha colpito e ferito gravemente l'operaio: un trauma toracico, contusioni multiple e distorsione grave alla caviglia, per una malattia complessiva di oltre 40 giorni.
In seguito ad accertamenti, sia il tribunale sia la corte d'appello hanno attribuito la responsabilità dell'accaduto al dirigente dell’azienda con delega alla sicurezza, condannato per lesioni colpose per essere venuto meno all'obbligo di organizzare l'attività di carico degli elementi prefabbricati in modo che ne fosse garantita la stabilità in ogni fase.
Egli ha però svolto un ulteriore ricorso alla corte di Cassazione, sostenendo che l’incidente non era accaduto per una mancata organizzazione dei lavori, ma per una carenza del documento di valutazione dei rischi (DVR), la cui corretta redazione non era di sua competenza, ma del suo datore di lavoro.
In quella sede, la Corte di Cassazione ha infatti chiarito che l’obbligo di valutare i rischi e di redigere un DVR è del datore di lavoro e non è delegabile, così come stabilito esplicitamente dall’articolo 17 del D. Lgs. n. 81/2008. In questo contesto, la Corte ha sottolineato inoltre come il datore di lavoro sia il garante dell’incolumità fisica dei lavoratori, come previsto dall’articolo 2087 del Codice Civile.
Ne consegue dunque che, se il datore di lavoro non ottempera agli obblighi di tutela, la responsabilità per gli eventi lesivi ricade su di lui, in virtù del principio giuridico che stabilisce che non impedire un evento che si ha l’obbligo di impedire equivale a causarlo.
La sentenza della Corte di Cassazione
Nella sua decisione, la Corte ha evidenziato la contraddizione nella sentenza della Corte d’Appello, che da un lato riconosceva l’inadeguatezza del DVR e la mancanza di prescrizioni operative necessarie per la prevenzione del rischio di ribaltamento, e dall’altro pareva attribuire al dirigente la responsabilità di garantire tali misure. In virtù della non delegabilità della corretta redazione del DVR, il dirigente non poteva infatti essere ritenuto responsabile per la carenza rilevata, che ha causato l'incidente.
La sentenza chiarisce in seguito il ruolo del dirigente nella catena di responsabilità: Il dirigente, nella sua funzione, deve assicurarsi che le misure di sicurezza previste siano attuate e seguite dai dipendenti. Egli può ricevere delle deleghe se la struttura aziendale lo richiede, ma non quando si tratta di attività fondamentali come la redazione e l’aggiornamento del DVR, già che riguarda non solo aspetti tecnici, ma anche scelte aziendali strategiche.
La sentenza della Corte d'Appello è stata dunque annullata e rinviata per nuovo giudizio.
Considerazioni finali
Nonostante non la vicenda giudiziaria non sia ancora conclusa, la sentenza della Corte di Cassazione porta a riflettere sull'importanza della responsabilità nella gestione della sicurezza sul lavoro. L’incidente descritto e la successiva decisione della Corte non devono infatti essere letti solo come un caso giuridico, ma come un monito: la sicurezza non è mai un optional e la sua gestione deve essere presa seriamente da tutti i livelli aziendali, a partire dal datore di lavoro.
Per maggiori approfondimenti relativi al caso giudiziario preso in esame, al link qui sotto è possibile scaricare gratuitamente il testo integrale della sentenza della Corte di Cassazione fin qui citata. Buona lettura!
-
" Cassazione Penale, Sez. 4, 25 ottobre 2024, n. 39168 - Ribaltamento di un carico di capriate. Ruolo del dirigente con delega di funzioni in materia di salute e sicurezza sul lavoro"
News
Gestione dei near miss nelle piccole imprese: un'iniziativa INAIL
12/12/2024
Negli ultimi anni, la gestione dei near miss – eventi che non provocano danni fisici ai lavoratori, ma hanno il potenziale di causare infortuni – ha acquisito sempre maggiore rilevanza nel contesto della sicurezza sul lavoro (ne avevamo già parlato in questo articolo del 2023). La corretta gestione e analisi di questi eventi consentono infatti di identificare e gestire molti rischi prima che si verifichino infortuni veri e propri.
A tal proposito, l'INAIL ha recentemente presentato un documento tecnico utile per definire un modello di analisi e gestione dei near miss sostenibile anche per le piccole imprese, con l’obiettivo di avviarsi verso la creazione di un protocollo il più possibile standardizzato e capillare. Il documento si intitola “Il supporto alle aziende per la segnalazione e analisi dei near miss: proposta di un modello tecnico-organizzativo. Documento tecnico” ed è il risultato di un Protocollo d’Intesa tra INAIL e Confimi Industria.
Nel documento vengono dapprima descritti i risultati di un'indagine esplorativa condotta presso aziende che registrano i loro near miss come parte del progetto, al fine di ottenere riferimenti sullo stato attuale della situazione.
In particolare, è emerso che:
1. Per raccogliere e analizzare le segnalazioni di near miss, molte aziende si affidano a strumenti tradizionali come moduli cartacei o fogli Excel. Tuttavia, molte di esse sarebbero propense a passare a software gestionali digitalizzati, più immediati e facili da compilare.
2. Nella maggior parte dei casi, i moduli utilizzati si limitano a raccogliere le principali informazioni relative al near miss, spesso senza affrontare questioni cruciali, come il corretto uso dei DPI da parte dei lavoratori o se si trattasse di episodi già verificatisi in passato.
3. Solo il 46% delle segnalazioni registrate in tali moduli sono effettivamente classificabili come near miss: il 15% riguardano situazioni o comportamenti pericolosi, mentre il 39% consistono in infortuni veri e propri.
A seguito di questa analisi, viene illustrata un’istruzione operativa – denominata PSAT1 – per la segnalazione, l’analisi e il trattamento dei near miss, applicabile anche alle non conformità e agli infortuni. Si tratta di un modello tecnico-operativo con definizioni chiare e flussi comunicativi da seguire, volto a rendere questa attività il più semplice e sostenibile possibile nella quotidianità delle piccole imprese.
L'istruzione operativa PSAT1 si articola in tre sezioni principali:
1. Scopo e campo di applicazione: stabilisce la procedura per la segnalazione e l'analisi di near miss, non conformità e infortuni all'interno dell'azienda, con l'obiettivo di migliorare la sicurezza dei lavoratori;
2. Definizioni:
§ Near miss: incidente che non ha causato danno fisico, ma poteva farlo;
§ Non conformità: situazione di pericolo rilevabile che non ha generato incidenti, riguardante procedure, attrezzature e ambienti di lavoro;
§ Infortunio: evento che ha causato danno fisico al lavoratore.
3. Operatività: descrive i flussi comunicativi, le figure di riferimento e i moduli operativi da utilizzare, differenziati in base al tipo di analisi effettuata (vedi tabella a pagina 32 del documento a fondo pagina).
I moduli operativi variano quindi a seconda del tipo di evento (near miss, non conformità o infortunio) e risultano essere particolarmente utili per standardizzare le informazioni relative agli incidenti e alle situazioni di pericolo negli ambienti lavorativi, poiché le loro cause spesso coincidono.
Per approfondire ulteriormente l’argomento, vi invitiamo a consultare il documento integrale, scaricabile gratuitamente dal link qui sotto. Infine, mtm news saluta i suoi lettori per il 2024 e vi aspetta dopo le feste con tante novità. Buona lettura e… alla prossima!
-
“Il supporto alle aziende per la segnalazione e analisi dei near miss: proposta di un modello tecnico-organizzativo. Documento tecnico” - INAIL, 2024.
News
Agenti chimici e DPI: protezione di vie respiratorie, occhi, mani e corpo
28/11/2024
Più volte in passato abbiamo parlato dei rischi causati dagli agenti chimici presenti in alcuni ambienti di lavoro (ad esempio in questo articolo del 2021 e in questo altro articolo del 2023).
Nell’articolo di oggi, tuttavia, andremo a sottolineare il legame tra i vari tipi di rischio chimico presenti in un ambiente di lavoro e i Dispositivi di Protezione Individuale (DPI) necessari per contrastarli e prevenire incidenti e malattie. A tal proposito, il documento INAIL da cui è tratto questo articolo riguarda il rischio chimico nei laboratori di ricerca. Tuttavia, risulta molto utile anche per individuare i DPI necessari in tutti i tipi di ambienti dove il rischio chimico è elevato.
Infine, prima di procedere, ricordiamo che, oltre a dover essere marcati CE e a rispettare tutte le caratteristiche necessarie per garantire la piena conformità, i DPI devono:
§ essere adeguatamente selezionati in base al tipo di rischio presente;
§ essere custoditi in luoghi facilmente accessibili al lavoratore;
§ considerare le esigenze ergonomiche e di salute del lavoratore, senza compromettere l’efficacia o risultare un ostacolo allo svolgimento del lavoro in sicurezza.
Protezione delle vie respiratorie
I DPI per la protezione delle vie respiratorie includono diversi tipi, come i facciali filtranti antipolvere, comunemente conosciuti come “mascherine”. Questi dispositivi proteggono da polveri, fumi e nebbie, riducendo il rischio di inalazione di agenti nocivi. Sono catalogati in tre classi in base alla loro capacità di filtraggio: FFP1, FFP2 e FFP3, e possono essere monouso (NR) o riutilizzabili (R).
In situazioni in cui ci si espone a sostanze chimiche specifiche, è consigliabile utilizzare respiratori antigas dotati di filtri al carbone attivo. Questi filtri sono progettati per trattenere determinati composti chimici dannosi. Per maggiori indicazioni a riguardo, troverete una tabella riassuntiva molto esplicativa a pagina 29 del documento in fondo alla pagina.
Protezione degli occhi
Gli occhi possono essere vulnerabili a vari tipi di rischio, come spruzzi, gocce, polveri e gas. A seconda del caso, è necessario utilizzare diversi tipi di DPI, tra cui occhiali a mascherina, visiere, occhiali con visiere e occhiali antiacido. In particolari situazioni, la protezione degli occhi è integrata in un altro dispositivo di protezione, come nel caso delle maschere integrali antigas, che coprono l'intero viso.
L'aspetto essenziale è che i DPI siano realizzati con materiali in grado di resistere ai vari agenti per i quali sono progettati. Devono proteggere efficacemente la zona oculare, garantendo al contempo una visione chiara e senza distorsioni.
Protezione delle mani e del corpo
Le mani sono tra le parti del corpo generalmente più soggette al contatto con gli agenti chimici durante l'attività lavorativa. Pertanto, la scelta dei guanti è fondamentale per garantire una protezione efficace. Esistono diversi materiali tra cui scegliere, come nitrile, neoprene e PVC, ognuno con caratteristiche specifiche di resistenza agli agenti chimici.
Lo stesso vale per la protezione del corpo, che può prevedere l'uso di grembiuli, camici o tute realizzati in materiali specifici per resistere agli agenti chimici in questione. Data la varietà degli agenti e dei DPI, per maggiori dettagli suggeriamo di consultare le apposite schede di sicurezza, che possono guidare nella scelta del prodotto più adatto per ogni specifico caso.
Possiamo perciò concludere che l’importanza di avere DPI adeguati non è da sottovalutare, così come il loro uso appropriato. Infatti, in ambienti lavorativi dove il rischio chimico è presente, i DPI possono fare una differenza significativa per la salute dei lavoratori, sia a breve che a lungo termine.
Per una comprensione più approfondita e dettagliata dell'argomento, potete consultare il manuale completo pubblicato dall'INAIL, scaricabile gratuitamente al link qui sotto. Buona lettura!
-
“Rischio Chimico. Manuale informativo per la tutela della salute del personale dei laboratori di ricerca” - INAIL, seconda edizione 2023.
News
Attività di pulizia: la sicurezza delle macchine semoventi con operatore a bordo
14/11/2024
Ce lo diciamo da sempre: la sicurezza è un elemento fondamentale durante le fasi di utilizzo di una macchina o attrezzatura da lavoro, per via dei numerosi rischi di infortunio e malattie professionali che comportano. Questi rischi aumentano particolarmente quando l'operatore si trova a bordo della macchina, come nel caso delle macchine semoventi per la pulizia professionale che, sebbene siano essenziali per garantire efficienza e produttività nel processo di pulizia, comportano svariati rischi specifici per il lavoratore, come il ribaltamento, lo schiacciamento e le vibrazioni. Oltre a ciò, queste macchine costituiscono un pericolo anche per le persone presenti nell’area di lavoro durante il loro utilizzo.
A tal proposito, un documento fornito dall'INAIL e intitolato “La sanificazione nel post Pandemia. La standardizzazione dei processi. Sensibilizzare le aziende ai processi di pulizia e sanificazione come prassi standard di prevenzione dagli infortuni e dalle malattie sul lavoro” offre indicazioni preziose sui rischi e sulle buone pratiche da adottare per prevenire infortuni e malattie professionali durante l’uso di queste attrezzature.
I rischi del lavoro con macchine semoventi
L’utilizzo di macchine per la pulizia professionale con operatore a bordo espone il lavoratore a diversi rischi specifici, come il ribaltamento, lo schiacciamento e le vibrazioni e aumentano in contesti in cui ci sono persone presenti.
Per ridurli è innanzitutto fondamentale:
§ seguire le indicazioni di sicurezza riportate nei libretti d’uso e di manutenzione;
§ rispettare le procedure approntate dal datore di lavoro;
§ conformarsi alla normativa vigente in materia (D.lgs. 9 aprile 2008, n. 81).
Oltre a ciò, è molto importante anche svolgere l'attività di pulizia in sicurezza, ad esempio leggendo attentamente le etichette presenti sull’attrezzatura e sui detergenti utilizzati e adottare dispositivi di protezione individuale.
Le buone pratiche da adottare
Tra le indicazioni chiave per garantire un utilizzo sicuro delle macchine semoventi per la pulizia, troviamo:
§ Verifiche Prima dell'Uso: ogni operatore deve controllare l’efficienza del mezzo prima di iniziare il turno, inclusi livello della batteria, corretto funzionamento del clacson e dei sistemi di segnalazione e le condizioni di gomme e impianto frenante;
§ Comportamenti Sicuri Durante l’Operazione: è importante manovrare la macchina a velocità contenuta e fare attenzione in presenza di persone, così come non parcheggiarla in pendenza e seguire le corrette procedure per la manutenzione e la ricarica delle batterie;
§ Prevenzione di Rischi Aggiuntivi: quando la macchina è in funzione, è fondamentale utilizzare sempre l’indicatore lampeggiante per segnalarne la presenza e non lasciarla mai l’apparecchiatura incustodita. È inoltre vietato mescolare detergenti diversi e lavare la macchina con getti d’acqua diretti.
Cosa fare in caso di problemi
Gli operatori devono conoscere le procedure per affrontare situazioni di emergenza, come la fuoriuscita di liquidi o la formazione di schiuma. Inoltre è sempre consigliabile spegnere la macchina e accertarsi che il motore d’aspirazione si spenga in caso di fuoriuscite.
Conclusioni
L’utilizzo di macchine per la pulizia professionale semoventi richiede un elevato grado di attenzione e rispetto delle norme di sicurezza. La formazione continua e l’adozione di pratiche consolidate possono fare la differenza nel garantire non solo l'efficienza delle operazioni di pulizia, ma anche la sicurezza degli operatori e delle persone che si trovano nello stesso ambiente.
Per maggiori dettagli, come sempre al link qui sotto potete scaricare gratuitamente il documento INAIL a cui a riferimento l'articolo. Buona lettura!
-
"LA SANIFICAZIONE NEL POST PANDEMIA, LA STANDARDIZZAZIONE DEI PROCESSI. Sensibilizzare le aziende ai processi di pulizia e sanificazione come prassi standard di prevenzione dagli infortuni e dalle malattie sul lavoro" - INAIL, 2023.
News
L'importanza della formazione e della verifica nell'utilizzo delle attrezzature di lavoro
10/10/2024
La sicurezza sul lavoro è un tema di primaria importanza, specialmente in contesti dove l'uso di vari macchinari e/o e attrezzature è quotidiano. A tal proposito, un recente verdetto della Corte di Cassazione ha ribadito che il semplice possesso di manuali di istruzione non è sufficiente a garantire un ambiente di lavoro sicuro. Come riporta l'art. 71 del D.Lgs. n. 81/2008, al datore di lavoro non solo deve mantenere le attrezzature in buone condizioni di funzionamento, ma è anche tenuto a verificare che i dipendenti siano adeguatamente formati per l’utilizzo delle attrezzature e che svolgano la loro attività in conformità con le istruzioni della macchina.
La sentenza in questione riguarda un infortunio avvenuto in un cantiere edile: l'incidente ha coinvolto un lavoratore colpito da un argano staccatosi a causa di un errore nel montaggio. Al termine dell’iter giudiziario, responsabilità è stata attribuita al datore di lavoro, poiché non aveva fornito un adeguato livello di formazione e verifiche sul corretto uso delle attrezzature.
In particolare, la Corte sottolinea l’obbligo del datore di lavoro di assicurarsi che le prescrizioni antinfortunistiche siano realmente comprese dai lavoratori, andando oltre la mera disponibilità di documentazione. In altre parole, oltre a lasciare un manuale di istruzioni a disposizione è quindi necessario un intervento attivo per garantire che i dipendenti comprendano le procedure corrette, i rischi associati e come evitarli.
In questo scenario, la figura del preposto assume un'importanza cruciale per supervisionare il corretto svolgimento delle attività lavorative. Anche qui, è compito del datore di lavoro garantire che i preposti siano presenti, adeguatamente formati e competenti per svolgere il loro ruolo di supervisione. Inoltre, qualora emergano prassi operative scorrette, è sempre responsabilità del datore di lavoro intervenire, fornendo ulteriore formazione e vigilando sull'aderenza alle normative di sicurezza.
Il secondo principio messo in evidenza dalla Corte riguarda la non sostituibilità della formazione formale con l’esperienza acquisita sul campo. Ogni singolo lavoratore deve essere infatti messo nelle condizioni di utilizzare le attrezzature in modo sicuro e competente, al fine di prevenire infortuni e garantire un ambiente di lavoro sano. L'apprendimento derivante dall’attività lavorativa e dalla collaborazione tra colleghi non può dunque sostituirsi alle misure di formazione previste dalla legge.
Questi principi non solo hanno una valenza legale, ma rappresentano anche un dovere etico verso i lavoratori e le loro famiglie. Un ambiente di lavoro sicuro è essenziale non solo per rispettare le normative, ma anche per promuovere una cultura della sicurezza all'interno dell'azienda e ridurre così il rischio di infortuni.
In conclusione, il ruolo del datore di lavoro è cruciale nel garantire la sicurezza sul lavoro e le attività di formazione e verifica dell’apprendimento non devono essere viste come un mero adempimento normativo, ma come parte integrante della gestione delle risorse umane e della creazione di un ambiente di lavoro sicuro ed efficiente.
Per maggiori dettagli sul caso giudiziario qui citato, qui sotto potete scaricare gratuitamente la sentenza nella sua versione integrale. Buona lettura!
-
Cassazione Penale, Sez. Feriale, 23 agosto 2024, n. 33094 - Distacco dell'argano montato erroneamente dal preposto. Responsabilità del datore di lavoro.
News
Robotica avanzata e intelligenza artificiale: opportunità e rischi per la salute e sicurezza sul Lavoro
26/09/2024
L'evoluzione della tecnologia nel contesto lavorativo – soprattutto attraverso l'adozione della robotica avanzata e dell'intelligenza artificiale – ha portato significativi cambiamenti nelle dinamiche lavorative. Si tratta di innovazioni che offrono opportunità concrete, ma presentano anche sfide da affrontare, specialmente in relazione alla salute e sicurezza sul lavoro (SSL).
Ne parla un recente rapporto dall’Agenzia europea per la sicurezza e la salute sul lavoro (EU-OSHA) da cui è tratto l’articolo di oggi, la cui versione italiana si intitola “Robotica avanzata e sistemi basati sull’intelligenza artificiale sul luogo di lavoro: problematiche e opportunità dal punto di vista della SSL conseguenti alla loro adozione”. Si tratta di un documento di sintesi che analizza diversi fattori emersi da studi condotti dall'EU-OSHA, evidenziando le problematiche e le potenzialità derivanti dall'integrazione di queste tecnologie nei luoghi di lavoro.
Tra le opportunità più promettenti legate all’introduzione delle nuove tecnologie nel contesto lavorativo, si distingue la riduzione del carico di lavoro fisico. Nello specifico:
§ la robotica permette di automatizzare compiti fisici rischiosi o ripetitivi, il che contribuisce a ridurre il rischio di infortunio e a tutelare la salute fisica dei dipendenti;
§ i sistemi basati sull'IA possono ottimizzare il carico di lavoro cognitivo, facilitando l'elaborazione delle informazioni pertinenti e liberando tempo prezioso per attività più stimolanti.
Inoltre, entrambe queste tecnologie contribuiscono a:
§ rendere i processi lavorativi più vari, alleviando la monotonia e aumentando la soddisfazione lavorativa;
§ incrementare le competenze professionali dei dipendenti, grazie al maggior tempo da dedicare alla formazione e agli investimenti di formazione aziendali per consentire loro di utilizzare efficacemente queste nuove tecnologie. Ciò migliora le loro qualifiche e competenze, generando effetti positivi a lungo termine in termini di inquadramento professionale.
Tra le sfide principali dell’avvento delle nuove tecnologie in ambiente troviamo l’aumento dello stress lavorativo (e di conseguenza del rischio di errore e infortunio) legato principalmente a:
§ la paura della perdita del posto di lavoro legata all’avanzare dell’automazione, che può influenzare negativamente la salute mentale dei dipendenti;
§ maggiori carichi di lavoro cognitivi legati all’apprendimento di nuovi sistemi e attività, il che può portare a confusione e inefficienze nel lavoro quotidiano.
In entrambi i casi, si tratta di sfide legate alla transizione tecnologica in atto, che necessitano di adeguato supporto formativo e un monitoraggio continuo per essere affrontate con successo.
Altre difficoltà includono i rischi fisici legati all'uso dei sistemi automatizzati, che vanno valutati e gestiti accuratamente e in modo specifico con strumenti che possano adattarsi alla rapidità dell'innovazione tecnologica, in modo da tutelare la sicurezza di chi lavora al loro fianco.
Per appianare le sfide poste dall’IA è dunque essenziale:
§ adottare strategie aziendali di comunicazione efficaci che incoraggino il dialogo tra tutti i dipendenti;
§ creare una cultura aziendale che promuova la formazione continua;
§ valutare in modo specifico i rischi che via via emergono e svolgere un costante monitoraggio per mantenere la sicurezza al passo con i mutamenti tecnologici.
Tali strumenti dovrebbero considerare anche variabili psicosociali, per assicurarsi che le misure di sicurezza siano ben integrate in un quadro complessivo di benessere lavorativo.
In conclusione, l'integrazione della robotica avanzata e dell'IA nel mondo del lavoro offre una vasta gamma di opportunità e la cui corretta comprensione, gestione e monitoraggio delle problematiche a esso legate è cruciale per massimizzarne i benefici e garantire che la tecnologia si ponga come un alleato nella promozione della salute e della sicurezza sul lavoro, piuttosto che come un ostacolo.
Per consultare il documento fin qui ripreso nella sua versione integrale clicca al link qui sotto e scaricarlo gratuitamente. Buona lettura!
-
“Robotica avanzata e sistemi basati sull’intelligenza artificiale sul luogo di lavoro: problematiche e opportunità dal punto di vista della SSL conseguenti alla loro adozione”, 2023.
News
Esplosioni da polveri: prevenzione e protezione tecnica
12/09/2024
Il rischio associato alle esplosioni da polveri rappresenta una minaccia significativa in molte attività industriali, incluse quelle del settore alimentare, tessile, della plastica, dei metalli e della lavorazione del legno, come del resto dimostrano alcuni episodi passati tristemente noti in termini di infortuni professionali.
Data l'importanza di adottare misure efficaci di prevenzione e protezione contro il rischio specifico di esplosione da polvere, l'articolo di oggi intende offrire una panoramica delle principali strategie tecniche da implementare negli ambienti lavorativi che lo richiedono. Per farlo ci baseremo sul documento "La prevenzione delle esplosioni da polvere" di ARPA Piemonte, disponibile in fondo alla pagina. Anche se il documento ha qualche anno, rimane ancora una risorsa utile per i datori di lavoro, poiché consente di affrontare l'argomento in modo sistematico. corredato da casi studio che facilitano la comprensione.
Se invece hai bisogno di una mano per valutare e gestire correttamente questo rischio nel tuo ambiente di lavoro, non esitare a contattarci per una consulenza dedicata in materia.
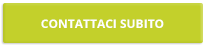
Normativa e Sistemi di Prevenzione
Il D.lgs. 81/2008 disciplina le misure di sicurezza da adottare per prevenire le atmosfere esplosive. In particolare, l'articolo 289 stabilisce che è responsabilità del datore di lavoro creare un ambiente di lavoro sicuro, prevenendo la formazione di atmosfere esplosive e mitigando gli effetti di eventuali esplosioni.
Le misure di prevenzione includono:
§ Rimozione delle Polveri: È fondamentale mantenere le superfici pulite attraverso sistemi di aspirazione centralizzati o aspiratori industriali di sicurezza (Gruppo II, Categoria 2D).
§ Prevenzione dell'Accensione: È necessario monitorare tutte le superfici che potrebbero superare le temperature critiche di accensione (MIT e LIT) e implementare misure di sicurezza che prevengano l'innesco.
§ Progettazione dei Sistemi: I sistemi di prevenzione devono funzionare in modo indipendente e garantire una sicurezza positiva, con chiari limiti di controllo delle sorgenti di accensione.
Sistemi e Misure di Protezione
Ove la prevenzione non sia sufficiente, è essenziale adottare sistemi di protezione per limitare l'impatto delle esplosioni.
Tali sistemi devono essere progettati considerando:
§ La pressione massima prevista.
§ L'indice di esplosività Kst, che indica la velocità di aumento della pressione durante un'esplosione.
Le principali misure di protezione includono:
§ Creazione di strutture in grado di resistere a esplosioni;
§ Utilizzo di sistemi di venting per dissipare le pressioni di esplosione;
§ Implementazione di sistemi attivi per neutralizzare le esplosioni in fase iniziale;
§ Adottare misure per isolare l’esplosione tramite dispositivi specifici, in modo da evitarne la propagazione. Nello specifico, tra i dispositivi di isolamento più comuni troviamo:
ü Barriere Estinguenti, che rilevano un'esplosione e iniettano agenti estinguenti nelle condutture per evitare che la pressione generata non comprometta le strutture circostanti.
ü Valvole a Chiusura Rapida, che si attivano al superamento di una certa velocità di flusso, bloccando il passaggio di materiale esplosivo.
ü Altri dispositivi di protezione includono valvole rotative, deviatori di esplosione e sistemi di ricezione del prodotto, tutti progettati in modo da garantire la sicurezza delle persone e dell'ambiente circostante.
In sostanza, la risoluzione del rischio di esplosioni da polveri richiede un approccio proattivo e multifattoriale, combinando misure di prevenzione, protezione e isolamento. È quindi fondamentale che le aziende non solo implementino queste misure, ma anche che riesaminino periodicamente le loro strategie di sicurezza in risposta a eventuali cambiamenti nel processo produttivo.
Per ulteriori dettagli sulle misure tecniche di prevenzione e protezione contro le esplosioni da polveri, si consiglia di consultare il documento da cui è tratto l’articolo, che potete scaricare gratuitamente al link qui sotto. Buona lettura!
-
"La prevenzione delle esplosioni da polvere", ARPA Piemonte, 2015.
News
Esoscheletri e sicurezza sul lavoro: la nuova norma Uni/Tr 11950 per un utilizzo consapevole
11/07/2024
Gli esoscheletri occupazionali sono dispositivi indossabili progettati per assistere e supportare fisicamente i lavoratori durante le attività lavorative, permettendo loro di ridurre lo sforzo fisico necessario a compiere determinate azioni ripetitive o gravose, prevenire il sovraccarico biomeccanico e ridurre il rischio di malattie muscoloscheletriche correlate al lavoro.
>>> Quanto ne sai di valutazione e prevenzione del sovraccarico biomeccanico? QUI trovi il nostro ultimo articolo sull’argomento!
Gli esoscheletri stanno diventando sempre più comuni negli ambienti di lavoro, siano essi attivi – ovvero dotati di motori o altre componenti elettriche – o passivi, che invece forniscono supporto sfruttando i principi meccanici.
La loro crescente diffusione è sicuramente un bene per la salute dei lavoratori, ma è anche vero che rende necessario valutarne attentamente i rischi per garantire la sicurezza di chi li indossa.
Per questo motivo, il 18 aprile 2024 è stata pubblicata la nuova norma Uni/Tr 11950, intitolata “Sicurezza e salute nell’uso degli esoscheletri occupazionali orientati ad agevolare le attività lavorative” e redatta da un gruppo di lavoro coordinato dall’INAIL con lo scopo di fornire indicazioni dettagliate sulla corretta progettazione, costruzione e utilizzo degli esoscheletri.
Nello specifico, il documento:
ü Fornisce indicazioni sulla corretta terminologia e sulle definizioni di settore;
ü Descrive i diversi tipi di esoscheletri attivi e passivi attualmente presenti sul mercato e utilizzati negli ambienti di lavoro;
ü Valuta attentamente:
- l’impatto degli esoscheletri sulla riduzione del rischio di sovraccarico biomeccanico dei lavoratori;
- i rischi residui che permangono nonostante il loro utilizzo;
- i rischi correlati all’introduzione degli esoscheletri stessi;
ü Definisce misure di prevenzione necessarie a garantire la salute e la sicurezza dei lavoratori che indossano tali dispositivi.
Per maggiori informazioni e approfondimenti visitare la pagina INAIL dedicata all’argomento. Buona lettura!
-
News
Rischio macchina: come individuare e valutare carenze nella prevenzione
27/06/2024
A chi ci legge ormai è ben noto che per garantire la sicurezza sul luogo di lavoro è essenziale svolgere una corretta valutazione del rischio e adottare misure preventive adeguate che permettano di evitare infortuni durante l'utilizzo di macchine e impianti.
Per supportare le aziende nel corretto svolgimento di queste attività e per promuovere la consapevolezza tra i lavoratori esistono diversi strumenti e azioni di supporto, promozione e vigilanza, come piani mirati di prevenzione e guide operative per la gestione di rischi più o meno specifici.
Nello specifico, oggi analizziamo la guida dell’ATS Brianza dal titolo "Utilizzo in sicurezza delle macchine. Guida per le imprese”, frutto del lavoro del gruppo "Sicurezza macchine" del Comitato di Coordinamento Provinciale di Monza e Lecco ex art. 7 D.Lgs. 81/08. Questo documento, sebbene non esaustivo, costituisce infatti un punto di partenza e un riferimento valido per impostare o revisionare la propria valutazione del rischio macchine all’interno di un’azienda.
Il documento in questione ribadisce più volte che la salute e la sicurezza non sono obiettivi statici, che vengono raggiunti una volta per tutte, ma esito di un lavoro continuo di aggiustamento della prestazione lavorativa alle variazioni del contesto in cui è svolta, che necessita quindi di sforzi e aggiornamento periodici.
Oltre a trattare numerosi aspetti relativi alle attrezzature e alla prevenzione (rischio residuo, manutenzione etc.), il documento fornisce anche indicazioni pratiche utili a svolgere correttamente ed efficacemente la compilazione di una specifica "scheda macchina" per ciascuna macchina in ingresso, contenente l'elenco dei requisiti di sicurezza, i controlli necessari per garantirne l'efficienza e gli interventi di manutenzione da eseguire.
La guida include inoltre diversi allegati contenenti esempi di schede e check list da utilizzare nello svolgimento dell’attività di valutazione. In particolare, l’allegato U contiene una vera e propria scheda di autovalutazione aziendale che, oltre a fornire numerose indicazioni in modo pratico e sintetico, contiene un prezioso elenco di domande a cui l’azienda può rispondere per valutare la propria capacità di prevenire i rischi legati all'uso delle macchine, come ad esempio:
ü È presente in azienda un elenco (censimento) di tutte le macchine/impianti?
ü Per ogni macchina in ingresso è compilata una specifica check list di controllo del buon acquisto/installazione e completezza documentale?
ü Quali sono le misure che s’intraprendono in azienda prima di mettere in servizio una macchina?
ü Come è stata effettuata la valutazione dei rischi correlati alle macchine? La valutazione dei rischi correlati alle macchine prende in considerazione le diverse attività connesse al loro utilizzo.
L’allegato P fornisce infine specifiche indicazioni riguardo alla formazione e addestramento dei lavoratori, riassumibili nel seguente schema a punti:
1. Prima di adibire il lavoratore all’utilizzo di macchine:
a) Formazione generale: Concetti di rischio, danno, prevenzione, protezione, organizzazione della prevenzione aziendale, diritti e doveri dei vari soggetti aziendali, organi di vigilanza, controllo, assistenza;
b) Formazione specifica di base: Rischi riferiti alle mansioni e ai possibili danni e alle conseguenti misure e procedure di prevenzione e protezione caratteristici del settore o comparto di appartenenza dell’azienda e con riferimento agli esiti del Documento di Valutazione dei Rischi (DVR) aziendale.
2. Al momento dell’uso della macchina:
a) Formazione integrativa: Rischi derivanti dall’utilizzo di una determinata macchina nello specifico contesto aziendale;
b) Addestramento: modalità d’utilizzo in sicurezza della macchina, comprese le operazioni di manutenzione ordinaria affidate all’operatore (pulizia etc.).
3. Entro 5 anni dall’erogazione della formazione specifica:
a) Aggiornamento della formazione specifica: Approfondimenti giuridico-normativi, aggiornamenti tecnici sulle fonti di rischio ai quali sono esposti e sulle relative misure di prevenzione, aggiornamento sull’ organizzazione e gestione della sicurezza in azienda.
In conclusione, la guida fornisce una serie di strumenti, tra cui una scheda di autovalutazione aziendale, per aiutare le aziende a condurre una valutazione accurata dei rischi presenti nel loro ambiente lavorativo. Al link qui sotto la potete scaricarla gratuitamente direttamente dal sito dell'ATS Brianza, così come tutti gli allegati in formato editabile.
https://www.ats-brianza.it/it/approfondimenti-sui-rischi-lavorativi-specifici-piani-mirati-di-prevenzione-faq-e-informazioni/23-master-category/cat-servizio-imprese/2246-p-m-sicurezza-macchine.html
Cliccando QUI e compilando il modulo potete invece contattarci per ricevere il nostro supporto professionale in materia. Buona lettura!
-
News
Guida ai dispositivi di protezione individuale per il lavoro con agenti chimici pericolosi
23/05/2024
Se è vero che, quando si tratta di sicurezza sul lavoro, prevenire è sempre meglio che curare, ciò vale ancora di più quando si tratta di agenti chimici pericolosi. Ogni giorno, innumerevoli lavoratori sono esposti a rischi potenzialmente nocivi per la salute, derivanti dall'uso di agenti chimici. Nonostante le misure preventive e le protezioni collettive, spesso è necessario ricorrere ai Dispositivi di Protezione Individuale per garantire un'adeguata protezione.
Nel complesso quadro normativo e delle buone pratiche in materia, il documento Inail “Agenti chimici pericolosi. Istruzioni ad uso dei lavoratori” – a cura di Elisabetta Barbassa, Maria Rosaria Fizzano e Alessandra Menicoccia e aggiornato nel 2023 – risulta essere particolarmente prezioso per orientare lavoratori e datari di lavoro nella scelta e nell'uso dei Dispositivi di Protezione Individuale o DPI.
Obblighi e categorie dei DPI
Il documento in questione chiarisce innanzitutto gli obblighi relativi ai DPI sottolineando che devono essere marcati CE, adeguati al rischio specifico, che non devono introdurre nuovi pericoli e si devono adattare al lavoratore, preservando la propria efficacia anche in caso di uso congiunto di più dispositivi. Inoltre, il documento distingue i DPI da altri tipi di attrezzature, come gli indumenti di lavoro ordinari e le apparecchiature di protezione personale per i servizi di soccorso o le forze dell'ordine.
La classificazione dei DPI viene poi suddivisa in tre categorie, a seconda del livello di rischio:
· Categoria I: Rischi minimi, come lesioni superficiali o condizioni atmosferiche non estreme.
· Categoria II: Rischi non compresi nelle altre due categorie.
· Categoria III: Rischi che possono causare danni gravissimi, inclusi agenti chimici e biologici pericolosi, carenza di ossigeno e radiazioni ionizzanti.
La scelta e le istruzioni dei DPI
Per svolgere una corretta valutazione del rischio, il datore di lavoro deve individuare i DPI più adatti, basandosi sulle caratteristiche tecniche indicate dal fabbricante. La scelta deve essere guidata dall'analisi del rischio e dal confronto con l'offerta di mercato, nel pieno rispetto delle norme tecniche più aggiornate. Ogni DPI deve essere accompagnato da istruzioni dettagliate e comprensibili per l'uso, la manutenzione e la pulizia, così come informazioni sulla vita utile del prodotto.
A tal proposito, oltre a fornire linee guida generali Il documento INAIL in questione fornisce informazioni su DPI per la protezione specifica di varie parti del corpo, per la protezione delle vie respiratorie e per quella del corpo intero.
In conclusione, gli agenti chimici pericolosi richiedono un'attenzione particolare e l'utilizzo dei DPI si rivela una misura imprescindibile nella protezione quotidiana dei lavoratori. La cultura della prevenzione passa anche attraverso la corretta informazione e formazione e il documento INAIL fin qui analizzato è un punto di riferimento essenziale per tutti gli attori coinvolti nel mantenere gli ambienti lavorativi sicuri e salutevoli.
Per saperne di più sull’argomento invitiamo quindi alla lettura integrale del documento, che come sempre potete scaricare gratuitamente al link qui sotto. Buona lettura!
-
“Agenti chimici pericolosi. Istruzioni ad uso dei lavoratori” – Doc. INAIL a cura di Elisabetta Barbassa, Maria Rosaria Fizzano e Alessandra Menicoccia , 2023.
News
Responsabilità condivisa e sicurezza macchine: una sentenza rilevante per gli imprenditori
18/04/2024
In un recente verdetto della IV Sezione penale della Corte di Cassazione, emerge un chiaro messaggio per gli imprenditori e i fornitori del settore delle macchine industriali: la sicurezza deve essere una priorità condivisa e la responsabilità non è limitata all'operatore che ha messo in funzione la macchina, ma si estende anche a tutti coloro coinvolti nella costruzione, installazione, vendita o cessione della stessa.
Fatto e iter giudiziario
Il fatto riguarda un incidente su un cantiere edile: un lavoratore è rimasto ferito in un cantiere edile dopo che un pannello coibentato si è staccato dalla presa di una ventosa utilizzata per il sollevamento con una gru.
Questa dinamica conduce quindi ad analizzare le seguenti responsabilità:
· il cedente della ventosa, ossia la società che ha fornito l’attrezzatura al lavoratore, poiché non ha verificato le condizioni di sicurezza prima della consegna;
· il lavoratore, che ha utilizzato l'apparecchio senza una preventiva verifica dello stato delle guarnizioni o delle superfici applicative.
Il legale rappresentante della società è stato accusato di lesioni colpose. Dopo aver esaminato gli elementi e respinto le difese che imputavano il danneggiamento a cause alternative come un errore umano o un danneggiamento durante il trasporto dopo l'infortunio, il giudice ha confermato la colpevolezza del rappresentante della società.
Il Tribunale si è espresso sulla base delle testimonianze, della documentazione e di consulenze tecniche, a partire dalle quali è stato stabilito che la ventosa aveva difetti preesistenti che non erano conseguenza di un utilizzo nei giorni precedenti l'incidente e che non sono state fornire istruzioni adeguate ai lavoratori prima dell’uso.
La Corte d'Appello ha poi confermato la sentenza, ritenendo che vi fosse stata negligenza nella manutenzione della ventosa e che le difese presentate fossero irrilevanti rispetto all'accusa di cattivo stato di manutenzione, che ha portato alle lesioni del lavoratore.
Conclusioni
Questa sentenza ribadisce che la responsabilità in materia di sicurezza sul lavoro è multidimensionale e coinvolge molteplici attori.
In particolare il messaggio per le imprese è inequivocabile: la collaborazione nella sicurezza non è solo una prassi etica ma anche una necessità giuridica, poiché un’inadempienza può portare a sanzioni penali e civili.
Per questo motivo, tutte le aziende coinvolte nel ciclo di vita di una macchina devono attuare tutte le azioni necessarie per garantire che possa essere utilizzata senza porre in pericolo la salute dei lavoratori e, di conseguenza, anche la propria posizione legale.
Per maggiori dettagli riguardanti questo caso giudiziario, al link qui sotto è possibile scaricare la sentenza integrale. Se invece hai dubbi sulla sicurezza delle tue macchine, contattaci subito CLICCANDO QUI e raccontandoci brevemente la situazione. Buona lettura!
-
Cassazione Penale, Sez. 4, 14 marzo 2024, n. 10665 - Posizioni di garanzia_ fabbricante_venditore_noleggiatore_concedente del macchinario e utilizzatore_datore di lavoro.pdf
News
Nuovo bando 2023-2024 per finanziamenti a fondo perduto alle imprese: ecco a chi si rivolge e le modalità di accesso
14/03/2024
A dicembre 2023, l’INAIL ha pubblicato il nuovo Bando ISI 2023 – 2024 che permette alle imprese italiane di ottenere finanziamenti a fondo perduto da investire in progetti di miglioramento delle condizioni di salute e sicurezza nei luoghi di lavoro.
A chi è rivolto?
Il bando si rivolge a tutte le imprese italiane operanti nei settori del commercio, industria, artigianato, agricoltura e del terzo settore, ad esclusione di:
§ quelle aziende che hanno già partecipato al Bando INAIL 2020, 2021 e 2022, fatta eccezione per quelle che avevano presentato un progetto per l’adozione di modelli organizzativi e di responsabilità sociale.
§ le micro e piccole imprese agricole che hanno già ricevuto l’incentivo ISI Inail 2021 e 2022 per l’Asse 5, o l’incentivo ISI Inail Agricoltura 2019/2020.
In cosa consiste il contributo ottenuto?
La misura del contributo varia da un importo minimo di 5.000 euro fino a un massimo di 130.000 euro e corrisponde al 65% della spesa d'investimento ammissibile, fino a un massimo di 200.000 euro. Ad esempio, per una spesa di investimento di 200.000 euro, il contributo massimo ammissibile sarà di 130.000 euro.
È importante sottolineare che si tratta di un finanziamento a fondo perduto e non di un credito d'imposta, pertanto l'importo assegnato verrà direttamente accreditato sul conto corrente dell'impresa beneficiaria.
Quali sono le spese ammissibili?
Gli interventi che rientrano nel Bando riguardano principalmente tre ambiti:
ü Investimenti in attrezzature e macchinari nuovi, come macchinari a controllo numerico, impianti di aspirazione di fumi, insonorizzazione di pareti, gru, macchinari per la movimentazione di carichi, escavatori e altro ancora.
ü Impianti che migliorano le condizioni di salute per i lavoratori, come ad esempio aspirazione di fumi, insonorizzazione, e attrezzature che riducono la movimentazione manuale, le vibrazioni e il rumore.
ü Rimozione dell'amianto, comprensiva delle spese di rifacimento del tetto.
Requisiti e modalità di accesso
Per accedere al bando è necessario:
ü verificare di rientrare nei requisiti di accesso
ü presentare domanda a partire dal 15 aprile 2024 e non oltre il 30 maggio 2024 ore 18:00 seguendo l’iter indicato.
È inoltre importante tenere a mente che:
§ Le imprese possono presentare un solo progetto riguardante una sola unità produttiva per una sola tipologia di progetto
§ Il progetto non deve essere già in corso d’opera
§ sono ammesse a finanziamento anche le spese direttamente necessarie alla realizzazione del progetto e le spese accessorie o strumentali funzionali e indispensabili per la realizzazione dello stesso.
Per maggiori informazioni rimandiamo alla pagina dedicata del sito dell’INAIL. Buona lettura!
-
News
Classificazione zone ATEX: cos’è cambiato dal 23 gennaio 2024
29/02/2024
A partire dal 23 gennaio 2024, le aziende con zone a rischio esplosione devono aggiornare obbligatoriamente il documento di classificazione dei luoghi per adeguarsi alla nuova normativa vigente.
A tal proposito è bene specificare che questo aggiornamento riguarda la norma CEI EN 60079-10-1, che tratta la zonizzazione degli ambienti in cui c'è o ci può essere presenza di atmosfere potenzialmente esplosive per via di gas, vapori o nebbie. Per gli ambienti classificati a causa della presenza di polveri che possono generare atmosfere potenzialmente esplosive si mantiene invece come norma di riferimento la CEI EN 60079-10-2, la cui ultima edizione risale al 2015.
Di seguito elenchiamo quindi in modo sintetico i vari passaggi evolutivi del quadro normativo e i cambiamenti introdotti per quanto riguarda la classificazione degli ambienti in cui è o vi può essere presenza di atmosfere potenzialmente esplosive dovute a gas, vapori o nebbie.
Evoluzione normativa
Fino al 2016, per la classificazione di questo tipo di zone pericolose si è fatto riferimento alle linee guida CEI 31-35 e 31-35/A, che si basavano sulla norma CEI EN 60079-10-1 del 2010. Nel 2016 è stata poi pubblicata la nuova edizione della norma, che il 14/10/2018 ha definitivamente sostituito la precedente. Tuttavia, le guide CEI non sono mai state aggiornate di conseguenza, generando incertezza normativa.
La situazione è in parte stata mitigata dal rapporto tecnico UNI CEI TR 11798 del 2020, che forniva esempi applicativi per la classificazione dei luoghi a rischio esplosione per la presenza di gas sulla base della norma CEI EN 60079-10-1 del 2016.
La normativa oggi: cos’è cambiato il 23 gennaio 2024?
Anche se ad oggi i lavori per aggiornare le linee guida abrogate non sono ancora iniziati, nel 2021 è stata rinnovata la norma CEI EN IEC 60079-10-1, che segna l’abrogazione definitiva della versione 2016 in data 22 gennaio 2024. Dunque, a partire dal 23 gennaio 2024, è applicabile solo l'edizione 2021 della norma, che contiene le procedure aggiornate per calcolare le dimensioni delle zone pericolose. Sempre a gennaio 2024 è stato allineato a quest’ultima edizione della norma anche il rapporto tecnico del 2020 sopra citato.
Ad ogni modo, a partire dal 23 gennaio scorso è obbligatorio aggiornare la documentazione di valutazione del pericolo di esplosione alle ultime disposizioni normative. In particolare, per quanto riguarda gas, vapori e nebbie infiammabili l’edizione del 2021 della norma CEI EN IEC 60079-10-1 ha aggiornato le procedure per calcolare le dimensioni delle zone pericolose, il che richiede un’adeguata modifica dei documenti aziendali per evitare le sanzioni previste dalla normativa.
Siete sicuri che la vostra classificazione delle zone in cui è probabile si formino atmosfere potenzialmente esplosive sia aggiornata e conforme alla nuova normativa? Se la risposta è no non aspettare oltre, clicca qui e contattaci per una consulenza dedicata, oppure chiamaci al +39 039 28 48 437. Ti aspettiamo!
-
News
Valutare il sovraccarico biomeccanico: la metodologia check-list OCRA
15/02/2024
Come alcuni tra i nostri lettori di vecchia data ricorderanno a maggio 2023 abbiamo condiviso con voi la notizia della recente pubblicazione terzo volume INAIL di schede per la valutazione del rischio di sovraccarico biomeccanico degli arti superiori: tali schede hanno l’obiettivo di migliorare l’approccio alla valutazione di questo specifico rischio, che rappresenta una delle più diffuse cause di malattia professionale.
Se l’articolo dello scorso anno (che trovate QUI) si soffermava sui compiti trattati nelle singole schede e i contenuti da esse riportati, oggi ci soffermiamo invece su una delle metodologie utilizzate per valutare tali compiti: la check list OCRA derivata dal metodo OCRA Index (Occupational Ripetitive Action Index) e riportata dalla norma tecnica UNI ISO 11228-3:2009, poi integrata dalla ISO/TR 12295:2014.
Rispetto ad altre metodologie, la check list OCRA è considerata un riferimento internazionale in quanto tiene conto di tutti i fattori correlabili al sovraccarico biomeccanico degli arti superiori evidenziati dalla letteratura di settore. Nello specifico, considera i seguenti fattori di rischio:
ü carenza di periodi di recupero;
ü frequenza di azione;
ü applicazione di forza;
ü assunzione di posture incongrue e/o presenza di stereotipia;
ü fattori complementari, come vibrazioni meccaniche al sistema mano-braccio, esposizione a basse temperature, effettuazione di lavori di precisione, ecc.
Inoltre specifica che, per rendere confrontabili le stime valutative ottenute e facilitarne l’utilizzo, sono state considerate le seguenti modalità operative:
ü operatore destrimane;
ü svolgimento del compito in esame per una giornata lavorativa di 8 ore;
ü presenza di 2 pause da 10 minuti ciascuna – la prima inserita a metà mattinata e la seconda a metà pomeriggio – in aggiunta alla pausa mensa, che è comunque esterna all’orario di lavoro.
Si sottolinea poi come i risultati stimati siano riferibili alle specifiche caratteristiche descritte per ciascun compito: layout, macchinari e attrezzature utilizzate, organizzazione del lavoro, ciclo di lavoro, etc. Per questo motivo, per un corretto utilizzo dei dati illustrati nelle schede è necessario tener conto delle particolarità di ogni singola realtà lavorativa esaminata.
Ulteriori vantaggi della metodologia check list OCRA sono:
ü fornisce una previsione dell’insorgenza di disordini muscolo-scheletrici lavoro-correlati degli arti superiori (UL-WMSD) nella popolazione lavorativa;
ü ai fini della stima del rischio, prende in esame anche la durata netta giornaliera del lavoro ripetitivo;
ü offre la possibilità di progettare preventivamente una postazione di lavoro e un metodo di lavoro che possa al meglio tutelare la salute del lavoratore.
Il valore ottenuto dall’applicazione di tale metodologia corrisponde poi a una delle fasce di rischio riportate nella seguente tabella del documento.
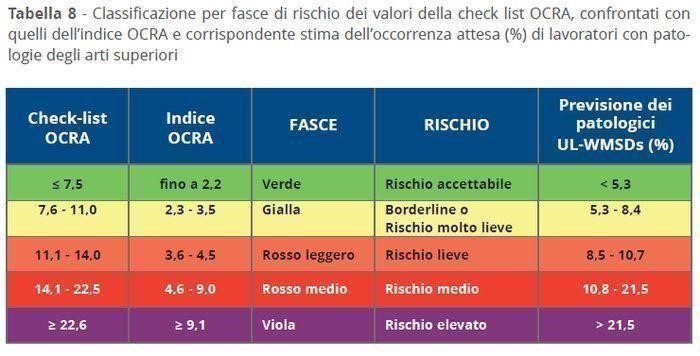
Per approfondimenti in merito alla metodologia check list OCRA di analisi del rischio da sovraccarico biomeccanico degli arti superiori nei compiti sulle schede INAIL, al link qui sotto potete scaricare gratuitamente la versione integrale del terzo volume INAIL fin qui analizzato. Buona lettura!
-
“Schede di rischio da sovraccarico biomeccanico degli arti superiori nei comparti della piccola industria, dell’artigianato e dell’agricoltura – Volume III”, INAIL, Febbraio 2023.
News
Come valutare la qualità dell’aria nei luoghi di lavoro
25/01/2024
Ormai sappiamo bene che la presenza di condizioni ambientali non ottimali può interferire negativamente con le attività lavorative, portando a maggiori distrazioni, rallentamenti, errori e quindi incidenti. Anche se può sembrare banale o scontato, tra i vari fattori che concorrono a definire la qualità di ambiente di lavoro quello dell'aria respirata è fondamentale, in quanto influisce ampiamente sul benessere e la produttività dei lavoratori.
Ed è con queste premesse che nasce la recente pubblicazione dell'Inail intitolata "La valutazione della qualità dell'aria nei luoghi di lavoro. Benessere, performance", il cui scopo è fornire una valida sintesi delle conoscenze e della legislazione attuale in materia, in modo da agevolare le aziende nella valutazione di questo aspetto all’interno dei loro ambienti lavorativi.
Valutare la qualità dell'aria nei luoghi di lavoro è infatti una sfida complessa, poiché l’aria presenta molte e diverse sostanze al suo interno, provenienti sia dalla respirazione umana che da materiali o agenti esterni. Ciò comporta la necessità di adottare approcci e metodologie specifiche per una corretta valutazione.
In particolare, il Documento si concentra principalmente su un approccio prestazionale – ovvero basato sulla misurazione delle concentrazioni di inquinanti – piuttosto che su quello prescrittivo, basato sulla portata d’aria immessa nell’ambiente. Questa scelta è legata al fatto che, sebbene la ventilazione di un ambiente sia importante per evitare il ristagno di sostanze dannose nell’aria, da sola non rappresenta l’approccio più coerente per valutare la qualità dell’aria in un ambiente e i rischi per la salute che ne derivano.
Dal punto di vista legislativo, il documento rimanda all’Allegato IV del D.Lgs. 81/2008, che contiene indicazioni riguardo alla valutazione della qualità dell'aria. In particolare, dice che:
1. Nei luoghi di lavoro chiusi sia garantita un'aria salubre in quantità sufficiente, anche attraverso impianti di areazione, che devono essere sempre mantenuti funzionanti, periodicamente controllati e sottoposti a pulizia e sanificazione per tutelare la salute dei lavoratori;
2. Devono essere evitati flussi d'aria fastidiosi per i lavoratori e deve essere eliminata rapidamente qualsiasi sporcizia che possa rappresentare un pericolo per la salute;
3. La valutazione della qualità dell'aria deve essere inserita nel documento di valutazione dei rischi per la salute e sicurezza (DVR) e devono essere indicati tutti gli elementi rilevanti: la data della valutazione, i dati del personale qualificato che ha effettuato la valutazione, i dati del rappresentante dei lavoratori per la sicurezza consultato, i risultati delle misurazioni eseguite e le misure tecniche e organizzative da adottare per eliminare o ridurre eventuali disagi;
4. La relazione tecnica va conservata dall'azienda e resa disponibile agli organi di vigilanza.
Il documento Inail fornisce infine informazioni sulle legislazioni e le normative tecniche degli altri Paesi europei, offrendo una panoramica più ampia sul tema.
Se vuoi approfondire l’argomento, qui sotto trovi la versione integrale del documento in questione, che come sempre è scaricabile gratuitamente. Buona lettura!
-
"La valutazione della qualità dell'aria nei luoghi di lavoro. Benessere, performance" - Inail: direzione regionale Campania, 2023.
News
Progettazione e costruzione dei ripari sulla macchina: la norma UNI EN ISO 14120: 2015
31/03/2016
Alla fine del 2015 è stata pubblicata anche in Italia la norma EN ISO 14120: 2015 relativa alla progettazione e costruzione dei ripari fissi e mobili su una macchina. Questa norma, che garantirà la presunzione di conformità alla Direttiva Macchine 2006/42/CE non appena sarà pubblicata sulla Gazzetta Ufficiale dell’Unione Europea (OJEU), specifica i requisiti generali per la progettazione, costruzione e selezione di ripari forniti per proteggere le persone dai pericoli meccanici. Vediamo qui le principali novità della norma.
MTM Consulting s.r.l. è in grado di seguire i fabbricanti di macchine nella stesura del fascicolo tecnico e, in particolare, della valutazione dei rischi, garantendo loro un continuo ed efficace aggiornamento normativo al fine di individuare le soluzioni tecniche migliori e rappresentative dello stato dell’arte vigente che possano ridurre i rischi correlati alle fasi di vita della macchina.
La norma UNI EN ISO 14120: 2015 – “Sicurezza del macchinario - Ripari - Requisiti generali per la progettazione e la costruzione di ripari fissi e mobili” sostituisce la precedente UNI EN 953: 2009 e specifica i requisiti generali per la progettazione, costruzione e selezione di ripari forniti per proteggere le persone dai pericoli meccanici. Prossimamente la norma sarà pubblicata sulla Gazzetta Ufficiale dell’Unione Europea (OJEU) garantendo così la presunzione di conformità ai correlati requisiti essenziali di sicurezza della Direttiva Macchine 2006/42/CE. Questa norma è fondamentale nella progettazione della macchina in quanto fornisce al fabbricante le indicazioni, rappresentative dell’attuale stato dell’arte, relativamente alla progettazione, alla costruzione e alla scelta dei ripari (fissi e mobili) che devono essere posizionati sulla macchina al fine di proteggere l’operatore dai pericoli meccanici presenti.
Un riparo è definito come una barriera fisica, progettata come parte della macchina, con lo scopo di fornire protezione all’operatore. Le tipologie di ripari analizzate dalla norma sono:
- Riparo fisso, tra cui si possono distinguere i carter (ripari fissati alla macchina) e i perimetrali,
- Riparo mobile (necessariamente associato ad un dispositivo di interblocco, con o senza bloccaggio, come analizzati nella norma UNI EN ISO 14119: 2013)
- Ripari motorizzati
- Ripari regolabili
- Ripari con comando dell’avviamento.
Per ognuna delle categorie di ripari sopra indicata, la norma fornisce una serie di indicazioni progettuali e costruttive che il fabbricante deve adottare al fine di realizzare un riparo che sia considerato efficace.
Inoltre, la norma analizza l’aspetto della corretta scelta del tipo di riparo in funzione del pericolo esistente sulla macchina e della situazione pericolosa in cui l’operatore potrebbe trovarsi. Infatti, un tipo di riparo non vale l’altro e la scelta del riparo da adottare deve essere, anzitutto, conforme alla frequenza di intervento prevista da parte dell’operatore in quella zona da proteggere. In linea di principio, se l’operatore non deve accedere alla zona pericolosa durante il normale funzionamento allora la scelta deve ricadere sui ripari fissi; qualora l’accesso alla zona pericolosa sia richiesto per attività di manutenzione, messa a punto, regolazione, pulizia, ecc. allora si dovranno scegliere preferibilmente ripari interbloccati; in ultimo, qualora l’operatore debba accedere alla zona pericolosa durante il normale funzionamento, le scelte possono essere diverse (ripari mobili interbloccati, ripari con chiusura automatica, ecc.) ma mai pari ad un riparo fisso. In quest’ultimo caso, inoltre, la protezione dell’operatore dovrà essere garantita secondo le disposizioni del requisito 1.2.5 dell’Allegato I della Direttiva Macchine 2006/42/CE in merito alla selezione del modo di comando e/o funzionamento (anche in accordo alla correlate disposizioni della norma UNI EN ISO 12100: 2010).
Il secondo aspetto da valutare è la tipologia di elementi mobili che è necessario proteggere: parti mobili di trasmissione del moto (pulegge, cinghie, ingranaggi, ecc.) richiedono scelte differenti relativamente ai ripari rispetto alle parti mobili che partecipano alla lavorazione (come utensili, cilindri, rulli, ecc.).
Un ultimo aspetto interessante di questa nuova norma sono le modalità di prova della resistenza dei ripari, sia per gli urti da parte di elementi delle macchine che da parte di persone che cadono contro i ripari:
- Il test del proiettile è una prova che testa la resistenza del riparo contro gli impatti dall’interno della zona pericolosa.
- Il test del pendolo è usato per testare la resistenza dei ripari contro urti dall'esterno della zona pericolosa protetta e dall'interno della zona pericolosa protetta.
[A cura di: Ing. Massimo Granchi - Ing. Christian Trinastich]
-
News
La Valutazione del Rischio Chimico: il rinnovato metodo Inforisk
16/02/2016
La letteratura in merito ai metodi analitici quantitativi per la valutazione preliminare del rischio di esposizione ad agenti chimici è molto estesa e propone varie metodologie, di derivazione internazionale o elaborate da enti territoriali nazionali.
Dopo la revisione effettuata nel corso del 2013 e perfezionata con la pubblicazione di “Quesiti e istruzioni per il corretto uso” nel 2015, il metodo Inforisk elaborato dalla Regione Piemonte risulta essere il metodo più completo e maggiormente aderente alle richieste del D.Lgs. 81/2008 allo specifico Titolo IX.
MTM Consulting può seguire la tua azienda nell’effettuare la valutazione preliminare del rischio chimico, programmare eventuali analisi ambientali ed elaborare le migliori misure di prevenzione e protezione per i tuoi addetti.
Lo scopo dei metodi analitici semplificati è quello di effettuare la valutazione preliminare del rischio, così come identificata del D.Lgs. 81/2008: “ricognizione iniziale finalizzata alla determinazione della presenza di agenti chimici la cui esposizione può presentare anche un minimo livello di rischio”. Da questa ricognizione iniziale deve perciò emergere, per ogni sostanza pericolosa alla quale ogni addetto è esposto, se tale esposizione può generare un rischio da considerarsi “Basso per la salute ed Irrilevante per la sicurezza” oppure se sono necessarie ulteriori indagini, a questo punto di natura strumentale, o se la pericolosità dell’esposizione sia conclamata e quindi urge modificare sostanze impiegate, metodi di lavoro o dispositivi di protezione.
Con la pubblicazione del Testo Unico D.Lgs. 81/2008 i vari metodi analitici al tempo disponibili ed ufficiali risultarono mancanti in vari aspetti, secondo quanto invece ora richiesto dalla normativa. Il metodo Inforisk ad esempio mancava di una valutazione dipendente dal tipo di esposizione, ovvero una valutazione che individuasse anche il comparto fisiologico sul quale l’agente chimico possa avere effetti negativi. Altri metodi analitici ad esempio proponevano vari indici di rischio in funzione del comparto fisiologico, ma non consideravano la durata dell’esposizione o la quantità di agente chimico alla quale è possibile essere esposti, tutte richieste invece esplicitamente formulate dal D.Lgs. 81/2008 all’Articolo 223.
Il rinnovato metodo Inforisk introduce invece il calcolo di due indici di rischio, Indice di Rischio Inalatorio e Indice di Rischio Cutaneo, dai quali calcolare un Indice di Rischio globale.
Il rinnovato metodo Inforisk parte dalla valutazione della pericolosità del singolo componente, la quale si evince dalla Schede di Sicurezza (MSDS) del singolo prodotto. Questo dato viene impiegato per calcolare un Indice di Rischio Inalatorio sulla base di:
- durata dell’esposizione;
- quantità di prodotto alla quale si è esposti;
- tipo di processo;
- proprietà fisiche del singolo prodotto.
In modo analogo il dato sulla pericolosità del singolo componente viene impiegato per calcolare un Indice di Rischio Cutaneo sulla base di:
- durata dell’esposizione;
- quantità di prodotto alla quale si è esposti;
- modalità di contatto cutaneo;
- quantità di superficie esposta.
Tali due indici vengono sommati tramite somma vettoriale per generare l’Indice di Rischio Globale.
[A cura di: Ing. Massimo Granchi, Ing. Riccardo Bozzo]
-
News
Utilizzo delle banche dati nella valutazione del rischio rumore
25/01/2016
Nell’ambito della valutazione di tutti i possibili rischi correlati alle mansioni lavorative e alle attività presenti in azienda, la valutazione del rischio rumore comporta la necessità di effettuare delle misurazioni con opportuni strumenti (fonometro), secondo procedure standardizzate (definite dalle norme tecniche) in corrispondenza di tutte le attività eseguite dagli operatori. Una recente modifica al D.Lgs. 81/2008, in certe occasioni, prevede la possibilità di utilizzare specifiche banche dati sul rumore approvate dalla Commissione Consultiva Permanente.
MTM Consulting s.r.l. è in grado di seguire i datori di lavoro nella analisi e valutazione di tutti i rischi esistenti in azienda, compreso il rischio rumore, effettuando specifiche misurazioni fonometriche che evidenzino il valore di esposizione dell’operatore e il correlato valore di incertezza.
Il Decreto Legislativo 14 settembre 2015, n. 151 recante “Disposizioni di razionalizzazione e semplificazione delle procedure e degli adempimenti a carico di cittadini e imprese e altre disposizioni in materia di rapporto di lavoro e pari opportunità”, ha modificato il D.Lgs. 81/2008, tra le altre cose, anche per quanto concerne gli agenti fisici (Titolo VIII) e, nello specifico, per quanto attiene alla stima del rumore emesso da attrezzature di lavoro, macchine e impianti al fine della valutazione del rischio rumore.
In particolare, la modifica riguarda l’art. 190 del D.Lgs. 81/08 dove il comma 5-bis è stato sostituito con il seguente: “L’emissione sonora di attrezzature di lavoro, macchine e impianti può essere stimata in fase preventiva facendo riferimento alle banche dati sul rumore approvate dalla Commissione consultiva permanente di cui all’articolo 6, riportando la fonte documentale cui si è fatto riferimento”. In definitiva, il nuovo comma 5-bis fornisce la possibilità, almeno in via preventiva, di utilizzare specifiche banche dati approvate dalla Commissione Consultiva Permanente (per la salute e sicurezza sul lavoro) per stimare l’emissione sonora di specifiche macchine, impianti e attrezzature di lavoro. La differenza rispetto al comma 5-bis precedente è importante in quanto precedentemente veniva data la possibilità, sempre in via preventiva, di fare riferimento “a livelli di rumore standard individuati da studi e misurazioni la cui validità è riconosciuta dalla Commissione consultiva permanente”.
L’impostazione attuale prevede, invece, una vera e propria banca dati dove sono raccolte le indicazioni relative all’emissione sonora di diverse e specifiche attrezzature di lavoro. Al momento l’unica banca dati validata a cui fare riferimento è quella realizzata dal CPT Torino e relativa ai cantieri edili.
La possibilità di indirizzarsi ai valori stimati e raccolti all’interno della banca dati, invece di effettuare misurazioni del rumore sul campo è rivolta esclusivamente ai casi nei quali risulti impossibile disporre di valori misurati sul campo. Infatti, già durante la redazione del Piano di Sicurezza e Coordinamento, in alcuni casi si può essere nella condizione di non sapere quali aziende interverranno nel cantiere e, dunque, quali specifiche attrezzature saranno utilizzate. In questi casi, dunque, diventerebbe impossibile effettuare fisicamente specifiche valutazioni dell’emissione sonora al fine di valutare il rischio rumore in cantiere.
Per questo motivo, già in fase di redazione del P.S.C., durante la progettazione dell’opera, è possibile riferirsi ai dati di emissione raccolti nella banca dati con l'obiettivo primario di permettere la pianificazione delle misure di prevenzione e protezione già in fase preventiva rispetto all'inizio dell'attività.
In definitiva, in tutte le aziende che non rientrano nell’ambito dei cantieri edili è sempre necessario procedere ad una misurazione su campo del rumore emesso dalle macchine, impianti e attrezzature di lavoro utilizzate secondo le procedure definite dalle norme tecniche di riferimento.
[A cura di: ing. Christian Trinastich per mtm consulting s.r.l.]
-
News
Passaggio dalla Direttiva Atex 94/9/CE alla nuova 2014/34/UE
17/12/2015
Da più di un anno è stata pubblicata la nuova Direttiva Atex 2014/34/UE che risulterà applicabile a partire dal 20 aprile 2016. Fino a questa data resta applicabile l’attuale direttiva Atex 94/9/CE. Sebbene non vi siano differenze sostanziali tra le due direttive, è bene analizzare alcuni punti della nuova direttiva che potrebbero essere all’origine di dubbi o errate interpretazioni.
MTM Consulting s.r.l. è in grado di seguire i Fabbricanti, gli importatori e i distributori nel processo di certificazione necessario, ai sensi della Direttiva Atex 2014/34/UE, al fine di poter immettere i prodotti sul mercato.
La Direttiva Atex 2014/34/UE definisce i criteri di progettazione e realizzazione dei prodotti destinati ad essere utilizzati all’interno di un’atmosfera potenzialmente esplosiva e sarà applicabile a partire dal 20 Aprile 2016 in sostituzione della attuale Direttiva 94/9/CE.
Quindi, a partire dalla data indicata, gli apparecchi e sistemi di protezione immessi sul mercato e installati in ambienti classificati come potenzialmente esplosivi (ai sensi della Direttiva 1999/92/CE), dovranno essere marcati CE rispetto alla Direttiva Atex 2014/34/UE.
Dal punto di vista tecnico, la suddivisione degli apparecchi in gruppi e in categorie è del tutto analoga a quella presente nella attuale Direttiva 94/9/CE. Stesso discorso vale per le diverse procedure di certificazioni previste e per i requisiti essenziali di sicurezza. Pertanto, a livello puramente tecnico, non vi sono sostanziali aggiornamenti con la nuova Direttiva 2014/34/UE. Tuttavia, è bene analizzare e chiarire alcuni punti della nuova direttiva che potrebbero essere all’origine di dubbi o errate interpretazioni.
- Il fabbricante è la persona fisica o giuridica che fabbrica un prodotto o fa realizzare il prodotto e successivamente lo commercializza (quindi, lo mette a disposizione per la prima volta sul mercato) apponendovi il proprio nome o il proprio marchio oppure lo utilizza per fini propri. In definitiva, la definizione di fabbricante è allineata alla definizione di fabbricante già presente nelle direttive di prodotto di ultima emissione (per esempio, la direttiva macchine 2006/42/CE): non è fabbricante solo colui che realizza un prodotto per venderlo, ma anche colui che lo realizza per usarlo internamente in azienda all’interno di un’atmosfera potenzialmente esplosiva oppure colui che utilizza in atmosfera potenzialmente esplosiva un prodotto originariamente non destinato a tale luogo di installazione, definendo, di fatto, una nuova destinazione d’uso e quindi una nuova messa a disposizione sul mercato del prodotto, con necessità di arrivare ad una marcatura CE-Atex.
- I fabbricanti devono apporre sui prodotti che hanno immesso sul mercato un numero di tipo, di lotto, di serie o altri elementi che ne consentano l’identificazione, o, se le dimensioni o la natura del prodotto non lo permettono, devono apporre le informazioni qui riportate sull’imballaggio o su un documento di accompagnamento del prodotto. In definitiva non è strettamente necessario riportare su ogni singolo elemento della serie di prodotti realizzata un numero seriale identificativo del singolo prodotto. Anche in funzione della tipologia di prodotto, il fabbricante può scegliere di identificare un’intera famiglia di prodotti (per esempio con un numero di lotto) tenendo però in considerazione che, qualora l’Autorità di vigilanza del mercato, applicando la procedura di salvaguardia, decida che un certo prodotto deve essere ritirato dal mercato (in quanto pericoloso), se questi non è identificato da un seriale specifico, potrebbe decidere che debba essere ritirato l’intero lotto a cui il prodotto appartiene.
- I fabbricanti devono indicare sul prodotto il nome, la denominazione commerciale registrata o il marchio registrato e l’indirizzo postale al quale possono essere contattati; se ciò è impossibile, devono apporre tale informazione sull’imballaggio o su un documento di accompagnamento del prodotto. In taluni casi (per prodotti piccoli), tali indicazioni possono essere posizionate anche all’interno del prodotto stesso, tuttavia devono sempre essere facilmente individuabili dall’Autorità di sorveglianza del mercato senza danneggiare il prodotto e senza la necessità di smontarlo. Lo stesso obbligo ricade anche sulla figura di importatore (se presente): in questo caso, sul prodotto è necessario che sia presente sia il nome, denominazione commerciale o marchio del fabbricante che il nome, denominazione commerciale o marchio dell’importatore (entrambi con i rispettivi indirizzi postali di contatto). Nel caso particolare in cui fabbricante e importatore siano la stessa multinazionale (produce fuori dall’UE e vende in UE) è possibile indicare il solo importatore qualora quest’ultimo sia disponibile ad assumersi pienamente le responsabilità che ricadono sul fabbricante.
- I fabbricanti devono garantire che il prodotto sia accompagnato da istruzioni e informazioni sulla sicurezza in una lingua facilmente comprensibile agli utenti finali, come stabilito dallo Stato membro interessato. Considerando che sono oggetto della Direttiva 2014/34/UE anche i componenti destinati ad essere inseriti negli apparecchi e sistemi di protezione, tale obbligo ricade anche su di essi. Questi componenti sono spesso molto piccoli e sono forniti in lotti di dimensioni anche molto diverse, pertanto, per soddisfare questa richiesta della direttiva può essere una soluzione fornire la documentazione in allegato ai documenti di consegna.
- I fabbricanti, a seguito di una richiesta motivata di un’autorità nazionale competente, devono fornire a quest’ultima tutte le informazioni e la documentazione, in formato cartaceo o elettronico, necessarie per dimostrare la conformità del prodotto alla direttiva 2014/34/UE, in una lingua che può essere facilmente compresa da tale autorità. In definitiva, l’autorità nazionale competente di un qualunque stato della UE può contattare direttamente il fabbricante (o, nel caso, l’importatore) senza necessariamente passare dalla corrispondente autorità locale dello stato in cui risiede il fabbricante (o importatore). L’autorità locale potrebbe essere contattata, in seconda battuta, dall’autorità nazionale che ha fatto richiesta qualora il fabbricante non risponda alle richieste inviategli.
[A cura di: ing. Christian Trinastich per mtm consulting s.r.l.]
-
News
Prevenzione delle patologie muscolo-scheletriche: la Linea Guida di Regione Lombardia
10/12/2015
Nel settembre 2015 è stata pubblicata la Linea Guida di Regione Lombardia per la prevenzione delle patologie muscolo scheletriche connesse con movimenti e sforzi ripetuti degli arti superiori, aggiornamento della precedente versione del 2009.
La linea Guida si pone l’obbiettivo di indicare una metodologia generale e valida per approcciare in azienda alla valutazione generale dei rischi che possono portare all’insorgenza di patologie muscolo-scheletriche. Sebbene infatti i metodi di valutazione diretti, NIOSH e OCRA su tutti, siano ben definiti anche da norme ISO, resta difficile per un azienda, che ha molte e differenti lavorazioni e un elevato numero di addetti, gestire l’approccio generale a tale rischio. Quali mansioni analizzare dettagliatamente con un metodo normato? Quali mansioni escludere in primo luogo e con quale giustificazione? Come effettuare uno screening iniziale generale accettato dagli enti ispettivi, che evidenzi le criticità da approfondire? Come valutare a priori l’ergonomia di una nuova postazione di lavoro o di una nuova lavorazione e come migliorarla? Come valutare attività molto impegnative ma saltuarie o ripetute con cadenza non giornaliera?
MTM Consulting può supportare la tua azienda nel gestire tale aspetto della valutazione dei rischi di sovraccarico biomeccanico ed impostare uno strumento attivo che permette di analizzare in continuo i rischi presenti nelle varie postazioni di lavoro.
Il D.Lgs. 81/2008 prevede, all’art. 15, che il datore di lavoro adotti una serie di misure generali di tutela dei lavoratori che comprendono anche “il rispetto dei principi ergonomici nella concezione dei posti di lavoro, nella scelta delle attrezzature e nella definizione dei metodi di lavoro e produzione, anche per attenuare il lavoro monotono e ripetitivo”. Nello specifico Titolo poi il D.Lgs. 81/2008 rimanda alle tre norme ISO della serie 11228 pubblicata nel 2003. Queste tre norme incorporano tre metodologie già universalmente riconosciute ed applicate per la valutazione dei rischi da sovraccarico biomeccanico:
- il metodo NIOSH, per la valutazione della movimentazione di carichi pesanti (maggiori di 3 kg);
- il metodo Snook e Ciriello, per la valutazione del tiro-spinta di un carrello/transpallet;
- il metodo dell’indice OCRA, per la valutazione della movimentazione di carichi leggeri ad alta frequenza, ovvero dei cosiddetti movimenti ripetitivi.
Nelle norme poco o nulla si dice però su come approcciare in azienda in modo globale a questa problematica, ovvero come creare, nell’ottica di valutare per tutte le attività e mansioni tutti i rischi, una mappa, giustificata e basata su evidenze, delle lavorazioni presenti attribuendo ad ognuna di esse un punteggio sintetico di rischio, dal quale desumo se sono assolutamente lontano da una reale problematica legata a patologie muscolo-scheletriche o se invece devo appunto applicare un metodo maggiormente dettagliato per indagare tale rischio e nel caso migliorare la lavorazione o la postazione. Questo è sicuramente un obiettivo al quale tendere per rispettare le richieste del D.Lgs. 81/2008 e per gestire in modo realistico una problematica la cui incidenza sta aumentando anno per anno, con un grande incremento delle malattie professionali ad essa correlate.
La nuova linea guida di Regione Lombardia riporta a tal proposito spunti mutuati dalla recente norma ISO TR 12295, che è appunto l’interpretazione applicativa delle succitate tre norme, ed in particolare della norma in merito al metodo OCRA, che è la metodologia maggiormente complessa ma che riguarda la quasi totalità delle lavorazioni in azienda.
La linea guida quindi descrive i tre passaggi che devono portare ad ottenere una mappatura completa:
1.Identificazione dei compiti ripetitivi secondo criteri univoci.
Si tratta di capire se una lavorazione rientra all’interno di parametri di ripetitività; la Linea Guida stabilisce quindi della chiavi di ingresso, finalizzate a verificare l’esistenza di un pericolo lavorativo (nella fattispecie da sovraccarico biomeccanico) e l’eventuale necessità di una ulteriore analisi e valutazione rapida.
2.Valutazione rapida del rischio.
In questo successivo passaggio si valuta in modo semplificato la presenza di un rischio legato a tale ripetitività; consiste in una verifica rapida della presenza di potenziali condizioni di rischio, attraverso semplici domande di tipo quali/quantitativo. Questo passaggio è sostanzialmente indirizzato a identificare, in modo semplificato, tre possibili condizioni o esiti:
- accettabile, non sono richieste ulteriori azioni;
- critica, è urgente procedere ad una riprogettazione della postazione di lavoro o del processo;
- necessità di una analisi più dettagliata, è necessario procedere ad una stima o valutazione analitica attraverso strumenti più dettagliati di analisi.
3.Stima analitica del rischio.
Si procede tramite la metodologia OCRA all’analisi delle mansioni che al punto precedente si presentano come intermedie.
[A cura di: ing. Riccardo Bozzo per mtm consulting s.r.l.]
-
News
La valutazione dei rischio di esposizione a Radiazioni Ottiche Artificiali
09/12/2015
Le Radiazioni Ottiche Artificiali sono sempre più presenti all’interno delle nostre aziende, moltiplicandosi appunto l’impiego di sorgenti laser e LED per l’effettuazione delle più disparate lavorazioni, dalle lavorazioni meccaniche, alle attività di metrologia e misurazione, alle attività di conteggio e rilevazione prodotti, alla banale illuminazione puntuale.
Una corretta valutazione dei rischio di esposizione a Radiazioni Ottiche Artificiali diventa quindi fondamentale per ovviare a problematiche come lesioni oculari o cutanee e anche abbagliamenti momentanei che possono creare non solo fastidi ma anche veri e propri incidenti.
MTM Consulting può supportare la tua azienda nella valutazione dell’esposizione a queste specifiche sorgenti di emissione.
Con radiazioni ottiche si intendono tutte le radiazioni elettromagnetiche nella gamma di lunghezza d'onda compresa tra 100 nm e 1 mm. Lo spettro delle radiazioni ottiche si suddivide in radiazioni ultraviolette, radiazioni visibili e radiazioni infrarosse.
All’interno di questo spettro di radiazioni si collocano anche le radiazioni laser, ovvero radiazione ottica prodotta da un laser (qualsiasi dispositivo al quale si possa far produrre o amplificare le radiazioni elettromagnetiche nella gamma di lunghezze d'onda delle radiazioni ottiche) e le radiazioni incoerenti, ovvero radiazioni emesse da sorgenti UV e LED.
In generale i rischi che la legislazione intende prevenire sono quelli per la salute e la sicurezza che possono derivare dall’esposizione alle radiazioni ottiche artificiali o dal loro impiego durante il lavoro, con particolare riguardo ai rischi dovuti agli effetti nocivi sugli occhi e sulla cute. La tipologia di effetti dell’esposizione dipende dalla lunghezza d’onda della radiazione incidente, mentre dall’intensità dipendono sia la possibilità che questi effetti si verifichino che la loro gravità. L’interazione della radiazione ottica con l’occhio e la cute può provocare conseguenze dannose come ad esempio: foto cheratite, foto congiuntivite, eritema della pelle, cataratta fotochimica, lesione termica della retina, bruciatura della cornea, etc. Oltre ai rischi per la salute dovuti all’esposizione diretta alle radiazioni ottiche artificiali esistono ulteriori rischi indiretti, quali:
- disturbi temporanei visivi, quali abbagliamento, accecamento temporaneo;
- rischi di incendio e di esplosione innescati dalle sorgenti stesse e/o dal fascio di radiazione;
- ulteriori rischi associati alle apparecchiature/lavorazioni che utilizzano ROA quali stress termico, contatti con superfici calde, rischi di natura elettrica, etc.
La valutazione dei rischi deve essere effettuata ai sensi dallo specifico articolo 223 del D.Lgs. 9 aprile 2008, n. 81 e nello specifico parte dal censimento dettagliato delle sorgenti impiegata in azienda. Tale censimento deve riguardare anche:
- per le apparecchiature/dispositivi che emettono radiazioni ottiche incoerenti è necessario conoscere la “categoria” di classificazione della fonte di emissione secondo lo standard UNI EN 12198:2009;
- per le apparecchiature/dispositivi che emettono radiazioni laser è necessario conoscere la “classe” di classificazione della fonte di emissione secondo lo standard IEC 60825-1;
- per le apparecchiature dotate di LED è necessario conoscere la relativa classificazione secondo la norma CEI EN 62471:2009, in alternativa alle precedenti classificazioni indicate;
- Irradianza (E) o densità di potenza;
- Esposizione radiante (H);
- Radianza (L).
Questo primo censimento ha lo scopo inoltre di verificare per quali di queste apparecchiature/dispositivi non sia necessario eseguire una valutazione dei Rischi più dettagliata, secondo quanto indicato dalla apposita guida ISPESL in merito alla gestione degli agenti fisici, ovvero:
- apparecchiature/dispositivi che emettono radiazioni ottiche incoerenti classificate in “categoria 0” secondo lo standard UNI EN 12198:2009;
- apparecchiature/dispositivi che emettono radiazioni laser classificate in “classe 1” o in “classe 2” secondo lo standard IEC 60825-1;
- apparecchiature/dispositivi dotati di LED classificati come “Esente” secondo la norma CEI EN 62471:2009;
- illuminazione standard per uso domestico e di ufficio, monitor dei computer, display, fotocopiatrici;
- lampade e cartelli di segnalazione luminosa.
Nel caso non risulti disponibile la classificazione della sorgente luminosa da parte del relativo fabbricante secondo uno dei succitati standard, è possibile fare eseguire tale classificazione da un laboratorio accreditato a tal fine.
Nel caso le nostre apparecchiature non rientrino in questo succitato elenco di esclusione è necessario verificare il rispetto dei limiti di esposizione riportati nell'Allegato XXXVII del D.Lgs. 81/2008, tramite la metodologia ivi indicata, che si basa in generale su dati propri delle fonti radianti e sul tipo di esposizione durante l’attività lavorativa:
- Irradianza (E) o densità di potenza;
- Esposizione radiante (H);
- Radianza (L);
- Tempo di esposizione;
- Angolo di esposizione.
In alternativa, o nel caso i dati proprie delle sorgenti non siano disponibili, risulta necessario effettuare delle misure strumentali in sito.
[A cura di: ing. Riccardo Bozzo per mtm consulting s.r.l.]
-
News
Scelta dei Dispostivi di Protezione Individuale (DPI) per la protezione delle vie respiratorie
04/12/2015
Il datore di lavoro è tenuto a mettere a disposizione dei lavoratori specifici Dispositivi di Protezione Individuale quando i rischi non possano essere ridotti mediante misure tecniche di prevenzione, tramite mezzi di protezione collettiva oppure con misure, metodi o procedimenti di riorganizzazione del lavoro (secondo quanto riportato all’art. 77 del D.Lgs. 81/2008 e s.m.i.). La corretta scelta dei DPI, e nello specifico quelli necessari a proteggere le vie respiratorie, è, dunque, strettamente correlata al rischio da cui proteggere l’operatore.
MTM Consulting s.r.l. è in grado di aiutare i datori di lavoro nella scelta dei DPI idonei a proteggere il lavoratore nell’esecuzione delle proprie mansioni lavorative, anche al fine di conformarsi alle richieste del D.Lgs. 81/2008 e s.m.i.
L’obbligo primario del datore di lavoro (art. 17 del D.Lgs. 81/2008 e s.m.i.) è quello di valutare tutti i possibili rischi presenti in azienda e a cui sono esposti i lavoratori redigendo il documento di valutazione dei rischi (art. 28). Lo scopo della valutazione dei rischi è quello di individuare tutti i rischi esistenti in azienda e di fornire le misure di prevenzione e di protezione necessarie a ridurre i rischi individuati. La necessità di ricorrere a specifici DPI (art. 75 del D.Lgs. 81/2008 e s.m.i.) emerge dunque laddove i rischi legati all’esecuzione di una specifica attività non possano essere ridotti adeguatamente tramite misure tecniche di prevenzione, tramite misure di protezione collettiva o per mezzo di misure, metodi e procedimenti di riorganizzazione del lavoro.
Lo stesso art. 18 del D.Lgs. 81/2008 e s.m.i. indica l’obbligo, per il datore di lavoro, di fornire ai lavoratori i necessari e idonei dispositivi di protezione individuale: la scelta dei DPI deve dunque essere, attenta e pertinente rispetto al rischio o ai rischi da cui è necessario proteggere l’operatore.
A fronte di ciò, gli obblighi del datore di lavoro in merito alla scelta dei DPI da fornire ai propri lavoratori, sono riassumibili nei seguenti punti:
- La scelta deve essere correlata al risultato della valutazione dei rischi: i DPI sono da utilizzarsi laddove i rischi non possano essere evitati con altri mezzi.
- La scelta deve essere funzione della tipologia di rischio e delle caratteristiche del dispositivo stesso, riscontrabili presso il fabbricante di quest’ultimo.
- La scelta deve essere aggiornata ogni qualvolta intervenga una variazione significativa negli elementi della valutazione effettuata in precedenza.
I dispositivi di protezione individuale delle vie respiratorie sono DPI di terza categoria che, come indicato dal D.Lgs. 475/1992, comprende i DPI destinati a salvaguardare da rischi di morte o di lesioni gravi e di carattere permanente. Al fine di garantire un uso corretto di questi DPI sono obbligatorie l’informazione, la formazione e l’addestramento dei lavoratori.
Al fine di effettuare una scelta corretta per garantire protezione alle vie respiratorie, devono essere analizzati e valutati i seguenti fattori:
- tipo di sostanza: corretta scelta del tipo di filtro; necessità/opportunità di proteggere altre parti del volto (occhi - viso);
- concentrazioni: capacità del filtro in relazione al tempo di esposizione previsto;
- libertà movimento: in funzione delle attività previste, il DPI deve garantire facilità di movimento all’operatore;
- anatomia del viso: adeguatezza maschera in funzione dell’operatore;
- condizioni ambientali: necessario valutare l’adeguatezza del DPI in funzione delle condizioni ambientali in cui l’operatore è tenuto ad indossarlo (per esempio, ambiente di lavoro molto caldo oppure molto umido).
In linea generale, i DPI di protezione delle vie respiratorie si distinguono in:
- Respiratori isolanti: sono dispositivi di protezione che consentono di respirare indipendentemente dall’atmosfera circostante. Il DPI impedisce il contatto con l’atmosfera esterna e fornisce ossigeno o aria da una sorgente autonoma non inquinata. In particolare devono essere utilizzati quando: la percentuale di ossigeno è inferiore al 17%; la concentrazione dei contaminanti è superiore ai limiti di utilizzo dei respiratori a filtro; non si conosce la natura e/o la concentrazione dei contaminanti; in presenza di gas/vapori con scarse proprietà di avvertimento.
- Respiratori a filtro: sono dispositivi di protezione delle vie respiratorie nei quali l’aria inspirata passa attraverso un materiale filtrante (filtri) in grado di trattenere gli agenti inquinanti. I filtri si classificano in base al tipo, alla classe e al livello di protezione”. In particolare, questi respiratori possono essere: non assistiti (l’aria passa all’interno del facciale solo mediante l’azione dei polmoni), a ventilazione assistita (l’aria passa all’interno del facciale costituito da una maschera mediante un elettroventilatore normalmente trasportato dallo stesso utilizzatore) oppure a ventilazione forzata (l’aria passa all’interno del facciale costituito da un cappuccio o da un elmetto mediante un elettroventilatore normalmente trasportato dallo stesso utilizzatore).
- Respiratori a barriera d’aria con filtro: sono dispositivi che consentono di eseguire un lavaggio delle prime vie aeree mediante una visiera, ancorata alla parte superiore del capo, che copre tutto il volto, ed un flusso di aria laminare che viene fatto scorrere sul lato interno della stessa visiera, a pressione, dall’alto verso il basso. Non si ha quindi isolamento dall’ambiente circostante, ma una diluizione dell’inquinante presente a livello del naso e della bocca dell’utilizzatore. L’aria compressa viene filtrata e successivamente regolata in base alle esigenze operative: la compressione avviene mediante collegamento di questo dispositivo ad un impianto di compressione locale, mentre vengono utilizzate cartucce in carbone attivo, alloggiate nella cintura dell’operatore, per la decontaminazione dell’aria.
[A cura di: ing. Christian Trinastich per mtm consulting s.r.l.]
-
News
Analisi del Rischio Esplosione per le operazioni che impiegano polveri combustibili o elettrostatiche
04/12/2015
Diversamente da quanto si può pensare i dati storici evidenziano una costante presenza di incidenti in attività produttive causati dall’esplosione di polveri combustibili o elettrostatiche. Le analisi degli incidenti dimostrano inoltre che in alcuni casi tali incidenti sono avvenuti nonostante tutte le misure di sicurezza previste (installazione di apparecchiature in accordo alla classificazione ATEX, efficaci impianti per la continuità elettrica e messa a terra delle apparecchiature, impiego di adeguati dispositivi di protezione individuale, ecc.) fossero state messe in atto e costantemente mantenute attive nel tempo.
MTM Consulting può supportare la tua azienda nell’effettuare un’analisi dei rischi dedicata e nello sviluppare la procedura aziendale maggiormente adeguata a mantenere sotto controllo questo rischio complesso e a volte difficilmente percepito.
Molte polveri presenti nelle attività industriali sono combustibili o elettrostatiche e possono creare perciò un’atmosfera potenzialmente esplosiva, in particolare nei settori che manipolano:
- prodotti agroalimentari, dove troviamo farine e polvere di zucchero, ma anche le polveri residue della lavorazione e trasporto di cereali;
- prodotti farmaceutici, con vari preparati ad uso farmaceutico e cosmetico;
- materie plastiche, come ad esempio le polveri plastiche o quelle generate dal trasporto e uso di pellet in plastica o altri materiali friabili;
- carbone e legno;
- carta triturata;
- metalli, come ad esempio la polvere di alluminio.
- Tali polveri se sospese in aria costituiscono un potenziale pericolo di esplosione se si verificano tutte e cinque le condizioni che portano ad un’esplosione:
- presenza di comburente, ovvero l’ossigeno;
- presenza di combustibile, ovvero la polvere;
- presenza di un innesco, ovvero una scintilla elettrica o meccanica, una fiamma, una superficie in tensione o in elevata temperatura, etc.;
- presenza di un confinamento;
- presenza della giusta miscela tra comburente e combustibile, che varia per ogni tipologia di polveri.
La valutazione dei rischi di esplosione delle polveri sul luogo di lavoro deve essere effettuata secondo quanto previsto dal D.Lgs. 81/2008. Da questa analisi vengono implementate adeguate misure di prevenzione e protezione per ridurre al minimo tali rischi di esplosione, quali:
- classificazione delle aree pericolose, ovvero delle Zone potenzialmente esplosive;
- dotazione nelle varie Zone classificate di apparecchiature ATEX;
- gestione della continuità elettrica;
- portelle di scarico pressione;
- necessità di procedure di lavoro adeguate, etc.
In caso di presenza di polveri è poi comunque presente un rischio residuo legato alla possibilità di andare incontro ad anomalie gravi nelle attrezzature di lavoro o fallimento degli impianti di sicurezza. È quindi necessario considerare nell’analisi dei rischi di processo l’entità di tali rischi residui, allo scopo di stimare le frequenze di accadimento e le conseguenze degli scenari di esplosione dovuti a perdite di contenimento o ad anomalie di processo verificando l’adeguatezza delle misure di prevenzione e protezione, ma soprattutto delle procedure di lavoro e di emergenza.
Particolare attenzione infatti, in particolare durante la fase di stesura e verifica delle procedure, deve essere data alle attività di manutenzione e alle fasi di modifica e avviamento di nuovi macchinari o parti di impianto, situazioni nelle quali facilmente è possibile che alcune parti dei sistemi di sicurezza possano risultare non completamente funzionanti o controllate.
[A cura di: ing. Riccardo Bozzo per mtm consulting s.r.l.]
-
News
Nuova definizione di “operatore” secondo il D.Lgs. 81/2008
25/11/2015
Il Decreto Legislativo 14 Settembre 2015, n. 151 ha modificato in alcuni punti il Testo unico in materia di tutela della salute e della sicurezza nei luoghi di lavoro. In particolare, la principale modifica riguarda la definizione di “operatore” presente all’interno del Titolo III relativo all’uso delle attrezzature di lavoro in azienda. La nuova definizione prevede anche la figura del datore di lavoro.
MTM Consulting s.r.l. è in grado di seguire le aziende e, dunque, affiancare i datori di lavoro nel soddisfacimento degli obblighi previsti dal D.Lgs. n.81/2008 e s.m.i. anche relativamente all’uso delle attrezzature di lavoro e agli obblighi che ne derivano.
IL Decreto Legislativo 14 settembre 2015, n. 151 recante “Disposizioni di razionalizzazione e semplificazione delle procedure e degli adempimenti a carico di cittadini e imprese e altre disposizioni in materia di rapporto di lavoro e pari opportunità, in attuazione della legge 10 dicembre 2014, n. 183” ha modificato in alcuni punti il D.Lgs. 81/2008 - Testo Unico in materia di tutela della salute e della sicurezza nei luoghi di lavoro.
Una delle modifiche apportate è relativa alla definizione di “operatore”contenuta nel Titolo III (Uso delle attrezzature di lavoro e dei dispositivi di protezione individuale), Capo I (Uso delle attrezzature di lavoro) del D.Lgs. 81/2008. Infatti, l’articolo 20 - Modificazioni al decreto legislativo 9 aprile 2008, n. 81 - del D.Lgs. 151/2015 riporta: “l) all'articolo 69, comma 1, lettera e), dopo le parole: «il lavoratore incaricato dell'uso di una attrezzatura di lavoro» sono inserite le seguenti: «o il datore di lavoro che ne fa uso»”.
In definitiva, il nuovo articolo 69 del D.Lgs. 81/2008, in merito alla definizione di operatore è il seguente:
“e) operatore: il lavoratore incaricato dell’uso di una attrezzatura di lavoro o il datore di lavoro che ne fa uso”.
Questa modifica si è resa necessaria per andare incontro a quei casi in cui sia lo stesso datore di lavoro a divenire operatore e dunque a utilizzare direttamente le attrezzature di lavoro nella propria azienda. Quali sono quindi le conseguenze di questa modifica?
La più importante conseguenza è quella relativa alla formazione dell’operatore come richiesta dall’art. 73 del decreto. Nel momento in cui il datore di lavoro diviene operatore e utilizza una attrezzatura deve necessitare formazione, informazione e addestramento adeguati in funzione delle attività previste su quella stessa attrezzatura di lavoro in rapporto alle condizioni di impiego e alle situazioni anormali prevedibili. Parimenti nasce la necessità, anche per il datore di lavoro, di ricevere adeguata formazione in relazione all’uso di attrezzature soggette a specifica abilitazione, con riferimento a quanto richiesto dall’articolo 73 comma 5 del Testo Unico e quanto indicato nell’Accordo del 22 febbraio 2012. A riguardo si ricorda che tale Accordo concerne l’individuazione delle attrezzature di lavoro per le quali è richiesta una specifica abilitazione degli operatori (e, dunque, ora anche dei datori di lavoro che dovessero fare uso di attrezzature di lavoro), nonché le modalità per il riconoscimento di tale abilitazione, i soggetti formatori, la durata, gli indirizzi ed i requisiti minimi di validità della formazione, in attuazione dell’articolo 73, comma 5, del D.Lgs. 81/2008 e s.m.i.
Risulta quindi evidente che laddove un datore di lavoro utilizzi un carrello elevatore semovente, una PLE o qualunque altra attrezzatura di sollevamento rientrante nell’elenco dell’Accordo, necessiti di specifica abilitazione. Alcune delle attrezzature che richiedono specifica abilitazione sono, per esempio:
- PLE (Piattaforme di Lavoro Elevabili)
- Gru per autocarro
- Gru a torre
- Carrelli semoventi con conducente a bordo
- Gru mobili
- Trattori agricoli o forestali
- Escavatori
[A cura di: ing. Christian Trinastich per mtm consulting s.r.l.]
-
News
Obbligo del datore di lavoro: valutazione dei rischi sulle macchine in uso
02/10/2015
In accordo a quanto riportato nell’art. 28 del D.Lgs. 81/2008 e s.m.i. il datore di Lavoro deve considerare e analizzare tutti i rischi a cui possono essere esposti i propri lavoratori durante le loro attività effettuando una valutazione dei rischi. Tra questi ultimi, nelle realtà produttive, rivestono particolare importanza i rischi correlati all’uso delle attrezzature di lavoro. Da questo si evince come sia necessaria anche una specifica valutazione dei rischi sulle attrezzature di lavoro utilizzate in azienda.
MTM Consulting s.r.l. è in grado di affiancare i datori di lavoro nel soddisfacimento degli obblighi presenti nel D.Lgs. n.81/2008 e s.m.i. anche per quanto riguarda la sicurezza delle attrezzature di lavoro e la necessità, per i datori di lavoro, di effettuare su di esse una specifica valutazione dei rischi.
L’art. 70 del D.Lgs. 81/2008 e s.m.i. riporta i requisiti di sicurezza per quanto concerne le attrezzature di lavoro utilizzate in azienda. In particolare (comma 1) richiede che le attrezzature di lavoro messe a disposizione dei lavoratori siano rispondenti alle specifiche disposizioni legislative e regolamentari di recepimento delle Direttive comunitarie di prodotto: le attrezzature devono essere marcate CE ed essere realmente conformi ai requisiti di sicurezza delle direttive applicabili. In aggiunta (comma 2), per le attrezzature di lavoro per le quali non esistono direttive di prodotto specifiche, non esistono disposizioni legislative di recepimento o che sono state messe in servizio prima della data di entrata in vigore della direttiva di riferimento (in Italia, per la Direttiva Macchine, è il 21 settembre 1996), il datore di lavoro deve garantire che tali attrezzature siano conformi ai requisiti minimi di sicurezza di cui all’Allegato V del D.Lgs. 81/2008 e s.m.i
In accordo a quanto richiesto dal successivo art. 71 del D.Lgs. 81/2008 e s.m.i., il datore di lavoro è tenuto, dunque, a verificare l’effettiva conformità delle attrezzature utilizzate in azienda alla legislazione vigente e, solo in un secondo momento, metterle a disposizione dei lavoratori.
Per quanto riguarda gli obblighi più generali richiesti dal D.Lgs. 81/2008 e s.m.i., l’art. 28 richiede che il datore di lavoro effettui una valutazione dei rischi aziendali che copra tutti i possibili rischi a cui sono esposti i lavoratori. Quindi, nella valutazione dei rischi, devono essere analizzati anche i rischi correlati all’uso delle macchine. Pertanto, sebbene non sia espressamente richiesta una valutazione dei rischi sulle attrezzature di lavoro, considerando quanto richiesto dall’art. 28 e gli obblighi del datore di lavoro in merito alle attrezzature di lavoro messe a disposizione dei lavoratori (art. 71 come sopra ricordato), risulta necessaria una valutazione dei rischi sulle stesse attrezzature.
La valutazione dei rischi ha due scopi:
- dimostrare la conformità delle attrezzature di lavoro alla legislazione di riferimento e
- mettere in sicurezza le attrezzature di lavoro non conformi.
La valutazione dei rischi deve partire dall’analisi degli interventi previsti dal personale operativo sulla macchina, durante tutte le fasi di utilizzo previste (utilizzo in senso stretto ma anche manutenzione, pulizia, regolazione, ecc.). Di fatto, nella valutazione dei rischi il datore di lavoro analizza le diverse attività lavorative previste nella propria azienda che prevedono l’utilizzo di attrezzature di lavoro, evidenzia i pericoli presenti e specifica le misure di protezione attuate o da intraprendere al fine di ridurre il rischio correlato alle diverse situazioni pericolose e quindi esporre i lavoratori al solo rischio residuo.
Per capire come effettuare questa valutazione è possibile riferirsi alla normativa tecnica armonizzata alla Direttiva Macchine 2006/42/CE: nello specifico la norma di riferimento è la UNI EN ISO 12100: 2010. Questa norma fornisce i principi generali di valutazione dei rischi e loro successiva riduzione durante il processo di progettazione e realizzazione di una macchina. I principi forniti dalla norma sono assolutamente generali e possono essere facilmente applicati anche dal datore di lavoro che intenda ridurre i rischi legati all’uso delle attrezzature di lavoro nella propria azienda.
Il procedimento è applicabile sia nei confronti di macchine marcate CE sia nei confronti di attrezzature di lavoro “vecchie” e dunque prive di marcatura CE; ciò che cambiano sono i riferimenti tecnici.
Qualora la macchina sia marcata CE, è necessario conoscere i contenuti della Direttiva Macchine 2006/42/CE. Infatti, la valutazione dei rischi deve dimostrare come la macchina sia effettivamente conforme ai requisiti di sicurezza della Direttiva Macchine (in accordo a quanto richiesto dall’art. 70, comma 1) mettendo in risalto, specificatamente, quelle che potrebbero essere non conformità evidenti.
Nel caso di macchine prive di marcatura CE perché messe in servizio prima del 21/09/1996, la valutazione dei rischi deve mirare a soddisfare i requisiti tecnici dell’Allegato V del D.Lgs. 81/2008 e s.m.i. Anche in questo caso è evidentemente necessaria una conoscenza dell’Allegato V ma anche delle norme tecniche UNI e CEI applicabili.
[A cura di: ing. Christian Trinastich per mtm consulting s.r.l.]
-
News
Le novità introdotte dalla nuova versione della norma CEI 11-27 “Lavori su impianti elettrici”
08/09/2015
Già in altri passati comunicati ci siamo soffermati sull’importanza di avere una procedura aziendale in merito alla corretta effettuazione di attività di manutenzione su impianti elettrici a bordo macchina. Tale procedura si deve basare sulle indicazioni delle specifica norma CEI 11-27 “Lavori su impianti elettrici”, che definisce figure e responsabilità e metodo di lavoro. La norma, che costituisce corretta attuazione degli obblighi di legge, è stata modificata nel febbraio 2014 e ne elenchiamo ora le novità.
MTM Consulting può supportare la tua azienda nell’adempimento di tutti gli obblighi di legge in materia, elaborando la soluzione più pratica e completa per garantire alla tua azienda il rispetto delle norme applicabili.
La norma, nella sua quarta versione, si sofferma sulla definizione dei principali attori della gestione dell’impianto elettrico; le maggiori differenze dalla precedente versione si riscontrano sulle seguenti figure:
- Unità (o Persona) responsabile di un impianto elettrico (URI): è il proprietario dell’impianto elettrico, nella maggior parte dei casi identificato nel Datore di Lavoro. A questa figura fanno capo le responsabilità dell’impianto elettrico durante il normale esercizio, quindi in assenza di lavori di qualunque natura. Rappresenta inoltre il soggetto che evidenzia la necessità di manutenzione dell’impianto e in generale la necessità di effettuare di lavori sull’impianto.
- Persona designata alla conduzione dell’impianto elettrico (Responsabile Impianto, RI): è la persona responsabile della sicurezza dell’impianto elettrico durante un’attività lavorativa. Questa figura viene designata dalla URI in occasione di attività da svolgere sull’impianto stesso, compresa la manutenzione. Il RI ha la responsabilità dello svolgimento in sicurezza del lavoro, tramite la redazione del piano di lavoro e la diretta verifica dell’apposizione di eventuali terre nei punti di sezionamento e dei cartelli monitori.
Vediamo ora brevemente la definizione di lavoro elettrico e di lavoro non elettrico, utile per discriminare in azienda quali attività devono essere svolte da personale appositamente formato, addestrato e abilitato (PES, PAV, PEI).
- Lavoro elettrico: lavoro svolto a distanza minore o uguale a DV da parti attive accessibili di linee e di impianti elettrici o lavori fuori tensione sugli stessi. All’interno della zona prossima, tutti i lavori che si eseguono, qualunque sia la loro natura, sono assoggettati ai medesimi rischi elettrici. Ciò significa che, se non si è Persone esperte (PES) o avvertite (PAV) in ambito elettrico, si deve lavorare sotto la supervisione di una PES (sezionamenti e messa in sicurezza, oppure installazione di barriere o protettori isolanti), oppure sotto sorveglianza da parte di PES o PAV che applica la procedura del lavoro in prossimità, ovvero il rispetto della distanza di sicurezza.
- Lavoro non elettrico: lavoro svolto a distanza minore di DA9 e maggiore di DV da parti attive accessibili di linee e di impianti elettrici.
La norma poi effettua l’allineamento delle distanze di lavoro sotto tensione (DL) e delle distanze di prossimità (DV) con la Norma CEI EN 50110-1 per i lavori di costruzione ed altri lavori non elettrici.
[A cura di: ing. Riccardo Bozzo per mtm consulting s.r.l.]
-
News
Come gli studi di Life Cycle Assessment sono percepiti dalle organizzazioni stesse che li conducono
02/09/2015
Gli studi di LCA, sui quali scopi ci siamo già ampiamente dilungati in precedenti comunicati, offrono molteplici benefici all’azienda che li conduce, visti i numerosi utilizzi che possono essere fatti di uno studio.
Proprio a scopo divulgativo l’azienda olandese PRé Consultants, che fornisce uno dei software maggiormente utilizzati nel mondo per l’esecuzione di studi di LCA, ovvero il SimaPro, software impiegato anche da noi di MTM Consulting per supportare in nostri clienti, ha effettuato un sondaggio, pubblicato a maggio 2015, mirato a capire come viene percepito lo studio di LCA da aziende che lo hanno eseguito internamente nel corso dell’anno 2014.
Proponiamo ora brevemente i risultati, abbastanza sorprendenti, di questa indagine che ha visto coinvolte 274 aziende, distribuite in 28 nazioni.
Il primo dato riguarda la composizione dei team che svolgono lo studio di LCA aziendale: questo è mediamente composto da tre persone.
Viene poi riportato che il 57% dei top manager delle aziende che hanno intrapreso studi di LCA è a conoscenza dei benefici e degli scopi dello studio di LCA: tale dato è molto incoraggiante!
Viene poi proposta la classifica dei reparti aziendali che maggiormente promuovono lo svolgimento di uno studio di LCA, che vede solo al quarto posto, notevolmente staccato, il reparto marketing, mentre ai primi posti chi pianifica azioni di Corporate Social Responsibility e ricerca e sviluppo del prodotto:
- 35 % settore ambiente e sostenibilità e chi produce;
- 34 % ricerca e sviluppo;
- 11 % sviluppo del prodotto;
- 7 % marketing;
- 6 % altri reparti;
- 4 % gestione della catena di distribuzione;
- 2 % operations.
È poi stato domandato in quale dei seguenti ambiti si hanno avuti maggiori benefici dall’implementazione di uno studio di LCA:
- 57% avere una base scientifica;
- 55 % processo decisionale informato;
- 52% comunicazione con i propri clienti;
- 36 % miglioramento del marchio;
- 24 % gestione del rischio aziendale;
- 23 % aumento dell’efficienza;
- 20 % abbassamento dei costi;
- 11 % aumento dei ricavi;
- 0 % pochi o nessun beneficio.
Come ultimo dato che presentiamo vengono riportati gli anni di esperienza nel campo degli studi di LCA delle azienda contattate nel sondaggio. Tante sono aziende che già da tempo seguono tale argomento a livello interno, ma si rileva un forte interesse da parte di nuove aziende negli ultimi anni:
- 21 % più di 10 anni;
- 25 % tra i 5 e i 10 anni;
- 41 % da 1 a 4 anni;
- 13 % meno di un anno.
[A cura di: ing. Riccardo Bozzo per mtm consulting s.r.l.]
-
News
Responsabilità di progettisti, fabbricanti, fornitori e installatori
28/08/2015
Progettare, realizzare e installare un macchinario industriale secondo i requisiti della Direttiva Macchine 2006/42/CE permette di assolvere obblighi ed evitare quindi sanzioni, non solo correlati al recepimento italiano della Direttiva stessa, ovvero il D.Lgs 17/2010, ma anche al Testo Unico della Salute e Sicurezza sul Lavoro. Spesso infatti, in merito all’introduzione di un nuovo macchinario industriale in azienda, si conosce bene l’aspetto legato alla valutazione dei rischi che il Datore di Lavoro deve effettuare prima di fornire tale attrezzatura ai propri addetti, ovvero si vede il Testo Unico come una serie di obblighi che riguardano chi mette a disposizione o utilizza attrezzature di lavoro. Gli articoli 23, 23 e 24 del D.Lgs. 81/2008 però introducono obblighi puntuali su progettisti, fabbricanti, fornitori e installatori di tali attrezzature di lavoro, ai quali sono collegate sanzioni anche più pesanti di quanto accede nel D.Lgs 17/2010.
MTM Consulting lavora da anni nel campo della Marcatura CE e parte della nostra attività si sviluppa seguendo proprio i fabbricanti di macchinari industriali nel corso di tutto l’iter di CE, dalla progettazione, alla realizzazione alla installazione presso il cliente, tenendo ben in considerazione anche le richieste del Testo Unico.
La violazione dei succitati articoli è un evento spesso sottovalutato da chi realizza un macchinario industriale. Sebbene il numero di sanzioni correlate a tali articoli è abbastanza limitato, è utile considerare le modalità in cui un ente ispettivo arriva a commisurare tali sanzioni. La violazione di tali articoli infatti viene riscontrata dagli enti o in caso di denuncia di una mancanza da parte del Datore di Lavoro o, caso molto più probabile, in caso di infortunio grave; entrambe le situazioni sono quindi circostanze in cui il Datore di Lavoro che utilizza nella sua azienda il macchinario ha forti ragioni per dimostrare le mancanze presunte del fabbricante!
Lo scopo del Testo Unico nei tre succitati articoli è quello di impedire la commercializzazione o costruzione di attrezzature di lavoro aventi pericolosità tale da vanificare l’efficacia del sistema di prevenzione aziendale.
All’Articolo 22, viene richiesto a progettisti dei luoghi e dei posti di lavoro e degli impianti di rispettare i principi generali di prevenzione in materia di salute e sicurezza, elencati in modo generico all’articolo Articolo 15 “Misure generali di tutela” e nei Titoli specifici; inoltre viene richiesto di scegliere attrezzature, componenti e dispositivi di protezione rispondenti alle disposizioni legislative e regolamentari in materia.
Gli obblighi dei fabbricanti e dei fornitori dell’Articolo 23 riportano che è vietata la fabbricazione, la vendita, il noleggio e la concessione in uso di attrezzature di lavoro, dispositivi di protezione individuali ed impianti non rispondenti alle disposizioni legislative e regolamentari vigenti in materia di salute e sicurezza sul lavoro; qui è quindi presente il rimando maggiormente diretto alla Direttiva Macchine, per quanto concerne appunto un macchinario industriale. In caso di locazione finanziaria di beni assoggettati a procedure di attestazione alla conformità inoltre, gli stessi beni debbono essere accompagnati, a cura del concedente, dalla relativa documentazione, ovvero nel caso di un macchinario industriale della Dichiarazione di Conformità e dal Manuale di Uso e Manutenzione.
Gli obblighi degli installatori dell’Articolo 25 richiedono poi agli stessi, seguendo il filo logico impostato dal Decreto, di attenersi alle norme di salute e sicurezza sul lavoro, nonché alle istruzioni fornite dai rispettivi fabbricanti.
Le sanzioni come già detto sono, prese singolarmente, tra le più pesanti presenti nell’intero Testo Unico, in particolare proprio per i fabbricanti:
- i progettisti che violano il disposto dell’Articolo 22 sono puniti con l’arresto fino a un mese o con l’ammenda da 600 a 2.000 euro;
- i fabbricanti e i fornitori che violano il disposto dell’Articolo 23 sono puniti con l’arresto da quattro a otto mesi o con l’ammenda da 15.000 a 45.000 euro;
- gli installatori che violano il disposto dell’Articolo 24 sono puniti con l’arresto fino a tre mesi o con l’ammenda da 1.000 a 3.000 euro.
[A cura di: ing. Riccardo Bozzo per mtm consulting s.r.l.]
News
Direttiva Atex 94/9/CE: certificazione degli assiemi
28/08/2015
La Direttiva Atex 94/9/CE, si applica agli apparecchi destinati ad essere utilizzati in atmosfera potenzialmente esplosiva. Nella definizione di “apparecchi” sono inclusi anche più apparecchi tra loro combinati, intesi come assiemi. Secondo quanto previsto dalla Direttiva, laddove l’assieme debba essere utilizzato in atmosfera potenzialmente esplosiva deve sempre essere marcato CE ai sensi Atex.
MTM Consulting s.r.l. è in grado di affiancare i fabbricante di prodotti destinati ad essere installati in atmosfera potenzialmente esplosiva nel soddisfacimento degli obblighi richiesti dalla Direttiva Atex 94/9/CE, sia per quanto riguarda gli apparecchi che per quanto concerne gli assiemi.
La Direttiva Atex 94/9/CE, così come la futura Direttiva 2014/34/UE che sostituirà quella attuale a partire dal 20 Aprile 2016, si applica agli apparecchi e ai sistemi di protezione destinati ad essere utilizzati in atmosfera potenzialmente esplosiva. In particolare, i prodotti Atex sono certificati secondo specifiche categorie di protezione in funzione della classificazione dell’ambiente di installazione in cui andranno ad operare. Compito dell’utilizzatore è quello di acquistare sul mercato attrezzature che siano certificate CE Atex secondo una categoria di protezione conforme alla zonizzazione effettuata, rispetto al rischio esplosione, nel proprio luogo di lavoro.
Secondo la Direttiva Atex, per “apparecchi” si intendono “le macchine, i materiali, i dispositivi fissi e mobili, gli organi di comando, la strumentazione e i sistemi di rilevazione e di prevenzione che, da soli o combinati, sono destinati alla produzione, al trasporto, al deposito, alla misurazione, alla regolazione e alla conversione di energia e al trattamento di materiale e che, per via delle potenziali sorgenti di innesco che sono loro proprie, rischiano di provocare un’esplosione”.
Dall’espressione “combinati” di cui alla definizione di apparecchi sopra vista, ne consegue che un assieme, costituito dalla combinazione di due o più parti di apparecchi, deve essere considerato un prodotto e rientrare quindi nel campo di applicazione della Direttiva 94/9/CE.
Il concetto è simile ma non uguale a quello di insieme (inteso come sistema integrato di produzione) previsto dalla Direttiva Macchine 2006/42/CE. Infatti, per quest’ultima l’insieme deve necessariamente garantire una applicazione ben definita in quanto rientra nella definizione di macchina. Per la direttiva Atex 94/9/CE invece, l’assieme non necessariamente deve garantire una applicazione ben definita ma deve tuttavia presentarsi sotto forma di singola unità funzionale. In definitiva, potrebbe essere considerato un assieme per la Direttiva Atex 94/9/CE anche ciò che per la Direttiva Macchine è una quasi-macchina o addirittura non è nulla di definito.
Per quanto abbiamo detto, gli assiemi potrebbero non essere immediatamente pronti all’uso ma necessitare un’attenta installazione (secondo la logica, per esempio, delle quasi-macchine per la Direttiva Macchine). Pertanto, le istruzioni dovranno contemplare questa evenienza in modo che l’installatore, adottando le indicazioni in esse contenute, possa procedere alla installazione dell’assieme senza ulteriori valutazioni di conformità da parte sua, in quanto completate dal processo di certificazione portato avanti e concluso dal Fabbricante.
Qualora le singole parti costituenti l’assieme siano già conformi alla Direttiva Atex 94/9/CE e idoneamente marcate CE dai corrispondenti Fabbricanti, il compito del Fabbricante dell’assieme è quello di effettuare una valutazione dei rischi che evidenzi i pericoli di innesco aggiuntivi conseguenti all’unione delle singole parti a costituire l’assieme finale. Il risultato di questa valutazione dei rischi, al solito, deve garantire la conformità dell’assieme agli applicabili requisiti di sicurezza della Direttiva e dunque garantire la sicurezza dell’intero assieme rispetto al pericolo di esplosione. In questo caso, quindi, il Fabbricante presume la conformità della singole parti e si concentra solo sui pericoli di innesco eventualmente scaturiti dalla loro combinazione a costituire l’assieme. Il Fabbricante dunque dovrà realizzare un fascicolo tecnico e un manuale di istruzioni, apporre una targa di identificazione CE e Ex sull’insieme e firmare una dichiarazione CE di conformità a dimostrazione che l’assieme, come unità funzionale, rispetta i requisiti della direttiva Atex.
Nel caso in cui, invece, alcune (o tutte) parti costituenti l’assieme siano prive di idonea marcatura CE Atex (perché, per esempio, sono realizzate internamente oppure la marcatura è relativa ad una categoria di protezione non idonea all’ambiente di installazione previsto), il Fabbricante non potrà presumere la conformità di tali parti e dunque dovrà estendere la valutazione dei rischi dell’assieme anche a queste singole parti. In questo caso, dunque, sarà compito del Fabbricante redigere la valutazione dei rischi con l’intento di dimostrare che non solo l’assieme ma anche gli apparecchi privi di idonea marcatura CE Atex sono conformi ai requisiti applicabili della Direttiva Atex. In questo caso dichiarazione CE di conformità e targa di identificazione CE e Ex devono sempre essere unici e relativi alla certificazione dell’assieme.
[A cura di: ing. Christian Trinastich per mtm consulting s.r.l.]
News
La valutazione dei rischi secondo la Direttiva Atex 94/9/CE
28/08/2015
Il processo di certificazione che porta alla marcatura CE Atex di un prodotto secondo la Direttiva 94/9/CE cambia a secondo del gruppo e della categoria di protezione del prodotto. Tuttavia la necessità, da parte del fabbricante, di dimostrare la conformità del prodotto ai requisiti della direttiva comporta sempre la stesura di una specifica valutazione dei rischi come parte principale del fascicolo tecnico.
MTM Consulting s.r.l. è in grado di affiancare i fabbricanti nel soddisfacimento degli obblighi richiesti dalla Direttiva Atex 94/9/CE, sia per quanto concerne la procedura di certificazione da adottare, sia per quanto riguarda la documentazione da preparare (in particolare, il fascicolo tecnico, le istruzioni per l’uso e la dichiarazione CE di conformità).
Nell’ambito del processo di progettazione e realizzazione, la protezione contro le esplosioni degli apparecchi e dei sistemi di protezione oggetto della Direttiva Atex 94/9/CE è ottenuta attraverso la conformità degli stessi prodotti ai requisiti essenziali di sicurezza delle Direttiva. In aggiunta, il Fabbricante è tenuto a fornire all’utilizzatore le istruzioni per l’uso grazie alle quali sia possibile utilizzare correttamente il prodotto, vale a dire secondo l’uso previsto rispetto al quale è stato progettato e realizzato.
Per dimostrare la conformità del prodotto ai requisiti della Direttiva Atex 94/9/CE è necessario effettuare una specifica valutazione dei rischi. Questa valutazione dovrà concentrarsi prevalentemente sulla possibilità di evitare sorgenti di innesco sul prodotto e, all’occorrenza, sulla possibilità di contenere o controllare eventuali fenomeni esplosivi.
A dimostrazione di quanto appena indicato si può fare riferimento alla Direttiva 94/9/CE, allegato II, punto 1.0.1, secondo cui i fabbricanti sono tenuti a progettare gli apparecchi e i sistemi di protezione secondo i principi della “sicurezza integrata contro le esplosioni”. La sicurezza integrata contro le esplosioni ha lo scopo di impedire la formazione di atmosfere esplosive, nonché di sorgenti di innesco, e qualora, malgrado tutto, si produca un’esplosione, a soffocarla immediatamente e/o circoscriverne gli effetti. Tuttavia è da sottolineare come, in molti casi, il Fabbricante non è in grado di valutare esattamente la portata di eventi esplosivi definendo chiaramente le conseguenze negative di un’esplosione; infatti, queste ultime dipendono strettamente dal luogo di installazione in cui l’apparecchio è destinato ad operare e dalla presenza, o meno, di ulteriori sorgenti di innesco presenti che potrebbero amplificare le conseguenze di un fenomeno esplosivo. Per tale motivo, la valutazione dei rischi deve concentrarsi sulla valutazione del rischio di innesco o sulla funzione di controllo delle esplosioni grazie a dispositivi di protezione e di sicurezza presenti sull’apparecchio.
Alla luce di quanto esposto, la valutazione dei rischi, intesa come valutazione del rischio di innesco, deve coprire sia gli aspetti legati alla progettazione e realizzazione dell’apparecchio (per esempio, scelta di materiali isolanti o conduttori, tipologia di metalli, tipi di azionamento, ecc.) ma coprire anche gli aspetti legati all’ambiente di utilizzo del prodotto interfacciandosi direttamente con l’utilizzatore (per esempio, temperatura di accensione delle polveri o gas presenti nel luogo di utilizzo, limiti di esplosività dei gas, ecc.)
A livello procedurale, la valutazione dei rischi consiste in una serie di tappe logiche che consentono di esaminare in modo sistematico i pericoli associati agli apparecchi utilizzati in atmosfera potenzialmente esplosiva. Essa è seguita, ogni qualvolta risulti necessario, dalla riduzione del rischio secondo le modalità indicate dalla norma generale UNI EN ISO 12100: 2010 e dalla norma specifica per componenti non elettrici UNI EN 15198: 2008; quando questo processo viene ripetuto costituisce il processo iterativo per eliminare per quanto possibile i pericoli e per mettere in atto le misure di sicurezza.
La valutazione dei rischi si svolge essenzialmente in due passaggi successivi:
- l’analisi dei rischi, comprendente:
- la determinazione dei limiti della apparecchiatura,
- l’identificazione dei pericoli,
- la stima dei rischi;
- • la valutazione del rischio vera e propria.
Pertanto, durante la valutazione dei rischi vengono individuati gli interventi e le soluzioni adottabili per l'eliminazione o riduzione dei rischi (valutazione del rischio vera e propria) al fine di poter ottenere il livello di protezione richiesto, funzione della lavorazione prevista dalla apparecchiatura e dell’ambiente nel quale l’apparecchiatura deve essere installata.
[A cura di: ing. Christian Trinastich per mtm consulting s.r.l.]
News
La gestione integrata degli infortuni
27/08/2015
La gestione degli infortuni che occorrono in azienda riveste un aspetto molto importante poiché incorpora in sé numerosi obblighi, ma anche numerose opportunità di miglioramento.
Gestire in modo integrato i vari aspetti che sono compresi nella rilevazione e analisi degli infortuni, siano essi anche molto lievi, diventa quindi fondamentale per dare e dimostrare continua applicazione dei principi di tutela dei lavoratori.
MTM può aiutare la tua azienda ad impostare quindi una corretta e puntuale procedura di gestione ed analisi dell’infortunio, allo scopo di assolvere gran parte di obblighi e valutazioni legate alla negativa occorrenza di un infortunio, correlata alla formazione generale di tutti gli addetti.
All’accadimento di un infortunio il massimo sforzo deve essere dedicato all’assistenza immediata dell’addetto infortunato, per alleviare la sofferenza legata ad un evento che in un mondo lavorativo perfetto non dovrebbe mai accadere.
In secondo luogo la gestione e la successiva analisi dell’evento sono lo strumento migliore in mano all’azienda per evitare che infortuni analoghi non si ripetano; anche su questa fase è quindi necessario convogliare numerose energie per completare un processo spesso difficoltoso ma che può portare grandi risultati.
La prima fase gestionale post infortunio porta il datore di lavoro a implementare, con il medico competente, tutti gli obblighi legislativi e burocratici, come la denuncia di infortunio e l’avvio delle pratiche assicurative. Ma in contemporanea il datore di lavoro deve essere in grado di assicurare che subito venga attivato un processo di analisi dell’infortunio e delle sue cause, definendo in una procedura tempi e responsabilità di questa fase di indagine interna. Questo passaggio è molto importante sia per attuare azioni di miglioramento sia per rispondere ad eventuali quesiti delle parti interessate e organismi competenti.
Questa prima fase di indagine dovrebbe essere compiuta, tramite documenti precompilati e guidati, direttamente dagli operatori maggiormente vicini, a livello di attività e di ruolo, all’infortunato. La giusta figura per condurla è quindi un preposto di area, che deve coinvolgere e più lavoratori possibili, meglio se testimoni dell’accaduto, gli addetti al primo soccorso intervenuti e se è fattibile l’infortunato stesso.
Dopo questa prima fase di indagine deve essere avviata una fase maggiormente dettagliata e di più ampio respiro, in collaborazione con medico competente e RSPP. In questa fase è necessario valutare la correlazione di tale evento con altri avvenuti in passato o con mancati infortuni, in modo da stabilirne le cause reali e programmare interventi di miglioramento mirati, tramite la definizione di tempi e responsabilità.
Altro aspetto fondamentale per gestire al meglio gli infortuni è poi la formazione e l’informazione in merito allo svolgimento dell’indagine. Infatti spesso risulta difficile ottenere informazioni adeguate dai colleghi di lavoro dell’infortunato, proprio perché non conoscono a cosa queste informazioni possono essere utili. Formare le persone sulle procedure interne che le riguardano anche parzialmente e fornire informazioni in merito al completamento delle azioni correttive a seguito di un infortunio contribuisce a creare un clima di fiducia reciproca e collaborazione tra le varie figure aziendali.
Ultimo punto ma molto importante è la definizione di che cosa l’azienda considera essere un infortunio. Spesso infatti le aziende considerano come infortunio, e avviano quindi tali modalità di indagine, solamente quegli eventi che vengono denunciati all’INAIL. L’obbligo di denuncia si ha unicamente per infortuni con prognosi medica che dichiara l’infortunato guaribile in tre o più giorni oltre a quello dell’infortunio. In questo modo però nel calcolo degli infortuni ma anche nella loro analisi si perdono tutti quegli eventi minori, magari che vengono direttamente medicati presso l’infermeria aziendale, con la perdita di nemmeno un giorno di lavoro. L’analisi di tali eventi è invece addirittura più importante, poiché permette di evitare l’accadimento di un fatto più grave: le statistiche dell’INAIL mostrano chiaramente come gli infortuni più gravi sono nella maggior parte dei casi preceduti da un numero limitato di infortuni lievi, lievissimi o addirittura di mancati infortuni.
[A cura di: ing. Riccardo Bozzo per mtm consulting s.r.l.]
-
News
Noleggio o comodato d’uso di attrezzature assoggettate a verifiche periodiche
03/07/2015
L’obbligatorietà delle verifiche periodiche è prevista dall’art. 71, comma 11 del D.Lgs. n.81/2008 e s.m.i. per quelle attrezzature di lavoro riportate nell’elenco dell’Allegato VII dello stesso decreto. Questi rientra tra gli obblighi del datore di lavoro. Ma nel momento in cui una attrezzatura è fornita a noleggio o in comodato d’uso, chi è il soggetto che deve richiedere la verifica?
MTM Consulting s.r.l. è in grado di affiancare i datori di lavoro nel soddisfacimento degli obblighi riportati dal D.Lgs. n.81/2008 e s.m.i. anche per quanto riguarda le attrezzature di lavoro, sia quelle di proprietà utilizzate in azienda, sia quelle fornite o ricevute a noleggio o in comodato d’uso.
Tra gli obblighi che vertono sul datore di lavoro, relativamente alle attrezzature di lavoro messe a disposizione dei propri lavoratori in azienda, vi è anche quello di garantire che siano effettivamente sicure e rimangano tali nel tempo. L’art. 71, comma 4, in particolare, richiede, tra le altre cose, che le attrezzature siano sottoposte ad una documentata manutenzione periodica che possa garantire nel tempo il soddisfacimento dei requisiti di sicurezza, siano essi quelli rispondenti alle direttive europee di riferimento per macchine marcate CE, oppure quelli rispondenti alla legislazione nazionale previgente (allegato V, D.Lgs. n.81/2008 e s.m.i.) per le macchine prive di marcatura CE.
Sempre l’art. 71, al comma 8, richiede che gli interventi di controllo su specifiche attrezzature (sia quelli successivi all’installazione, che quelli periodici di controllo e verifica) siano volti ad assicurare il buono stato di conservazione e l’efficienza ai fini della sicurezza delle stesse attrezzature e che questi controlli siano effettuati da persona competente.
Il comma 11 riporta che le attrezzature che richiedono un regime di verifiche e controlli ben definito sono quelle elencate nell’Allegato VII del D.Lgs. n.81/2008 e s.m.i. Queste attrezzature devono essere sottoposte ad un controllo iniziale (che ne possa certificare la corretta installazione e messa in servizio) e, successivamente, siano sottoposte a verifiche di tipo periodico (che possano garantire il soddisfacimento dei requisiti di sicurezza nel tempo).
Questi interventi devono essere richiesti dal datore di lavoro presso cui sono in servizio le attrezzature. Nello specifico, la prima verifica deve essere richiesta all’INAIL che vi deve provvedere entro 45 giorni. Una volta decorso il termine di 45 giorni il datore di lavoro può avvalersi, a propria scelta, di altri soggetti pubblici o privati abilitati. Le verifiche successive sono effettuate su libera scelta del datore di lavoro dalle ASL o, ove sia previsto con legge regionale, dall’ARPA o da soggetti pubblici o privati abilitati. I verbali redatti all’esito delle verifiche devono essere conservati e tenuti a disposizione dell’organo di vigilanza.
Ma in caso di noleggio o comodato d’uso di attrezzature ricadenti in Allegato VII, chi deve richiedere tali verifiche? Se definito nel contratto di noleggio o concessione in uso, la richiesta di queste verifiche può essere effettuata anche dallo stesso noleggiatore o concedente in uso.
Nel caso in cui il concedente in uso sia inadempiente (di fatto, non fa richiesta delle verifiche), che tipo di responsabilità vertono sul datore di lavoro presso il cui ambiente di lavoro sono utilizzate le attrezzature? A riguardo è bene sottolineare che l’obbligo riportato dall’art. 71, comma 11 del D.Lgs. n.81/2008 e s.m.i. ricade sul datore di lavoro; pertanto, qualora il noleggiatore o concedente in uso non provvede a far eseguire le verifiche periodiche, si ritiene che il datore di lavoro, in quanto titolare di una posizione di garanzia primaria, sia passibile della sanzione amministrativa pecuniaria da 548 a 1972.80 euro oltre che, in caso di infortunio, di quelle penali (secondo art. 589 e 590 del c.p.). Successivamente, in sede civile, il datore di lavoro potrà agire nei confronti del noleggiatore per il risarcimento dei danni subiti.
In definitiva quali sono le responsabilità del noleggiatore? A riguardo si può fare riferimento ad una decisione della Cassazione Penale (n.12293 del 15 marzo 2013). Secondo la Cassazione, in questo caso, trovano applicazione gli art. 23 e 57 del D.Lgs. n.81/2008 e s.m.i. Nello specifico, l’art. 23 individua gli obblighi di fabbricanti e fornitori e specifica che sono vietate la fabbricazione, la vendita e la concessione in uso di attrezzature di lavoro non rispondenti alle disposizioni legislative e regolamentari vigenti in materia di salute e sicurezza sul lavoro precisando, al secondo comma, che in caso di locazione finanziaria di attrezzature assoggettate a procedure di attestazione della conformità, esse siano accompagnate, da parte del concedente, dalla relativa documentazione. In definitiva, chi concede in uso attrezzature di lavoro a noleggio deve fornire la documentazione completa e aggiornata (quindi anche gli esiti delle verifiche precedentemente richieste per le attrezzature in Allegato VII).
Una volta stipulato il contratto di noleggio e consegnata la macchina, il responsabile del corretto utilizzo e delle verifiche periodiche diviene, per quanto esposto sopra, il datore di lavoro.
[A cura di: ing. Christian Trinastich per mtm consulting s.r.l.]
-
News
Classificazione attrezzature a pressione secondo la Direttiva 2014/68/UE (PED)
01/07/2015
Dal 1 giugno 2015 è entrato in vigore nell’intero mercato unico europeo e, pertanto, anche in Italia, l’articolo 13 (classificazione delle attrezzature a pressione) della nuova Direttiva PED 2014/68/UE che sostituisce l’articolo 9, di pari oggetto, della precedente, ma ancora vigente, direttiva 97/23/CE. Qui di seguito analizziamo le novità introdotte.
MTM Consulting s.r.l. è in grado di affiancare i fabbricanti nell’individuare i riferimenti legislativi applicabili ai propri prodotti, seguendoli in tutto il processo di certificazione che porta alla marcatura CE del prodotto prima della sua immissione sul mercato unico europeo.
Sulla Gazzetta Ufficiale della Unione Europea del 27/06/2014 è stata pubblicata la nuova Direttiva inerente la messa a disposizione sul mercato delle attrezzature a pressione, Direttiva 2014/68/UE (PED).
Il campo di applicazione della Direttiva 2014/68/UE non è mutato rispetto alla precedente Direttiva 97/23/CE. Esso è stato aggiornato, meglio organizzato e reso più chiaro, ma nei contenuti è rimasto inalterato. Un importante aggiornamento è relativo, invece, alla classificazione delle attrezzature a pressione.
Le attrezzature a pressione che rientrano nel campo di applicazione della Direttiva PED 2014/68/UE sono organizzate in categorie, in base all’Allegato II, secondo criteri di pericolosità crescente. La classificazione è funzione anche del tipo di fluido presente all’interno dell’attrezzatura secondo quanto riportato all’art. 13 della Direttiva 2014/68/UE. La classificazione dei fluidi riportata dal citato articolo fa riferimento a quanto indicato nel Regolamento (CE) n. 1272/2008 che classifica non solo i fluidi, ma anche le loro miscele e che identifica una serie di classi di pericolo sia fisico che per la salute:
- fluidi gruppo 1: esplosivi instabili, gas infiammabili, gas comburenti, liquidi infiammabili, solidi infiammabili, sostanze o miscele auto-reattive, liquidi e solidi piroforici, sostanze e miscele che a contatto con l’acqua, liberano gas infiammabili, liquidi e solidi comburenti, perossidi organici, sostanze tossiche per contatto, via aerea, per inalazione, ecc. Nel gruppo 1 rientrano anche le sostanze e miscele contenute nelle attrezzature a pressione la cui temperatura massima ammissibile TS è superiore al punto di infiammabilità del fluido.
- fluidi gruppo 2: tutte le sostanze e miscele che non rientrano nel gruppo 1.
Sempre il citato art. 13 riporta che, allorché un recipiente è costituito da vari scomparti, è classificato nella categoria più elevata di ciascuno dei singoli scomparti. Allorché uno scomparto contiene più fluidi, è classificato in base al fluido che comporta la categoria più elevata.
Come detto, la classificazione dei fluidi si basa sul nuovo Regolamento (CE) n. 1272/2008 (regolamento CLP - Classification, Labelling and Packaging) entrato in vigore il 1° giugno 2015 e che sostituisce la Direttiva 65/548/CEE sulla base della quale fino alla stessa data era disciplinata la suddivisione dei fluidi pericolosi necessaria per la corretta classificazione delle attrezzature a pressione. Per tale motivo, si è resa necessaria l’entrata in vigore dell’art. 13 proprio in tale data, di fatto in anticipo rispetto alla data di entrata in vigore delle restanti previsioni della Direttiva 2014/68/UE, fissata al 19 luglio 2016.
Infatti, la Direttiva 2014/68/UE obbligava gli stati membri a recepire nel proprio ordinamento legislativo nazionale i contenuti dell’art. 13 entro il 28 febbraio 2015, rendendo applicabili le disposizioni di tale articolo proprio a partire dal 1° giugno 2015. In Italia è stata emanata una Circolare del Ministero dello Sviluppo Economico che analizza questo aspetto, rendendo applicabile dal 1° giugno 2015 l’art. 13 della Direttiva 2014/68/UE sebbene manchi un recepimento nazionale della Direttiva che sarà pubblicato solo entro la fine del 2015.
Le classi di pericolo di cui al Regolamento n. 1272/2008 possono comportare, in certi casi, la classificazione nel gruppo 1 di alcune sostanze precedentemente classificate nel gruppo 2 (a seguito, ad esempio, della diversa classificazione dei pericoli per la salute di cui al Regolamento stesso). Per questo motivo, in alcune situazioni, si potrebbe presentare una diversa categorizzazione dell’attrezzatura a pressione con conseguente diverso modulo di valutazione della conformità da applicare per arrivare alla certificazione del prodotto. Il risultato è che per i prodotti che utilizzano fluidi di cui alla lettera a) del paragrafo 1 dell’art. 13 della Direttiva 2014/68/UE (quindi, di gruppo 1), è necessario prestare attenzione alla nuova classificazione introdotta al fine di individuare, mediante una specifica valutazione dei rischi, una eventuale diversa categorizzazione del prodotto che potrebbe comportare l’applicazione di un diverso modulo di valutazione della conformità.
In questa fase transitoria, sebbene sia applicabile la classificazione ora vista e definita dalla Direttiva 2014/68/UE, restano applicabili tutti gli altri aspetti (e, dunque, anche i moduli di valutazione della conformità) definiti dalla Direttiva 97/23/CE ancora vigente e dal recepimento italiano, il D.Lgs. n. 93/2000.
Non sono, invece, oggetto di variazioni le procedure relative dei prodotti di cui alla lettera b) del paragrafo 1 del citato articolo 13 della direttiva, cioè le procedure per le attrezzature che contengono fluidi di gruppo 2. Analogamente non è modificato il criterio di classificazione di cui al paragrafo 2 dello stesso articolo 13, secondo cui è classificato nella categoria più elevata un recipiente a pressione costituito da vari scomparti riferibili a categorie diverse o in cui uno scomparto contenga più fluidi.
[A cura di: ing. Christian Trinastich per mtm consulting s.r.l.]
News
Il rischio chimico e cancerogeno dell’attività di saldatura
15/06/2015
La saldatura di metalli è un’attività lavorativa che si ritrova in numerose aziende italiane, sia all’interno di reparti manutenzione, ove viene eseguita saltuariamente per effettuare delle riparazioni, sia in aziende che svolgono tale attività in modo quotidiano, come parte del proprio processo.
Questo tipo di attività risulta sicuramente tra le più critiche per quello che concerne la salute dei lavoratori addetti.
Il rischio correlato all’attività di saldatura deriva prevalentemente dallo sviluppo dei fumi, originati da una miscela di componenti chimici inorganici ed organici, che si libera durante la fase di riscaldamento di materiale oltre al punto di fusione.
In funzione del tipo di saldatura e del tipo di materiali coinvolti vi sono differenti metodologie di valutazione dei rischi da mettere in pratica, tra cui misurazioni strumentali in sito degli inquinanti aerodispersi e redazione di un Registro degli Esposti, in caso si liberino sostanze classificate come cancerogene.
La problematica è però bene descritta dal Testo Unico e da linee guida nazionali e regionali: MTM Consulting può seguire la tua azienda nel definire quale tipologia di rischio è presente in azienda e quale sia la soluzione corretta e sufficiente nel tutelare i tuoi lavoratori e rispettare la normativa vigente.
Il problema legato alla valutazione dei rischi correlati ai fumi di saldatura è rivestito principalmente dalla poca conoscenza che si ha del processo chimico in atto durante lo svolgimento della saldatura.
Se infatti in merito a composti chimici manipolati noi possiamo documentarci tramite la scheda di sicurezza del fabbricante, ciò non è possibile con l’attività di saldatura, dove il materiale saldato è solitamente inerte o privo di rischi correlati all’esposizione quando manipolato a temperatura ambiente.
Durante invece il suo surriscaldamento e portandolo a temperature oltre la sua temperatura di fusione si rilasciano fumi sicuramente pericolosi.
In sostanza durante una qualsiasi attività di saldatura si rilasciano in atmosfera sicuramente: polveri sottili, ozono e metalli pesanti, la cui specificità dipende dal tipo di materiale saldato.
Tali sostanze liberate presentano tutte, come riportato sul Testo Unico all’Allegato XLIII, i seguenti valori correlati all’esposizione umana:
- TLV-TWA, che rappresenta la concentrazione media ponderata nel tempo, per una giornata lavorativa di 8 ore e per 40 ore lavorative settimanali, a cui quasi tutti i lavoratori possono essere esposti ripetutamente, giorno dopo giorno, senza effetti negativi;
- TLV-STEL, che rappresenta la concentrazione a cui lavoratori possono essere esposti continuativamente per un breve periodo senza che insorgano irritazioni , alterazioni croniche o irreversibili del tessuto, narcosi di grado sufficiente ad accrescere la probabilità di infortuni, a compromettere la capacità di mettersi in salvo, l’efficienza lavorativa. Uno STEL viene definito come la esposizione media ponderata su un periodo di 15 minuti che non deve mai essere superata nella giornata lavorativa, anche se la media ponderata su 8 ore rientra nei limiti TLV-TWA.
- TLV-C, che rappresenta la concentrazione che non deve mai essere superata neppure istantaneamente.
Il punto di partenza è quindi quello di effettuare delle analisi in ambiente, in modo da ottenere dei valori di esposizione da confrontare con i sopra citati limiti imposti.
Risulta però fondamentale individuare, oltre alle polveri sottili e all’ozono, l’inquinante da ricercare sotto forma di metallo pesante maggiormente presente, in funzione del tipo di materiale lavorato.
Questa problematica è comune anche con la realizzazione di un Registro degli Esposti, in funzione del fatto che si liberino o meno sostanze (metalli pesanti) classificate come cancerogene.
Ad esempio nelle saldature eseguite su acciaio, in funzione del tipo di acciaio lavorato e della sua composizione possono liberarsi prevalentemente cromo esavalente, cadmio, berillio o cobalto, tutte sostanze classificate come cancerogene.
È bene inoltre ricordare che i principi di prevenzione cui deve attenersi il Datore di Lavoro nel mettere in atto interventi di miglioramento sono, in ordine di fattibilità e se possibile congiuntamente:
- la sostituzione, quando possibile, di una sostanza o preparato con uno a minore tossicità;
- minimizzare la formazione dei fumi che si possono originare durante le lavorazioni;
- utilizzare opportuni sistemi di estrazione (aspirazione) o di diluizione dell’aria (ventilazione forzata);
- utilizzare sempre, in abbinamento ad estrazione/diluizione, impianti di aspirazione localizzata in prossimità del punto di saldatura adeguati a ridurre la dispersione di aerosol nell’ambiente (ideale ‘ciclo chiuso’, ecc.).
Solo come ultima possibilità il Datore di Lavoro deve ricorrere all’uso di DPI come mascherine o autorespiratori. Questa ultima soluzione, spesso preferita dal Datore di Lavoro anche se non giustificata, non elimina inoltre problematiche gestionali, visto la particolarità e pericolosità dei fumi, in merito a utilizzo esclusivo del DPI da parte del lavoratore, gestione e manutenzione di filtri degli stessi DPI, impiego dei corretti filtri per l’inquinante specifico in funzione del tipo di saldatura.
[A cura di: ing. Riccardo Bozzo per mtm consulting s.r.l.]
-
News
La Nuova Norma ISO 14001 : 2015
04/05/2015
Nel corso dell’anno 2015 è prevista la pubblicazione della nuova Norma ISO 14001:2015 da parte dell’Organizzazione Internazionale per la Normazione (ISO).
La versione odierna della Norma che regola la realizzazione, implementazione e mantenimento di un Sistema di Gestione Ambientale è attualmente in vigore dal 2004.
MTM Consulting può seguire la tua azienda nel gestire il piano di transizione alla nuova Norma ISO 14001, incorporando le modifiche nel vostro sistema di gestione anche già attuato e certificato.
La norma ISO 14001 “Sistema di gestione ambientale – Requisiti” è stata la prima norma pubblicata ad applicazione universale per la realizzazione di un sistema di gestione degli aspetti ambientali di un’organizzazione e per la sua certificazione. La prima pubblicazione della norma risale all’anno 1996, norma poi ripubblicata con successiva edizione nell’anno 2004, edizione attualmente in vigore.
Le modifiche previste per la nuova edizione non sembrano al momento incidere pesantemente sui sistemi ad oggi esistenti, introducendo modifiche applicabili tramite interventi di miglioramento degli strumenti già ad adesso presenti in un classico sistema di gestione ambientale. In generale si tratta di interventi che portano a meglio pianificare le attività di un sistema di gestione ambientale, calibrandone l’importanza relativa. Vediamo brevemente i punti al momento trapelati.
Il primo riguarda il ciclo di Deming e la sua rappresentazione. Le classiche fasi dell’iterazione che porta il sistema al miglioramento continuo delle performance ambientali dell’organizzazione, ovvero pianificazione, esecuzione, monitoraggio e attuazione, vengono correlate tutte alla leadership. Questo a sottolineare che identificazione di ruoli e responsabilità di ogni singola parte, azione, pianificazione o monitoraggio sono fondamentali per far si che queste vengano svolte come pensato nel sistema di gestione: ognuno ha degli obiettivi legati al funzionamento del sistema, proprio allo scopo di farlo funzionare in modo efficiente e costante.
Questa tipologia di sistemi di gestione già prevede obbligatoriamente un’analisi dei rischi, ovvero la cosiddetta analisi ambientale, ovvero uno strumento dinamico che, tramite i feedback di indicatori e monitoraggi, fotografa lo stato degli aspetti ambientali rilevanti dell’organizzazione e permette la pianificazione e misurazione di obiettivi e programmi di miglioramento. Quello che si chiede ora riguarda la creazione di uno strumento analogo per la gestione delle parti interessate e delle comunicazioni nei loro confronti o ricevute da loro. Oltre ad identificare le varie parti interessate, siano esse interne od esterne, si vuole creare una scaletta di priorità e un’analisi dettagliata di che cosa si attende tale parte interessata di conoscere in merito agli aspetti ambientali dell’organizzazione e in che dettaglio, evidenziando in particolare i rischi legati a comunicazioni errate, lacunose o tardive. È ben diverso infatti il livello, il linguaggio e la tipologia di dati da comunicare ad un Ente Regionale, piuttosto che agli azionisti del gruppo, pur essendo entrambe due tipi di comunicazioni molto importanti.
Altra innovazione riguarda la forte enfasi data al concetto di ciclo di vita e quindi alla considerazione degli impatti ambientali a lungo termine e correlati alle attività svolte a monte e a valle della nostra organizzazione. Quindi ciò richiede di modificare la nostra analisi degli aspetti ambientali andando a comprendere anche indicazioni circa l’estrazione delle materie prime, aspetti legati all’uso del prodotto / servizio offerto dall’organizzazione e alla sua fase di fine vita e smaltimento, aspetti legati a come i nostri clienti sfruttano il nostro prodotto/servizio; inserire quindi aspetti ambientali non controllati direttamente ma che possono essere influenzati da alcune caratteristiche del nostro prodotto/servizio.
Al momento non sono stati definiti periodi transitori. Quanto al momento viene richiesto alle organizzazioni è di creare un piano di transizione, dove si identificano punti, passaggi, tempistiche e responsabilità per arrivare ad allinearsi completamente con la nuova edizione della norma.
[A cura di: ing. Riccardo Bozzo per mtm consulting s.r.l.]
-
News
Dispositivi di Protezione Individuale per le mani
04/05/2015
Per quanto riguarda la scelta e l’utilizzo dei Dispositivi di Protezione Individuale (DPI), il datore di lavoro è tenuto a rispettare gli obblighi riportati all’art. 77 del D.Lgs. 81/2008 e s.m.i. Evidentemente, la scelta dei DPI è correlata alla natura del rischio da cui il lavoratore deve essere protetto. Nell’industria, tra tutti i DPI utilizzati, meritano un rilievo particolare quelli dediti alla protezione delle mani e delle braccia.
MTM Consulting s.r.l. è in grado di aiutare i datori di lavoro nella scelta dei DPI idonei a proteggere il lavoratore nell’esecuzione delle proprie mansioni lavorative, anche al fine di conformarsi alle richieste del Titolo III del D.Lgs. 81/2008 e s.m.i.
Sappiamo che l’obbligo principale del datore di lavoro (art. 17 del D.Lgs. 81/2008 e s.m.i.) è quello di valutare tutti i possibili rischi presenti in azienda redigendo il documento di valutazione dei rischi (art. 28). Fine della valutazione dei rischi è quello di evidenziare tutti i rischi presenti in azienda e di indicare le conseguenti misure di prevenzione e di protezione necessarie a ridurre i rischi individuati. Tuttavia, laddove il rischio valutato nell’esecuzione di una specifica attività non possa essere ridotto adeguatamente tramite misure tecniche di prevenzione, tramite misure di protezione collettiva o da misure, metodi e procedimenti di riorganizzazione del lavoro, allora è necessario utilizzare specifici DPI (art. 75 del D.Lgs. 81/2008 e s.m.i.).
La scelta dei DPI deve essere effettuata conformemente al rischio da cui il lavoratore deve essere protetto. Il datore di lavoro, infatti, ha l’obbligo (art. 18) di fornire ai lavoratori i necessari e idonei dispositivi di protezione individuale.
Considerando le attività prevalenti presenti nell’industria è indubbio che un ruolo fondamentale è svolta dai dispositivi di protezione individuale delle mani e, dove necessario, delle braccia. Infatti, durante le attività lavorative effettuate nell’industria, mani e braccia sono le parti del corpo maggiormente esposte e soggette a potenziali rischi. Questi possono essere di diversa natura e sono racchiudibili nelle seguenti macro categorie:
- rischi meccanici (tagli, graffi, abrasioni, punture, ecc.)
- rischi termici,
- rischi chimici (contatto con prodotti pericolosi),
- rischi biologici (contatto con microrganismi),
- rischi elettrici.
Chiaramente, per ognuno dei rischi sopra indicati è necessario adottare la tipologia di guanti più adeguata. Questa scelta deve essere il naturale risultato del processo di valutazione dei rischi effettuato in azienda. Infatti, il datore di lavoro, con l’ausilio del responsabile del servizio di prevenzione e protezione, deve scegliere, i DPI più idonei al rischio da cui proteggere l’operatore e al tipo di intervento previsto.
In effetti, la tipologia di guanti intesi come dispositivi di protezione individuale marcati CE ai sensi della Direttiva 89/686/CEE recepita in Italia dal D.Lgs. 475/1992 e s.m.i. è molto ampia e ogni specifica tipologia è utile a proteggere l’operatore da rischi ben definiti.
Vediamo nel dettaglio le principali tipologie:
- Guanti a manopola: sono adatti per lavori pesanti, che richiedono una grossa presa, intesa anche come capacità di manipolare grossolanamente gli oggetti. Possono essere facilmente sfilati in caso di necessità. Tipicamente sono utilizzati contro il rischio termico, nel momento in cui è necessario manipolare, senza la necessità di avere libertà tra le dita, oggetti ad alta temperatura; possono essere utilizzati anche per evitare lesioni meccaniche durante trasporti o movimentazioni di oggetti con superfici ruvide o spigoli vivi. Evidentemente a rischi diversi corrispondono guanti a manopola differenti.
- Guanti a tre dita: sono adatti per lavorazioni che richiedono l’uso delle singole dita, come la saldatura o la molatura.
- Guanti a cinque dita: sono utilizzati quando è richiesta particolare agilità nelle dita della mano. I materiali in cui sono realizzati devono essere scelti in funzione del rischio da cui è necessario proteggersi: possiamo così avere guanti in fibra antitaglio, guanti in lattice, guanti in pelle, ecc. Evidentemente, anche in questo caso, un guanto che protegge da rischi biologici non sarà analogo ad un guanto antitaglio. Inoltre, è da considerare come questa tipologia di guanti, in caso di emergenza, sia sfilabile con una certa difficoltà in quanto devono essere, per ragioni operative, abbastanza aderenti alla pelle della mano.
- Manicotti: si tratta di una manica grossa e corta (arriva fino a poco sopra il gomito), realizzata in materiali differenti (maglia metallica, pelle, polipropilene, ecc.) in funzione del rischio da cui vuole offrire protezione. Sono necessari laddove l’operatore interviene nella zona pericolosa non solo con le mani, ma anche con le braccia.
[A cura di: ing. Christian Trinastich per mtm consulting s.r.l.]
-
News
La Nuova Norma ISO 9001 : 2015 e la gestione del transitorio
01/04/2015
Nel corso dell’anno 2015 è prevista la pubblicazione della nuova Norma ISO 9001:2015 da parte dell’Organizzazione Internazionale per la Normazione (ISO).
La Norma che regola la realizzazione, implementazione e mantenimento di un Sistema di Gestione della Qualità è praticamente immutata dal 2000, anche se l’ultima versione è del 2008, ma ora con la nuova versione 2015 si attendono grandi cambiamenti a vari livelli; la pubblicazione è prevista per il mese di settembre.
MTM Consulting può seguire la tua azienda nel gestire il piano di transizione alla nuova Norma ISO 9001, incorporando le modifiche nel vostro sistema di gestione anche già attuato e certificato.
La norma ISO 9001 “Sistemi di gestione per la qualità – Requisiti” è stata la prima norma pubblicata ad applicazione universale per la realizzazione di un sistema di gestione della qualità di un’organizzazione e per la sua certificazione. La prima pubblicazione della norma risale all’anno 1987, norma poi ripubblicata con successive edizioni nel corso degli anni 1994, 2000 e 2008.
Dal 1987 ad oggi si è modificata la richiesta dei propri clienti circa l’applicazione di tale norma e inoltre i mezzi informatici che aiutano la nostra attività di tutti i giorni, come i software gestionali, adempiono già di per sé ad alcune delle richieste della norma ISO 9001, gestendo così in modo ripercorribile e puntuale aspetti ad esempio correlati a amministrazione, gestione dei fornitori e degli approvvigionamenti, magazzino e relativa fiscalità, gestione dei contatti commerciali, etc. In sostanza quindi ad oggi lavorare in qualità, anche grazie al percorso virtuoso innescato a suo tempo dalla norma ISO 9001, è diventato lo standard per interfacciarsi alla nostra attività lavorativa quotidiana, anche senza essere certificati.
Da qui la necessità di rinnovare lo schema della norma dando strumenti nuovi e maggiormente utili alle aziende che vogliono mantenere o approcciarsi per la prima volta a tale schema.
La novità principale introdotta dalla nuova ISO 9001 riguarda la necessità di una valutazione dei rischi correlati alla gestione della qualità come punto di partenza per l’implementazione del sistema. Analogamente a quanto avviene per le altre norme correlate ai temi ambientali e di sicurezza e salute sul luogo di lavoro, si richiede non solo di individuare i processi aziendali nei quali possiamo scomporre l’azienda, ma di ricercare in questi processi quelli che sono i rischi correlati a falle della gestione della qualità: in questo modo posso fare una valutazione quali-quantitativa ed avere infine un elenco di rischi che posso ordinare per priorità ed agire quindi di conseguenza.
Ecco brevemente le altre novità che traspaiono dal draft della norma, pubblicato nel settembre 2013:
- differente struttura di alto livello, applicabile ora a tutti gli standard di sistema di gestione (9001, 14001, 18001);
- uso dei termini “beni e servizi” al posto del termine “prodotto”;
- introduzione dell’analisi del contesto e delle aspettative delle parti interessate;
- enfasi sull’approccio per processi;
- eliminate le azioni preventive;
- uso del termine “informazione documentata” anziché “documenti” e “registrazioni”;
- maggiori precisazioni sul controllo delle forniture esterne di beni e servizi;
- scompare la figura del Rappresentante della Direzione.
Al momento la pubblicazione della nuova norma è previsto per settembre 2015. L’International Accreditation Forum ha pubblicato il documento informativo "Transition Planning Guidance for ISO 9001 : 2015" per supportare tutte le parti interessate (ovvero organizzazioni, enti di certificazione, auditor, consulenti, etc.) nel processo di passaggio alla nuova edizione.
Al momento IAF e ISO hanno definito un periodo transitorio di 3 anni dalla pubblicazione della nuova edizione di norma, ovvero periodo in cui tutte le certificazioni sulla versione 2008 della norma dovranno essere tarate sulla nuova versione. Quanto al momento viene richiesto alle organizzazioni è di creare un piano di transizione, dove si identificano punti, passaggi, tempistiche e responsabilità per arrivare ad allinearsi completamente con la nuova edizione della norma.
[A cura di: ing. Riccardo Bozzo per mtm consulting s.r.l.]
-
News
Uso scorretto ragionevolmente prevedibile di una macchina
27/03/2015
Secondo quanto richiesto dalla Direttiva Macchine 2006/42/CE, il Fabbricante di una macchina deve garantire che sia effettuata una valutazione dei rischi esistenti considerando l’uso previsto e l’uso scorretto ragionevolmente prevedibile della macchina da parte dell’utilizzatore finale. La valutazione dei rischi deve dimostrare la conformità ai requisiti di sicurezza applicabili riportati in Allegato I. Ma cosa si intende per uso scorretto ragionevolmente prevedibile?
MTM Consulting s.r.l. è in grado di aiutare i Fabbricanti nel processo di certificazione di una macchina e, in particolare, nello stendere la valutazione dei rischi che possa soddisfare le richieste della Direttiva, anche rispetto all’uso scorretto ragionevolmente prevedibile della macchina.
Prima di immettere sul mercato una macchina, il Fabbricante è tenuto ad effettuare l’intero iter di certificazione che porta alla marcatura CE del prodotto. Uno dei passaggi richiesti consiste nella necessità di redigere una valutazione dei rischi che sia parte del Fascicolo Tecnico della macchina. Questo obbligo è richiamato al punto 1 dell’Allegato I – “principi generali” dove si riporta: “Il Fabbricante deve garantire che sia effettuata una valutazione dei rischi per stabilire i requisiti di sicurezza e di tutela della salute che concernono la macchina. La macchina, inoltre, deve essere progettata e costruita tenendo conto dei risultati della valutazione dei rischi”. Lo scopo della valutazione dei rischi è quello di dimostrare la conformità ai requisiti di sicurezza applicabili della Direttiva Macchine. Sempre in Allegato I, è riportato che, con il processo di valutazione dei rischi il Fabbricante, tra le altre cose, è tenuto a stabilire i limiti della macchina, il che comprende stabilire l’uso previsto e l’uso scorretto ragionevolmente prevedibile. Questo concetto è stato ripreso dalla norma UNI EN ISO 12100: 2010 che stabilisce i criteri generali di valutazione dei rischi.
Per uso previsto si intende l’uso della macchina in conformità alle informazioni fornite nelle istruzioni per l’uso; uso previsto è anche quello che deriva dal normale uso del tipo di macchina considerata (un trapano, per esempio, viene utilizzato per forare ed esclusivamente per quello scopo). Analogamente, per macchine complesse, è quello ricavabile da pubblicazioni promozionali, depliant, ecc. In generale, comunque, l’uso previsto non si deve limitare alla fase strettamente di uso, ma deve coprire tutte le fasi di vita della macchina. Resta dunque un obbligo del Fabbricante non solo considerare l’uso previsto nel processo di valutazione dei rischi, ma evidenziarlo chiaramente in tutta la documentazione a supporto della macchina, partendo dalle istruzioni per l’uso.
E’ bene sottolineare un aspetto: la macchina viene progettata e costruita dal Fabbricante per svolgere specifiche funzioni nel rispetto dei limiti (come definiti dalla norma UNI EN ISO 12100: 2010) e dell’uso previsto come indicato nelle istruzioni per l’uso. Solo in queste condizioni è garantita la conformità della macchina ai requisiti essenziali di sicurezza e, dunque, la sua sicurezza (tornando all’esempio del trapano, non è garantita la sicurezza della macchina qualora si faccia un’attività diversa dal forare o si lavorino materiali diversi da quelli previsti e indicati nelle istruzioni).
L’uso scorretto di una macchina è un utilizzo della stessa secondo una modalità non prevista dal progettista della macchina (e dunque, non indicata nelle istruzioni per l’uso). Questa situazione si verifica allorché l’utilizzatore abbia particolari esigenze non contemplate dall’uso previsto e le cui caratteristiche non vengano adeguatamente valutate e comunicate dal costruttore; una tal situazione comporta possibili situazioni di rischio e un comportamento anomalo della macchina.
Nella valutazione dei rischi, il Fabbricante è comunque tenuto a considerare quell’uso scorretto che risulti facilmente prevedibile, vale a dire che derivi da un comportamento umano facilmente prevedibile. Il Fabbricante, in quanto progettista e costruttore della macchina, è tenuto a conoscere tutte le modalità di interfacciamento (corrette o meno) dell’operatore con la macchina. Questo può derivare da una specifica valutazione durante la progettazione oppure più semplicemente dalla analisi del comportamento medio degli operatori su macchine simili.
Alcuni esempi di comportamenti umani scorretti, ma facilmente prevedibili da parte del Fabbricante che portano ad un utilizzo scorretto della macchina sono:
- manomissione dei dispositivi di protezione (per esempio, microinterruttori di sicurezza sui ripari mobili interbloccati), con il solo scopo di aumentare la produttività della macchina o semplificare le modalità di interfacciamento dell’operatore con la macchina;
- manomissione del circuito elettrico e/o di comando;
- perdita di controllo della macchina da parte dell’operatore (in particolare per le macchine mobili o a funzionamento manuale);
- reazione istintiva di una persona, in caso di guasto o malfunzionamento della macchina;
- comportamento derivante da mancanza di concentrazione.
Il Fabbricante, nella valutazione dei rischi, deve analizzare queste situazioni in cui si potrebbero presentare usi scorretti, ma ragionevolmente prevedibili, della macchina: le scelte progettuali devono sempre essere tali da soddisfare i requisiti della Direttiva Macchine e tali da rendere utilizzabile in sicurezza la macchina, garantendo la massima produttività possibile all’utilizzatore finale. A tal riguardo l’adozione delle soluzioni proposte dalle norme tecniche di riferimento, permette di ridurre la possibilità di uso scorretto da parte dell’utilizzatore. Per esempio, la norma UNI EN ISO 14119: 2013 fornisce indicazioni progettuali da adottare per evitare fenomeni di elusione dei microinterruttori di sicurezza sui ripari mobili.
Concludendo, possiamo dunque affermare che, insieme alle corrette scelte progettuali basate sulle norme tecniche armonizzate, l’indicazione nelle istruzioni per l’uso, in maniera chiara, di qual è l’uso previsto della macchina, quali materiali può lavorare, quale posizione deve occupare l’operatore durante la lavorazione, ecc. tutela il Fabbricante e lo stesso utilizzatore rispetto a quello che potrebbe essere un uso “improprio” e dunque scorretto della macchina stessa.
[A cura di: ing. Christian Trinastich per mtm consulting s.r.l.]
News
Nuovo Regolamento sui dispositivi di protezione individuale (DPI)
17/03/2015
A breve la Commissione Europea pubblicherà un nuovo Regolamento inerente i Dispositivi di Protezione Individuale che andrà a sostituire l’attuale Direttiva 89/686/CEE. A riguardo vi saranno una serie di importanti cambiamenti relativamente ai DPI oggetto della normativa, adeguando, nel contempo, il testo al nuovo quadro normativo europeo.
MTM Consulting s.r.l. è in grado di aiutare i Fabbricanti di DPI nel conformarsi alle indicazioni presenti nel nuovo Regolamento e i Datori di Lavoro nella scelta dei DPI idonei alle mansioni lavorative presenti nel proprio ambiente di lavoro, al fine di conformarsi alle richieste del Titolo III del D.Lgs. 81/2008 e s.m.i.
La direttiva 89/686/CEE sui dispositivi di protezione individuale (DPI) è stata adottata il 21 dicembre 1989 ed è pienamente applicabile dal 1º luglio 1995. Essa è stata tra le prime direttive a essere formulata secondo il Nuovo Approccio e disciplina la messa in circolazione nell’UE di dispositivi di protezione individuale (scarpe di sicurezza, indumenti di protezione, occhiali di protezione, tappi auricolari, ecc.). Questa direttiva, in definitiva, consente la libera circolazione in Europa dei DPI che rientrano nel suo campo di applicazione, garantendo al contempo un elevato livello di protezione degli utilizzatori.
Come per le altre direttive Nuovo Approccio, la direttiva sui DPI stabilisce i requisiti essenziali cui devono conformarsi i DPI prima di essere messi a disposizione sul mercato dell'UE. I fabbricanti devono apporre la marcatura CE sul prodotto e fornire agli utilizzatori istruzioni per l'uso, la pulizia, la conservazione, la manutenzione e la disinfezione dei DPI.
Nelle intenzioni della Commissione Europea vi è l’idea di sostituire questa direttiva ancora vigente con un Regolamento di prossima pubblicazione. Gli obiettivi generali di questa iniziativa sono: proteggere meglio la salute e la sicurezza degli utilizzatori dei DPI, garantire condizioni di concorrenza eque per gli operatori economici del settore nel mercato interno e semplificare il contesto regolamentare europeo in materia di DPI. Il nuovo Regolamento vuole modificare e chiarire alcune delle disposizioni della direttiva esistente e allinearle alle disposizioni della decisione n. 768/2008/CE relativa a un quadro comune per la commercializzazione dei prodotti.
La nuova forma giuridica scelta (Regolamento al posto di una Direttiva) che fa sì che il documento, una volta pubblicato sulla Gazzetta Ufficiale dell’Unione Europea, abbia una immediata validità in tutti gli Stati membri senza necessità di recepimento. L’aspetto sicuramente più importante che sarà oggetto di aggiornamento è il campo di applicazione del Regolamento: saranno inclusi anche i DPI contro umidità, acqua e calore (per esempio, i guanti da forno) per uso privato (gli stessi prodotti, per uso commerciale, erano già compresi). Un’altra importante novità è rappresentata dalla formulazione di definizioni e dalle nuove procedure di valutazione della conformità per i DPI su misura (identificati come “DPI fatti su misura”) e per i DPI sottoposti ad adeguamenti individuali (“DPI adattati singolarmente”). L'elenco dei prodotti oggetto della procedura di valutazione della conformità più severa è stato rivisto allo scopo di eliminare le incongruenze.
Il nuovo Regolamento contiene le disposizioni tipiche della normativa di armonizzazione dell'Unione relativa ai prodotti e stabilisce gli obblighi degli operatori economici interessati (fabbricanti, rappresentanti autorizzati, importatori e distributori), conformemente alla decisione n. 768/2008/CE relativa a un quadro comune per la commercializzazione dei prodotti. Il Regolamento CE obbliga i fabbricanti di DPI a redigere una documentazione tecnica e a garantire che i DPI siano accompagnati da una copia della dichiarazione di conformità UE o da una dichiarazione di conformità UE semplificata (con poche fondamentali informazioni e con il rimando a una pagina Internet dove è possibile visionare la dichiarazione di conformità completa). In questo senso il Regolamento inerente i DPI si allinea alle direttive europee di ultima pubblicazione in cui le responsabilità dei diversi soggetti coinvolti sono chiaramente evidenziate.
La proposta semplifica la definizione delle categorie di DPI: la categoria dipende esclusivamente dal rischio da cui il DPI vuole proteggere. I rischi che rientrano in ciascuna categoria sono indicati nell'allegato I. I DPI fatti su misura sono definiti sempre come categoria II. Le procedure di valutazione della conformità da seguire, come riportate dal Regolamento, dipendono dalla categoria di DPI.
La nuova normativa modifica la categoria di alcuni tipi di DPI rispetto alla direttiva 89/686/CEE. I DPI destinati a proteggere l'utilizzatore dall'annegamento, dai tagli da seghe a catena portatili, dai tagli da getti d'acqua ad alta pressione, dalle ferite da proiettile o da coltello e dal rumore nocivo sono elencati nella categoria III e sono dunque oggetto della procedura di valutazione di conformità più severa. Per quanto invece riguarda le procedure di valutazione della conformità, esse rimangono inalterate rispetto alla attuale direttiva 89/686/CEE.
Il nuovo Regolamento sarà applicabile due anni dopo la sua entrata in vigore al fine di dar tempo a fabbricanti, organismi notificati e Stati membri di adeguarsi alle nuove prescrizioni. Sono previste disposizioni transitorie per i prodotti fabbricati e i certificati rilasciati dagli organismi notificati a norma della direttiva 89/686/CEE, in modo da consentire l’esaurimento delle scorte e agevolare il passaggio alle disposizioni del nuovo Regolamento.
[A cura di: ing. Christian Trinastich per mtm consulting s.r.l.]
-
News
Parti del sistema di comando legate alla sicurezza: una nuova norma supererà a breve le attuali EN ISO 13849 e IEC 62061
09/03/2015
Due importanti norme inerenti la progettazione delle parti del sistema di comando legate alla sicurezza, EN ISO 13849 e IEC 62061, a breve saranno accorpate. Cosa significa questo per i costruttori di macchine? A riguardo è da considerare come la Direttiva Macchine 2006/42/CE definisca i requisiti che deve rispettare il sistema di comando della macchina in modo da evitare l’insorgere di situazioni pericolose. La conoscenza di tali norme tecniche è dunque fondamentale.
MTM Consulting s.r.l. è in grado di aiutare i Fabbricanti di macchine e impianti nell’analisi delle normative inerenti la progettazione delle parti dei sistemi di comando, anche legate alla sicurezza e quindi di realizzare la conseguente valutazione dei rischi necessaria a dimostrare la conformità del progetto alle richieste della Direttiva.
Il fabbricante della macchina ha l’obbligo di realizzare una valutazione dei rischi con lo scopo di dimostrare la conformità della propria macchina ai requisiti essenziali della Direttiva Macchine 2006/42/CE. Tale valutazione dei rischi deve coprire anche le scelte progettuali legate all’equipaggiamento del sistema di comando della macchina, in particolare per quanto attiene a quelle parti del sistema di comando legate alla sicurezza. Infatti, il requisito 1.2.1 dell’Allegato I –“Sicurezza ed affidabilità dei sistemi di comando”-, definisce i requisiti che deve rispettare il sistema di comando della macchina al fine di evitare l’insorgenza di situazioni pericolose. A riguardo, è da ricordare che la sicurezza della macchina deriva anche dalla idonea progettazione del sistema di comando legato alle funzioni di sicurezza della macchina (avvio, arresto, arresto di emergenza, ecc.). Pertanto, una progettazione dei sistemi di comando della macchina che non sia conforme a quanto richiede la direttiva, potrebbe comportare il verificarsi di una serie di situazioni di pericolo “indirette”, dovute proprio ad un guasto e/o cattivo funzionamento di tali sistemi di comando.
Oggigiorno, per conformarsi a quanto richiesto dalla Direttiva Macchine a riguardo è possibile riferirsi a due distinte norme tecniche: EN ISO 13849 e IEC 62061. Le due norme, pur con le loro differenze, forniscono un criterio per la scelta dei componenti e la progettazione delle parti del sistema di comando legate alle sicurezza. Tutti i componenti del sistema di comando sono soggetti a guasti e/o rotture, pertanto è impensabile immaginare di progettare un sistema di comando che non vada mai a guasto. E’ ragionevole però pensare di poter selezionare le parti del sistema di comando legate alla sicurezza in modo tale da realizzare un sistema che sia sufficientemente sicuro e affidabile rispetto alle situazioni pericolose da cui è necessario proteggere l’operatore, come evidenziate dalla valutazione dei rischi. Quindi, per ogni funzione di sicurezza individuata, se secondo la norma EN ISO 13849 si parla di garantire un definito livello di affidabilità (Perfomance Level), secondo la norma IEC 62061 si parla di confermare un definito livello di integrità della sicurezza (SIL). In particolare, la norma IEC 62061 è specificatamente scritta per garantire la sicurezza funzionale dei sistemi elettrici / elettronici / elettronici programmabili relativi alla sicurezza.
Di fatto, le due norme, pur con strade differenti, portano spesso allo stesso risultato, sebbene con esiti differenti. Al fine di semplificare il processo di analisi, le due norme saranno a breve unificate in una nuova norma, IEC/ISO 17305 entro il 2016. Anche se l’adozione è fissata per il 2016, sono previsti due anni di transizione, fino al 2018, e gli organismi normativi potrebbero necessitare di altro tempo per definire nei dettagli la norma IEC/ISO 17305. La data di entrata in vigore, dunque, è al momento ancora in via di definizione.
La metodologia di base e i requisiti essenziali introdotti nelle norme EN ISO 13849 e IEC 62061 dovrebbero restare inalterati. L’idea che sta alla base della unificazione di tali norme è quello di creare un’unica norma di più facile utilizzo eliminando alcune criticità identificate durante gli anni di utilizzo delle due norme attuali. Un ulteriore motivo che porta alla necessità di effettuare questa fusione è quello di garantire una migliore circolazione delle merci a livello mondiale. Come già successo per la norma ISO 12100 inerente i principi generali per la progettazione, analisi e valutazione dei rischi, la realizzazione di una norma considerata lo stato dell’arte in buona parte del mondo è fondamentale per garantire la circolazione dei prodotti.
In tutto il mondo, un sempre maggior numero di Paesi sta adottando le norme ISO e IEC come norme nazionali. Le differenti norme di riferimento (per esempio, UL, ANSI, EN, GB) forniscono indicazioni tecniche e criteri di progettazione che complicano l’attività di esportatori e importatori in quanto sono norme che si applicano in specifici continenti o addirittura singoli paesi. Tuttavia queste norme sono spesso simili alle norme ISO e IEC. Pertanto, la definizione di un’unica norma che specifichi i criteri di progettazione delle parti del sistema di comando legate alla sicurezza garantirà uniformità in tutto il mondo per quanto attiene a questi aspetti di progettazione.
Fino alla data di entrata in vigore della nuova norma IEC/ISO 17305 è, dunque, necessario applicare le norme EN ISO 13849 e IEC 62061. Le aziende che già conoscono e applicano al proprio processo di progettazione queste due norme non avranno molto probabilmente problemi con la nuova norma unificata.
[A cura di: ing. Christian Trinastich per mtm consulting s.r.l.]